As the boundaries of what is possible are pushed in the aerospace sector, engineers are faced with an intractable problem – how to stay in control.
Flight control systems are fundamental to all types of air and space vehicles, so the testing of controls is one of the most important aspects of flight testing. A spacecraft at the Moon or an aircraft traveling at hypersonic speeds of Mach 5+ is of limited use if it cannot be controlled.
The development of flight control systems then mirrors and enables advances in other areas of aerospace such as propulsion and aerodynamics. Furthermore, while traditionally based on mechanical and hydraulic systems, electro-mechanical actuation now provides lighter and smaller systems that require electrical and digital expertise to implement.
Hypersonic control
One of the leading examples of control at the extremes of flight is California, USA-based Stratolaunch’s program to develop a reusable hypersonic testbed, Talon-A (TA-1). Once operational, this rocket-powered Mach 5+ aircraft will carry customized experiments and fly a variety of hypersonic flight profiles.
TA-1 is air-launched from under the center of carrier aircraft Roc’s wing. Roc is the world’s largest flying aircraft and has a wingspan of 385ft (117m). A key feature of TA-1 is that it lands – the test vehicle must be reusable so it can reduce the cost and time needed to develop hypersonic aircraft and missiles. TA-1’s first user will be the US Air Force.
It is difficult to imagine a more complex flight control task than releasing from a moving carrier aircraft, firing a rocket-based propulsion system to produce Mach 5+ speeds and then gliding to land. Stratolaunch recruited US aerospace technology development stalwart Draper to help with the task in 2020.
Draper traces its hypersonic guidance, navigation and control (GNC) capability back to providing the guidance computer for NASA’s Apollo missions and through the Space Shuttle program. Its GNC software is an integral part of the overall flight control software for Talon-A.
Brandon Jalbert, program manager in Draper’s Space Systems office, says, “There are lots of similarities between Talon and vehicles when they are re-entering the Earth’s atmosphere.
“But the main difference is that Talon has to get up to altitude and speed. Our algorithms control the vehicle after it gets dropped from Roc, starting with its boost guidance.
“Then once the engine cuts out Talon-A glides along the flight trajectory. Approach and landing algorithms provide the safe landing or splashdown depending on the case.”
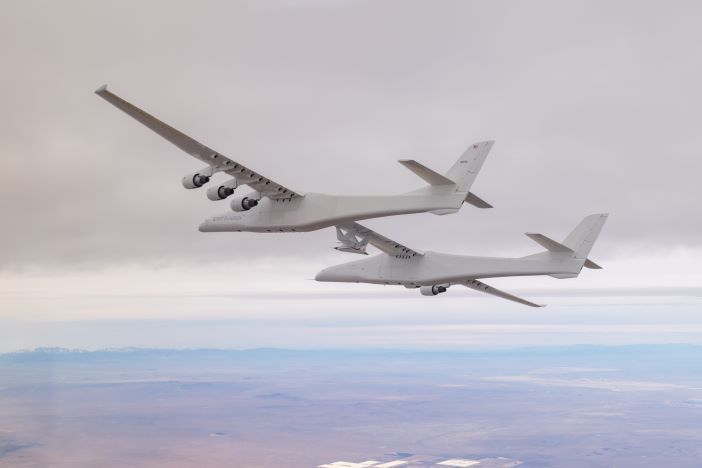
Dan Gallton, director of space navigation and in-space servicing, assembly and manufacturing for Draper’s Space Systems program office says, “It is a challenging environment in the upper atmosphere. It is very turbulent and complex, there are higher temperatures and pressures with hypersonic flight and a lot of varying densities of different particle populations that create a dynamic flight environment.
“The GNC is constantly adjusting. Quick executable command decisions have to be made by the software to maintain the flight profile and not lose the vehicle.”
Draper engineers have leveraged GNC algorithms from legacy programs but have also devised new ones for Talon-A. The GNC must be able to quickly adapt to the rapidly changing environment according to the phase of the flight. “Vehicles that go through transonic, supersonic, hypersonic and above require a higher rate of control,” says Jalbert.
“The software must be accurate, running at the appropriate rates, and be computationally efficient. You need robust hardware for these environments, which may mean sacrificing processor performance. Things that run on a desktop computer might not necessarily run on the target processor,” says Jalbert.
The trajectories of a hypersonic vehicle are different than a spacecraft re-entering the atmosphere, which increases the complexity of the GNC algorithms. Talon is a test platform and will carry different materials and systems to test them at hypersonic speeds. This adds another layer of complexity to the flight dynamics.
Simulation and validation
Simulated testing of the GNC software’s performance at hypersonic speeds is challenging because so little is known about the domain, especially with a new vehicle such as TA-1. Draper’s team worked closely with Stratolaunch on the models used for development, on the ground test campaign and on the captive-carry test campaign to ensure proper validation.
Jalbert says, “The initial models had unknowns and assumptions that as Stratolaunch has progressed through testing we have had the data to resolve.
“When we went back and looked, there were some conditions that were a bit off from what we initially expected, but once we corrected our simulation for the flight conditions, we found that our models were very accurate in predicting the flight performance.”
The flight test campaigns are therefore integral to developing a working GNC. Gallton says, “We have a lot of experience in legacy hypersonic. The test campaign is about burning down technology risk and minimizing the uncertainties. But we still learn something new every time we develop a GNC system.”
Learnings from the Talon program will be reused in future projects, which may include a return to space missions. Jalbert says, “As we look to push to the Moon, Mars and beyond we must answer these types of questions about guidance, navigation and control. It’s an exciting time for this type of work.
“Talon flights are now another application that Draper’s GNC is flight-proven for. We can reuse those for other applications, take what we learned from Talon and apply it to new applications with similar dynamics and control problems.”
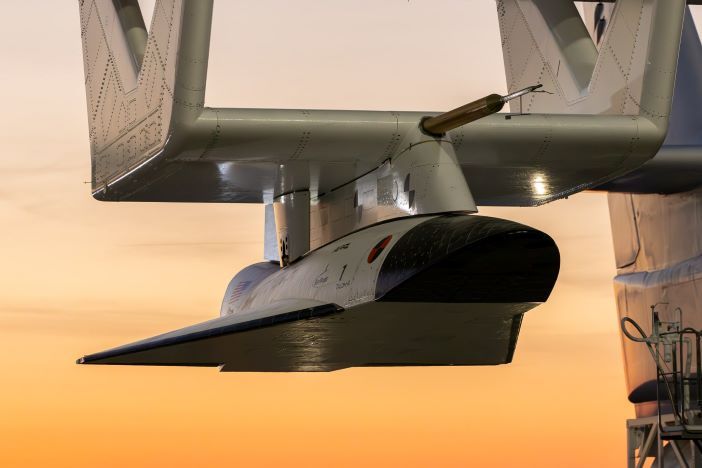
Easier space access
Another challenging area for flight control systems is rocket launches. Startup Aurora Avionics in Edinburgh, Scotland is developing technology to make it easier. Rowland Fraser is chief technical officer at the company, which he founded last year with Oren Smith-Carpenter to make a universal control system for rockets. Aurora Avionics has so far secured funding from the European Space Agency, private investors and the Scottish Government.
Fraser was working alongside Smith at Scottish launch vehicle company Orbex on avionics on flight control systems for the company’s Prime rocket when they spotted an opportunity: “What became clear to us was the limitations being enforced by the lack of commercial-off-the-shelf components for the avionics. It was causing us to repeat the disadvantages of iterative development, and we realized it must be a similar situation for all launch vehicle developers.”
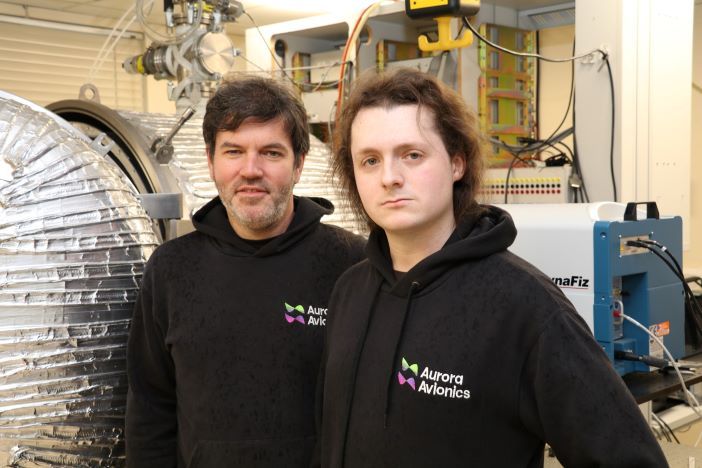
Without COTS equipment available, rocket-makers must develop onboard computers (OBCs) and related ground equipment in-house on an ad hoc basis. This lack of standardization directs time and man hours into work that will have been done somewhere else before.
Fraser and Smith realized that a standardized modular platform for the OBC using FPGAs (field Programmable Gate Arrays), which could be adapted for any launch system – available off the shelf – could save time and money. It would stop engineers from having to repeat the typical development and testing required during a launch vehicle development program.
A rocket’s OBC includes the GNC, high-level controllers for the fuel tanks and propulsion controls. The OBC must be able to withstand the harsh experience of a launch and the environment of space.
Aurora’s modular suite of electronic components will make a unified OBC that can control launch vehicles – a kind of rocket equivalent to the Bosch engine management systems found in many cars.
“Most companies will use closed microcontrollers to deploy an OBC, but the software used during development phases is typically rewritten many times, adding to the qualification time and cost,” says Fraser.
“Using FPGAs and ASICs [Application-specific integrated circuits] allows us to have custom firmware for critical control and processing functions that need precise timing and completely deterministic operation. Then you can get on with developing the software.”
Aurora does closed-loop testing using data generated by simulation which is continuously integrated into the model. They are working with a university to develop a hardware-in-the-loop emulator, which will do the job of the simulator. Launch vehicle developers will also send instrumentation details and data so that the GNC part of the OBC can be tailored for their use.
Functional testing is being done to meet specifications, which are validated using ground and flight testing. Fraser says, “We will validate using hundreds of hours of testing with engineering models then qualify for flight. We plan to have developed the engineering models by the end of this year, the flight models by the end of next year and to start hot fire testing in 2026.
“The volume of launches now means a standardized-COTS solution for OBC is commercially viable and technically possible. We are engaged with five launch vehicle companies, which are feeding us requirements.”
While the increasing complexity in flight control systems demanded from by the aviation and space industries drives advances, a combination of experience and new technologies is enabling engineers and pilots to stay in control and push the boundaries of flight further.
Flight controls evolve for eVTOL and eSTOL aircraft
Flight control systems pose major challenge for developers of eVTOL aircraft and eSTOL (electrical short take-off and landing). Most of these aircraft designs are novel and many employ distributed electric propulsion (DEP), where multiple propulsors are placed at various locations on an airframe, to create lift and thrust in different ways.
Electra’s hybrid-electric eSTOL aircraft is a leading example of this. The aircraft uses a relatively underused aerodynamic concept called blown-lift, enabled by DEP to shorten the amount of runway it needs to take off and land to 150ft (45m).
In July Electra announced Honeywell will be supplying the flight control computers and electromechanical actuation systems for its aircraft. Honeywell is also investing in Electra.
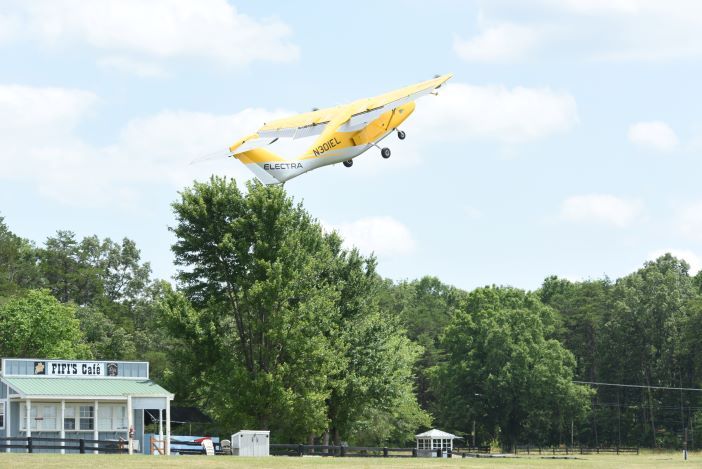
“Honeywell brings deep expertise in control system design, development and certification to support Electra’s goal of creating sustainable, efficient and accessible air travel,” said JP Stewart, vice president and general manager, Electra.
Honeywell’s compact fly-by-wire (cFBW) flight control computers are augmented by electronics, rather than manual controls. The computer is around the size of a paperback book. Honeywell says its cFBW computer draws less power, helps reduce turbulence, and can dynamically adjust flight motors to enable smooth flight paths, eliminating the need for heavy hydraulics and control cables.
Its electromechanical actuation systems take commands from the pilot or onboard flight management system and enable actions like moving the flaps on the wing.