Digitalization is revolutionizing many industries, driving down costs, speeding up projects and helping to increase innovation. Companies in the aerospace sector are becoming aware of how a more digitized approach to programs can result in positive changes.
It is why there is a huge interest in digital twin technology. A digital twin is a virtual representation of real-world entities and processes, synchronized at a specified frequency and fidelity – allowing an infinite amount of testing to run without the cost and time involved in more traditional approaches.
The technology can be used to recreate digital versions of entire aircraft, specific sub-sections or even individual components to better understand them.
The race to push the boundaries of what digital twin technology can achieve is pulling in research universities and the some of the largest companies in aerospace. Huge investments are being made across the world to develop digital tools and processes that can deliver the next advances in aerospace technology more efficiently and effectively.
Accelerated programs
In the UK, Digital Catapult is part of the Digital Twin Consortium that is working to create the UK Digital Twin Centre in Belfast, Northern Ireland. The Digital Twin Centre is due to open its doors in early 2025. The program is receiving £37.6 million (US$47.5 million) of funds from regional and national governments, with co-investment from Thales UK, Spirit AeroSystems and Artemis Technologies.
Steven Wood, head of aerospace, defence and security at Digital Catapult says, “The development of the Digital Twin Centre isn’t just for aerospace, but we see aerospace as being the driving force behind it. It is a national facility to make UK industry more competitive,” he says.
When it’s operational the Digital Twin Centre will help drive forward the use of the technology, and build on the work that is already taking place in the aerospace sector.
“We have already seen quite a few examples of digital twins. Rolls-Royce has done a lot of pioneering work creating simulated models of their latest engines,” says Wood. “Some large aerospace OEMs have even modelled every physical system of an aircraft in a way that mimics the physical world as closely as possible.
“They have created a test rig for a physical system, for example the actuators on a modern fighter jet, and then created a digital twin of those actuators. They have operated them side by side and measured the response and performance of each, and then narrowed that gap as much as possible so that the digital twin behaves exactly like the physical equivalent.”
This kind of approach could help aerospace companies improve the way they operate, impacting everything from innovation to manufacturing, speed of development and maintenance.
“When you are developing a product, traditionally you are building prototype versions of the product itself and every one of its systems. But as these things become more sophisticated the time it takes to develop them increases. You’ve seen some projects like the F-35, take much longer than they should have done,” says Wood.
It is projects like these that Wood believes digital twins will have a transformative effect on.
“What if a development stage doesn’t need to have a physical realization and a twin can be tested and stressed and shown to be fit for purpose in a digital environment?” he says.
It is a perhaps obvious but logical use. Each time a physical system doesn’t have to be created a significant amount of time and resources can be saved. When integrated systems or an entire aircraft are being tested in the real world, the process takes a long time. Digital twins can help reduce the number of prototypes needed. That also means reducing the amount of prototype tooling too.
“It adds up to a significant saving in both time and cost – for the client and for the company making it,” says Wood.
There are already important programs the technology could be used on. The use of digital twins could help the Global Combat Air Programme – the UK, Italy and Japan’s shared endeavor to develop a next generation fighter aircraft – to reduce the time and cost of the project by half according to Wood.
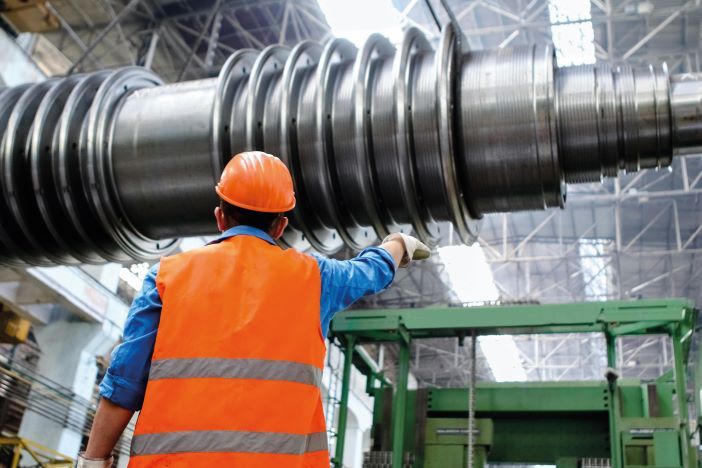
Manufacturing efficiencies
Siemens Digital Industries Software is committed to driving digital twin technology’s integration into aerospace programs. It is supplying its Siemens Xcelerator portfolio of industry software to US aerospace startup Natilus.
As part of the collaboration Natilus has used Siemens’ NX immersive designer to combine the real and digital worlds using a Sony XR Head Mounted Display. Natilus has used the technology to take a model from a 2D screen to a full-scale 85ft (26m) wingspan immersive digital twin that is viewed inside a hangar.
But Siemens does not only see digital twins as a tool for development programs. The company believes the technology can be a key part of making sure that once an aircraft, or its components and parts enter production they meet the stringent requirements needed by the aviation industry.
Siemens Digital Industries Software’s vice-president for aerospace and defence, Todd Tuthill says, “Digital twins become even more powerful in manufacturing. I can understand what the most efficient way to build a factory is by building a digital twin.
“They can help me to understand what machine I should purchase and figure out the most efficient way to move products through the factory.”
Once up and running there are also benefits. According to Tuthill you can continuously feed data from the factory floor into a digital twin to help streamline processes, improve efficiencies and overcome issues including machine downtime and supply chain problems.
“You could run all those what if scenarios on the digital twin and then take them out and implement them in the factory. So, digital twins can make the process of manufacturing much easier and improve efficiency,” says Tuthill.
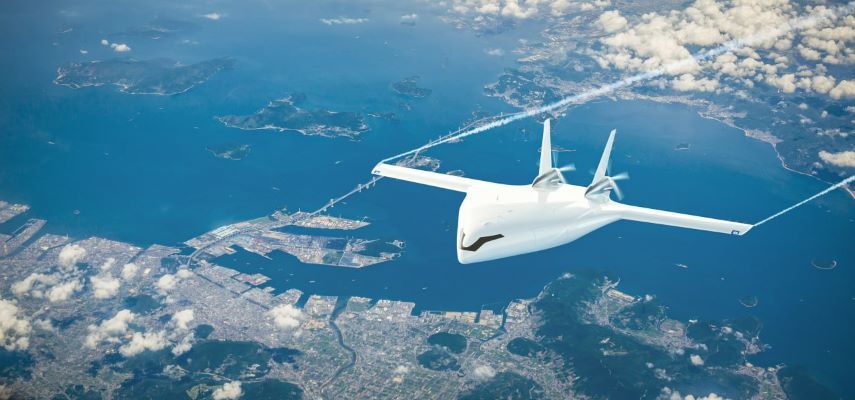
Maintenance targets
Aerospace is becoming increasingly focused on its environmental responsibilities too. New forms of propulsion could help it meet targets, and digital twins will play an increasingly important role.
The University of Nottingham in the UK has recently signed a memorandum of understanding with simulation company Altair to help it develop a digital twin to rapidly design, validate and test electric propulsion systems in aircraft and advanced air mobility vehicles.
While there are many challenges to overcome before electric powertrains are commonly used by aircraft, researchers at the University of Nottingham are already considering how digital twins can help improve electrified powertrains once they enter service.
Tao Yang, professor of aerospace electrical systems at the University of Nottingham says, “For future electric or hybrid-electric aircraft there is a large energy storage requirement. And with batteries we can help predict the maintenance schedule with digital twins.”
Existing propulsion systems are maintained to a set schedule and engineers physically inspect different components. However, batteries and motors are closed systems, so as Yang says, you cannot open them up in the same way to see how the copper is behaving.
Yang sees twins as linked by a thread between the ,physical and digital twins that carries data. When more data is constantly being fed into the system it should be able to better predict when there could be an issue – with a motor or a battery – and recommend preventative maintenance.
Predictive future
Digital twins could help remove the guess work sometimes involved with an aircraft’s operational life, especially when linked to artificial intelligence. Startup PhysicsX is building artificial intelligence models for accurate physics simulation. The AI models enable a generative engineering technique that help to accelerate time-consuming activities and streamline engineering processes.
Neil Cameron, principal engineer at PhysicsX says, “We train AI to predict the outcome of a digital twin simulation rather than running the base simulation. The AI provides answers that are the almost the exact equivalent of traditional testing methods, but in less than a second.”
This machine learning approach can be used to predict the output of anything from a component’s drag to its life expectancy. The technique is not theoretical, PhysicsX has already put the AI-powered technology into practice. It is working with a company that produces aero gas turbines. Use of the technology has helped to significantly reduce wastage in certain parts of the manufacturing process.
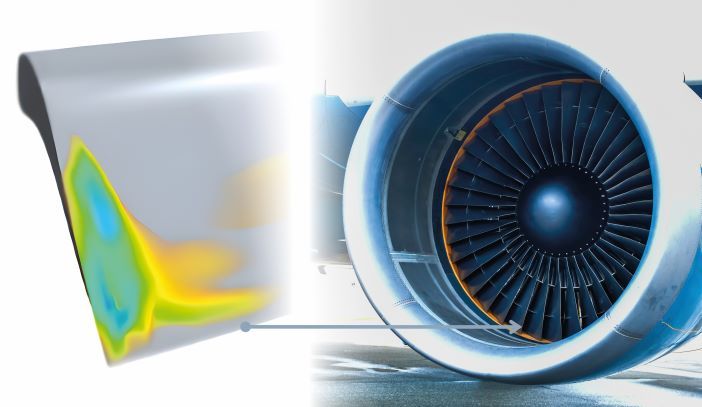
“The company was putting 30,000 parts per year into quarantine for further work to decide if they were any good,” says Cameron.
“Essentially, they were taking each [turbine] blade with its complex shape, 3D scanning it and comparing the scan to their model.” If it was out of tolerance the blade would be scrapped.
“The digital twin work we did essentially modeled how much air a given shape of blade transports through the engine,” says Cameron.
“If you get a blade out of tolerance, the answer the customer really needed was, how much air is it going to move? Am I going to be 10% down, 5% down, or is it going to be an insignificant amount?”
PhysicsX trained an AI-based model to predict the lift and drag of a blade. Key was that the system didn’t take hours to run, instead, they were getting answers in seconds.
“Something comes off the line, they scan it, they see it’s out of tolerance. They can then answer the question, what would the performance be if we integrated this into a gas turbine,” says Cameron. “They found that there was a much more nuanced picture, and tolerance was more about performance than about a geometric measurement.”
Digital twins are receiving a huge amount of attention, and importantly investment. The UK Digital Twin Centre based in Belfast will be joined by another center being created at the University of Nottingham – and no doubt far more in the UK. But there is also investment in the USA by big players including Lockheed Martin. And at some point it is hoped that different centres could speak with one another and collaborate.
Fully integrated into the aerospace sector, digital twin technology could help drive innovation, reduce costs and speed up programs, from initial concept phase, all the way through to continuous maintenance. It could be an incredible shift for an industry that has often suffered from program delays and constantly expanding budgets in the past.