The news that Airbus is to scale back its ZEROe hydrogen aircraft development program was received with a mix of dismay and lack of surprise by most in the sector. The ZEROe program was launched in 2020 and aimed to put a hydrogen-propulsion aircraft into service by 2035. Instead, there won’t be an Airbus hydrogen-electric aircraft flying until 2045, and the number of engineers working on hydrogen R&D globally is being slashed.
Speaking at the company’s 2024 financial results event last month, Airbus CEO Guillaume Faury blamed the cutbacks and delay on the shared lack of progress in developing a hydrogen ecosystem – fuel production plants and transmission infrastructure. Essentially, Airbus now believes hydrogen fuel won’t be available at airports in 2035, making a hydrogen-fuelled aircraft commercially unviable.
Faury defended the R&D done so far, stressing that a hydrogen-fuel cell powertrain is technically feasible and the best way to achieve a zero-emissions aircraft. Indeed, work on the “critical technologies”, such as fuel cells and cryogenic systems will continue.
But Faury also admitted that an eventual hydrogen fuel cell-powered aircraft could look very different from the ZEROe concepts publicized over the last five years. “The aircraft must make sense in terms of size, range and passenger capacity for between 2035 and 2045. We must look at the complete equation,” he said.
Small wins
The industry knows that hydrogen fuel cells can power aircraft, arguably most credibly thanks to flight testing achieved by German startup H2FLY of its four-seat HY4 demonstrator in September 2023. The aircraft flew at altitudes of up to 7,200ft and its longest flight lasted three hours. A modified Pipistrel light aircraft, HY4 is powered by cryogenic liquid hydrogen, which can give range and performance equal to fossil fuels minus the carbon emissions.
H2FLY was acquired by US eVTOL aircraft developer Joby in 2021. Parts of H2FLY’s propulsion system are being tested in Joby’s eVTOL. H2FLY also continues to develop its H2F-175 fuel cell propulsion system, which can output 175kW of power.
Josef Kallo, now chief technology officer at H2FLY agrees the largest barrier to using hydrogen in aviation is its production and distribution. “The main challenge for hydrogen aviation is to build the infrastructure to ensure a reliable and cost-competitive supply of hydrogen.
“Developing a comprehensive hydrogen ecosystem will require significant investment, particularly in renewable energy for green hydrogen production and specialized airport refueling infrastructure. This includes the development of storage and distribution networks to support hydrogen-powered aircraft.
“While it’s difficult to predict the exact impact of Airbus’ decision to scale back its hydrogen R&D efforts, we continue to believe in hydrogen as an aviation fuel and are fully committed to contributing to the development of a hydrogen ecosystem, starting with smaller electric aircraft.”
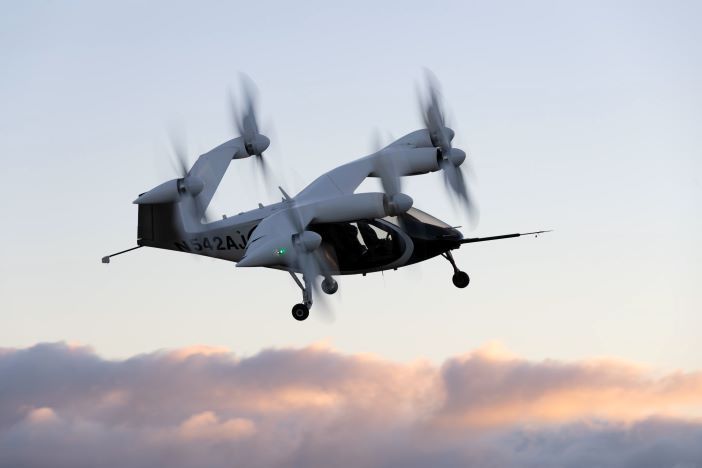
Realistic readjustment
The most important part of any hydrogen-electric aircraft is the fuel cell. UK-based Intelligent Energy already supplies hydrogen fuel cell systems to the automotive, telecoms and construction sectors. Founded in 2001 and with a workforce today of around 200 people, the company also worked with Boeing to build and fly the world’s first fuel cell-powered aircraft in 2008. Jonathon Douglas-Smith, head of aerospace sales at Intelligent Energy believes most people in the industry were expecting Airbus to scale back its hydrogen ambitions: “Airbus were trailblazers with ZEROe. But it is too large of an undertaking for them to do it all themselves,” he says.
“We don’t think it damages the route to market for hydrogen aircraft, it is a realignment that will allow suppliers to help Airbus make it happen.”
Intelligent Energy has developed an aviation fuel cell as part of the UK Government-funded £54 million (US$68 million) H2GEAR project. The 300kW capable fuel cell system was launched to the market in July 2024 at the Farnborough Airshow. The IE-FLIGHT 300 (F300) is for Part 23 aircraft with up to 19 seats and eVTOLs. The first OEM customers are expected to be announced soon, with the first deliveries planned for 2027.
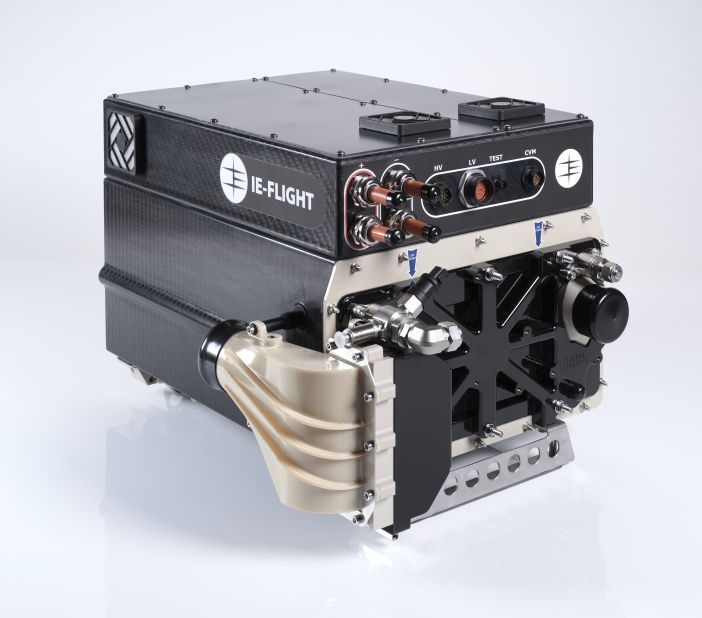
During the next two and half years, engineers at Intelligent Energy will develop the balance of plant for the F300. This includes the ancillary parts of the system such as the heat exchanger, air compressor, and hydrogen recirculation module.
Douglas-Smith says, “The market wants a more complete balance of plant with the fuel cell system because it removes the customer’s need to understand the complexities of how to run fuel cells optimally. We have 24 years of experience building fuel cell systems, so it makes sense for us to do it.”
Intelligent Energy is also developing the larger F500 fuel cell system based on the same underlying lightweight fuel cell stack technology for aircraft larger than 19 seats. “Scaling up is part of our roadmap,” says Douglas-Smith. “Larger aircraft need a higher specific power and more time is needed to develop the technology for those power densities. We have R&D programs that are looking at the technology.
“But we see larger aircraft as a longer-term market,” he says. “The market for smaller aircraft will be a lot sooner, towards the end of this decade, rather than the 2040-45 timeframe for fuel cell powered aircraft greater than 100 seats.”
Fuel cell competition
Intelligent Energy has invested heavily and made good progress with its aviation fuel cell, underlining its belief in the market. Other companies, such as Sweden’s Powercell are also betting on fuel cells for aviation applications. Having supplied the fuel cells for its prototypes, Powercell is supplying the stacks for ZeroAvia’s first 600kW powertrain (ZA600), which is also intended for use in Part 23 aircraft.
The two companies are also partnering on the R&D for the more powerful ZA2000 powertrain, which is aimed at turboprop aircraft of up to 80 seats and will be based on Powercell’s heavy-duty fuel cell stack design. Powercell is also supplying its 300kW HDS300 (heavy duty system) fuel cell stack and engineering support for an 18-month aviation project in Japan.
Meanwhile, German automotive supplier ElringKlinger’s aviation fuel cell technology has been licensed by Airbus and is being developed as part of a joint venture company called Aerostack. Its proton exchange membrane (PEM) fuel cell is based on ElringKlinger’s NM12 stack, which provides a maximum output of 205kW. The fuel cells were used in a successful ground test of a 1.2MW powertrain last January in Ottobrunn, Germany.
“Airbus has acknowledged that essential hydrogen fuel cell component technology is going to take longer than they anticipated to reach the performance levels needed for the 100-seater aircraft,” says Douglas-Smith. “I would confidently say that Intelligent Energy is a world leader in this field. But there is a long way to go – the regulations and conformity to airworthiness standards are still being written by EASA and the FAA – although roadmaps were published by both regulators last year.”
Heat dissipation
The H2GEAR project developed Intelligent Energy’s stack technology to TRL 5. One of the biggest challenges the company has encountered with developing fuel cells for use in aviation is the high-altitude environment.
“We tested the stack module in representative conditions of operating altitudes in barometric chambers. The stack was designed to specifically withstand the pressure differentials that can be expected at altitude. The seals were a key part of the design,” says Douglas-Smith.
“The air is less dense at altitude, making cooling harder. We see this already with our products for our drone customers, who use lower powered cells featuring air-cooling. Our patented evaporative cooling system is more thermally effective and the best way to get the heat out of the stack.”

Fuel cells are 50% efficient over life. A fuel cell delivering 100kW of power produces 100kW of heat which needs to be dissipated. The Flight F300’s evaporative cooling system injects deionized water into the very hot stack, which evaporates. Heat is transferred through vaporization, which is a more effective way of removing heat from the cells than liquid cooling.
Crucially for aviation applications, the increased effectiveness of evaporative cooling enables the thermal management system to be smaller and lighter. Injecting water directly also humidifies it, which optimizes the performance and lifetime of the stack.
Now-defunct hydrogen aviation startup Universal Hydrogen used USA company PlugPower’s automotive fuel cell for its testing program, integrating a system into the nacelle of a Dash 8 aircraft. Experts were quick to see the cooling challenges that had been encountered by the Universal Hydrogen team. “They needed really large air scoops and radiators, adding weight and drag. It became obvious it wasn’t a viable solution to go to market with,” says Douglas-Smith.
“That was one of the motivations for us to develop the F300, which beyond the evaporatively cooled technology, has a high temperature that can further shrink the thermal management and nacelle packaging. That’s one of the core development activities now.”
Other on-aircraft challenges
Thermal issues are not the only concern when integrating a hydrogen-electric fuel cell powertrain into an aircraft. Dr Craig Lawson is a reader in airframe systems at Cranfield University. Last month ground was broken on the University’s £69 million (US$87 million) Hydrogen Integration Incubator (CH2i) project, which will be one of the largest hydrogen R&D facilities in Europe.
Lawson says, “The introduction of hydrogen is so radical it will likely be done incrementally and at first sub-optimally. One of the big issues is storage volume.
“With a tube and wing design, you can’t put hydrogen fuel in the wings because they are too thin. We need cylindrical, ideally spherical tanks. You can put them in the fuselage, but then you are compromising on passenger space and payload,” says Lawson.
According to Lawson studies looking at modifying existing aircraft with hydrogen fuel systems have concluded the result will be aircraft with inferior payload and range capabilities compared to current models. “We are going to have to accept a hit on payload and range to have a zero-carbon aircraft,” he says.
In addition, a change in energy carrier means massive changes to certification and regulations. The safety case for hydrogen as an aviation fuel is yet to be fully explored.
“We understand the failure modes of kerosene, so it’s OK to have it relatively near an aircraft’s occupants. But it’s not clear that the failure mode of a hydrogen tank is going to be anything other than catastrophic,” says Lawson.
“That means to some people, if the hydrogen is within the same fuselage as the occupants, the aircraft is uncertifiable because any failure is going to be catastrophic.”
Hydrogen could be stored on tanks mounted on wings, but again this is a sub-optimal solution. Alternatively in a blended wing body (BWB) aircraft, which features a lot of storage volume, the hydrogen tanks could be placed outboard of the passengers.
“BWB is probably the best solution for a hydrogen airliner,” says Lawson.
BWB is an immature design, although studies have shown it to be efficient for large-capacity aircraft, no matter what the energy carrier. However, interest is growing in BWB, thanks to the push towards hydrogen as a fuel. California, USA-based startup JetZero plans to start flight testing a full-scale BWB aircraft in 2027. “There’s research coming in Europe and our Exaelia project has just started, looking at long-range, A350 replacements – green airliners,” says Lawson.
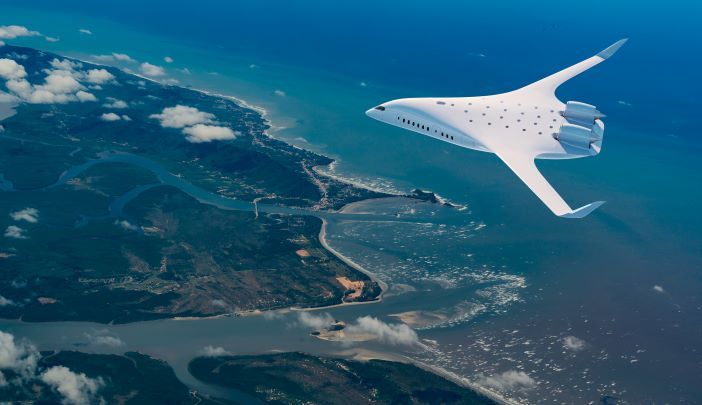
Power distribution systems
GKN Aerospace heads up the H2GEAR program, which started in 2020 and concludes in September. H2GEAR aims to develop a liquid hydrogen propulsion system for sub-regional aircraft that can be scaled up to larger aircraft. It is the largest single program ever awarded by UK funding body the Aerospace Technology Institute (ATI). As well as fuel cell company Intelligent Energy, partners include turbocompressor company Aeristech and several research universities.
H2GEAR is now reaching its demonstration and testing phase. ATI has awarded GKN other hydrogen research programs, including the £40 million, four-year HyFIVE program, which focuses on liquid hydrogen storage and fuel conditioning systems, and the £44 million H2FlyGHT, a follow-on to H2GEAR.
H2FlyGHT aims to demonstrate a 2MW hydrogen-electric propulsion system in flight by the end of the decade. Partners include: Parker Meggitt, which will be collaborating on thermal management and balance of plant for the fuel cell system; the University of Manchester, which will focus on the motor coil design and the University of Nottingham, where researchers will support the full motor design and scale-up and cryogenic inverter technology development.
Mike Hales is the chief engineer of hydrogen propulsion at GKN Aerospace and has been working on the H2GEAR project. He says, “At its heart, we are building an energy conversion system – liquid hydrogen is converted into DC power via a fuel cell, then distributed around the aircraft and provides the propulsion power.
“It’s converted to AC power in an inverter located next to the electrical machine, which converts that into torque to run the propulsor. The powertrain would be similar if you were using GH2 as a fuel source, but the H2GEAR architecture with an LH2 fuel source provides some preferential technical features.”
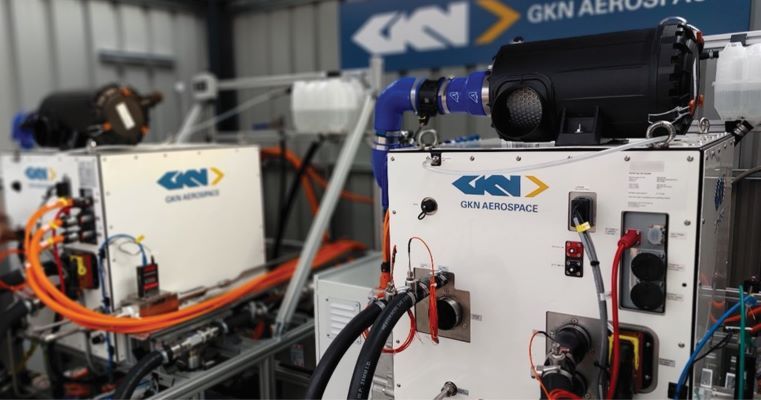
Hales believes the 50% fuel cell efficiency achievable today can be improved upon through advances in chemistry development and materials technology. Hyperconducting materials are being used in the DC power distribution system and the electrical machine’s stator. These behave similarly to superconductors but use metals such as high-purity aluminum, giving low resistivity at cryogenic temperatures without the abrupt failure risks of superconductors. “Hyperconductors are also an obtainable near-term technology and can be made reliably today in the form we require,” says Hales.
The reduced power losses in the distribution system mean more current can be transferred. Chunky copper cables can be replaced with smaller conductors and a lower voltage to reduce the weight by up to four times. The power distribution system can use a +/- 270V standard, already in use today on aircraft.
“Cryogenic cooling allows us to improve the efficiency of power distribution and propulsion. With hyperconducting materials, we see around a 10% improvement in electrical transfer efficiency, which directly translates into a smaller and lighter system for a given power,” says Hales.
“By cooling the electrical machine’s stator windings to cryogenic temperatures, we dramatically reduce AC and DC losses. This enhances efficiency and helps us keep the system compact.”
H2GEAR testing
Researchers on H2GEAR are integrating systems and have been testing fuel cells since the end of 2023. “A big milestone last year was the assembly of our demonstrator motor. It’s the first machine of its type that contains hyperconducting high-purity aluminum. That motor has been on test at the University of Manchester. We’re currently increasing its shaft power to verify its efficiency.”
GKN researchers have designed several concepts, including a notional study aircraft that will be used as a reference from which to study the powertrain in simulation.
“Our research indicates that hydrogen-electric propulsion offers a pathway to zero-emission aircraft. By leveraging cryogenic and hyperconducting technologies, we can improve range capability.
“With projected improvements in fuel cells and other components, we believe it’s feasible to scale up to single-aisle sized aircraft. That could make a meaningful impact on the aviation industry’s emissions footprint.”
Despite also being part of the H2GEAR program, GKN will not be using Intelligent Energy’s F300, because the fuel cell’s development roadmap targets aircraft of more than 100 seats, like Airbus’ plan.
“Fuel cell technology has only really been in development for aerospace for the last five years,” says Douglas-Smith. “There is uncertainty about its limits. It might be capped at 100 or 120-seat aircraft. Right now all we know for sure is it works for smaller aircraft and eVTOLs.”
Similarly to battery-electric aircraft, the path to market for hydrogen-electric will build up from smaller, general aviation aircraft to regional aircraft. and if the technology allows, perhaps on to larger airliners. Even then, the viability of hydrogen-electric depends on a massive cross-sector effort to establish sustainable ways of producing and distributing hydrogen fuel and swathes of new safety regulations. As Airbus has worked out, there is no shortcut to hydrogen aviation.