In recent years, nondestructive testing technology has grown more important in the aerospace sector. An increasing number of companies view it as a key element of testing in development, manufacturing, maintenance and inspection processes.
So, what are the different types of traditional and advanced methods and nondestructuve testing (NDT) processes? What are the key recent innovations and how might emerging technologies like AI, machine learning, or robotics influence the future of use of this technology?
Common Methods
The technologies and methods used for the NDT of aerospace parts are broad but can be grouped into several categories. These include: Penetrant Testing (PT), Ultrasonic Testing (UT), Radiography Testing (RT), Infrared Thermography (IRT), Visual Testing (VT), Eddy Current Testing (ET) – which uses an electromagnetically charged probe to induce eddy currents in the tested material to pick up surface and near-surface defects in conductive materials and Magnetic Particle Testing (MT).
As Guillaume Ithurralde, chief technical officer at Testia explains, the most commonly used NDT methods for the manufacture of metallic parts are PT, UT and RT – with ET and UT typically used for the maintenance of metallic parts, and UT and IRT for the manufacture and maintenance of composite parts.
“In Spain, the most common materials used in aerospace are composites, and therefore the most used NDT method is UT. Metallic materials are inspected mainly with Eddy Current and Penetrant Testing,” adds Pedro Serrano Cadahía, managing director at ENSIA (Testia Spain).
Elsewhere, Gary Reay, NDT engineer at Leonardo confirms that the company uses “all of the recognized common methods,” including ET, MT, PT, RT and UT. These are supplemented with other less common methods including Etch Inspection Testing (EIT) and Bond Testing (BT).
“Methods are chosen depending on the specific design requirement, material type, product topography, and production or repair setting,” says Reay.
Lifecycle variation
Meanwhile, Henning Juknat, global communications leader at Waygate Technologies, points to three main NDT technologies and methods: remote VT and inspection, UT, and industrial RT and computed tomography (CT). These inspection technologies are used to test initial materials, as well as finished aircraft components – and are also being used as part of in-field maintenance and repair processes.
“Which technology is used for inspection will vary within this lifecycle. Visual inspection, CT and UT all have certain strengths in inspecting specific materials and detecting different defects,” says Juknat.
“Next to the material, the shape of the part and its state and location of assembly may play a role. For example, industrial CT systems can be best used to inspect individual turbine blades, while the same blade as part of an engine on a wing might be better suited to remote visual inspection, borescope or ultrasonic inspection,” he adds.
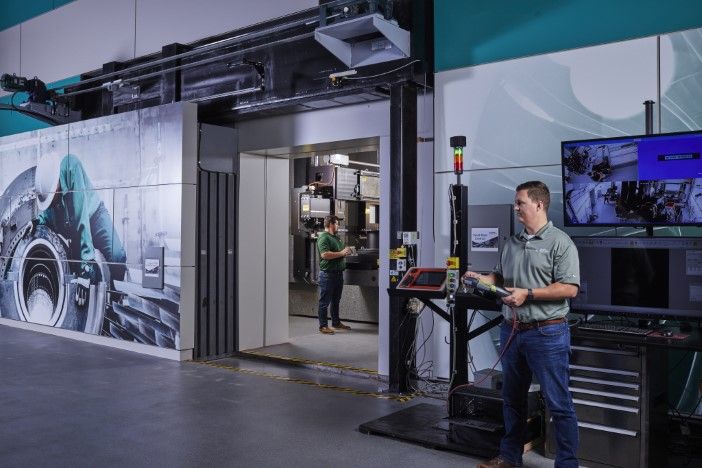
Recent innovations
Juknat notes it is difficult to point to any single development in NDT as the most important in recent years. However, he believes that “innovations that have provided better images for greater detection capabilities have had a big impact in recent years”. Digital and AI solutions like assisted defect recognition have “significantly sped up inspection and reporting processes while opening inspections up to personnel without expensive training and certifications”.
“The use of large-scale composite materials with complex internal structures, which can hide defects from traditional methods, have posed inspection challenges. Large and heavy samples, such as 3D-printed turbine components, require high penetration energy for thorough inspection, compounded by their complex geometries and internal structures,” Juknat says.
High-energy computed tomography (CT) systems – including those that use a linear accelerator to generate high-energy x-rays are becoming “essential” for inspecting such large and heavy samples with dense and thick components, which “could not be inspected with traditional methods”, says Juknat.
Phased Array Ultrasonic Testing (PAUT) also facilitates the inspection of large-scale composite materials with complex internal structures. An example of a PAUT system is Waygate’s own Krautkrämer RotoArray comPAct, which Juknat says provides “detailed internal images of components and allows inspectors to locate and characterize defects with precision.”
“We have also moved the PA technology directly into the probe so that inspectors can connect the probe directly to their tablet or phone to perform the inspection and send or file results much faster,” he adds.
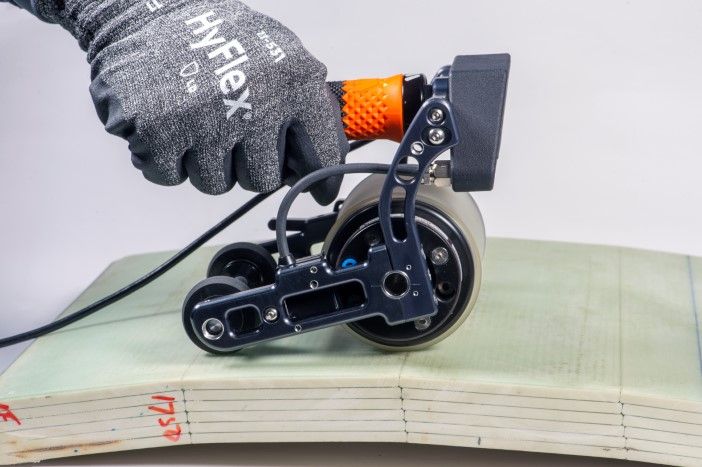
The aerospace sector is typically conservative when adopting NDT innovations, instead relying on well-proven technologies for inspection, but always aims to improve productivity and extend the lifetime of components.
“It takes time to trial, test and validate new technologies. Waygate Technologies has developed close relationships with end users to ensure a deep understanding of the challenges and opportunities and in turn the continued investment in the right areas,” Juknat says.
Digital Radiography
Reay believes that digital radiography has had the most significant impact on Leonardo among recent technological innovations. In particular, he notes that the introduction of computed radiography for the inspection of critical rotor components and assemblies “offered a big cost saving in terms of consumable materials, disposal of waste, and storage of images”.
“The process is no quicker, and process control is more intensive, but image evaluation is more detailed allowing for more accurate reporting,” he says.
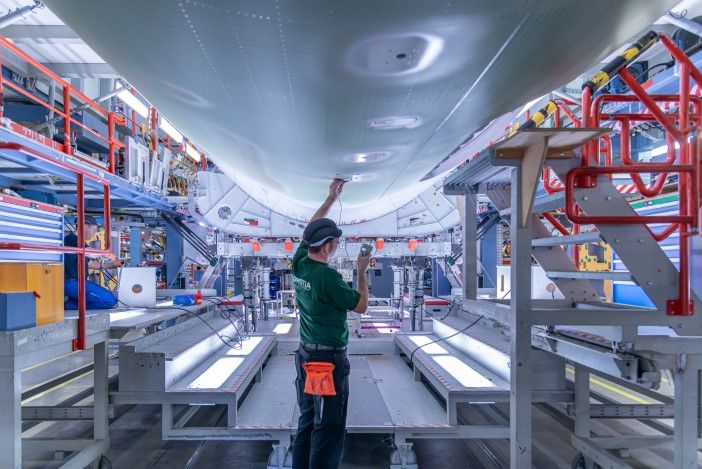
Although Leonardo has not yet found an opening for PAUT in its business to date – mainly because the company’s product designs “do not lend themselves to this technique so well” – Reay also observes that there have been “significant advances” in conventional UT test sets and systems that have made work more accurate. “The Sonatest Wave test set has enabled more reliable and repeatable inspections by the conventional UT Type II technique,” he says.
Meanwhile, Ithurralde highlights two main innovations at Testia – the digitalization of ET, RT, UT and VT systems, and the automation of data acquisition and post-processing systems, particularly following the adoption of NDTkit software. “PAUT increases data collection by a factor ranging between five and ten. It also brings traceability, which provides a good surface coverage. Digital x-ray is very interesting, especially for components requiring multiple shots. But both techniques require advanced operator skills,” he says.
“The most innovative software is the NDTKit, which allows most of the main companies and Tier Ones to use and share the same analysis software, at least for UT and RT – and for IRT and ET very soon. In the manual inspection field, it is also important to mention the robustness of some tooling like the UE1 that allows the inspector to have two NDT methods in one software package,” adds Cadahía.
Here, the UE1 – as well as the portable (Smart UE1) version and the technological brick (UE1 Box) version – refers to a multi-method inspection tool used by Testia that combines UT and ET capabilities in a single device.
“This makes them quite versatile for aircraft inspection purposes – all the other devices in the market are dedicated to just one method, either Ultrasound or Eddy Current,” says Cadahía.
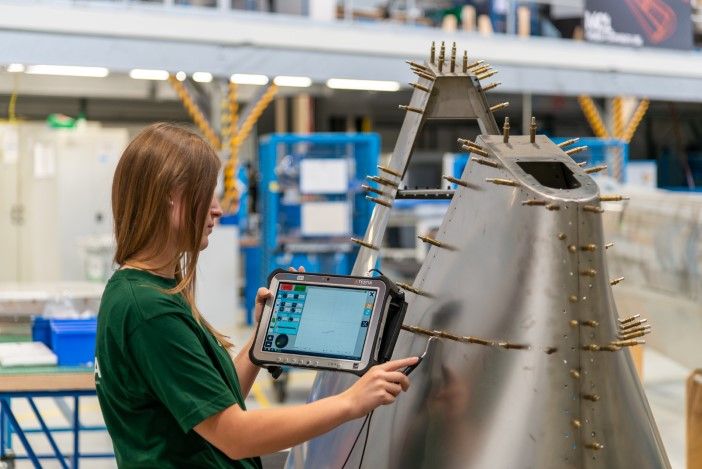
Safety and efficiency
The use of NDT in manufacturing, development, or maintenance exerts a significant impact on safety and efficiency.
Notable examples include the LineTool, LineMAP and LineSizing systems, first specified and prototyped by Airbus, then industrialized by Testia. Ithurralde says these tools enable users to tackle the lack of certified UT inspectors at airports. For example, if an A350, which features an airframe made of CFRP, needs to be inspected after an impact.
In terms of overall efficiency, Reay also points out that Leonardo’s recent procurement of a dual-robot, high-speed, 14-axis UT system will change the way NDT is viewed in the company by providing reduced inspection times and more accurate reporting. “It also ensures that the business is ready for parts in the future that come with increasing complexity, and cannot be inspected using conventional techniques,” he says.
According to Juknat, engine inspections are another key area in which the increasing demand for Maintenance, Repair, and Overhaul (MRO) services in the aerospace industry is pressuring operators to optimize processes without compromising safety.
A solution he points to that addresses this issue is the Everest Mentor Visual iQ+ (MViQ+) video borescope, a Waygate device that uses AI-enabled analytics to automatically count blades and recognize and categorize defects to improve data quality and streamline critical inspections.
“It is designed for immediate use without setup requirements and uses machine learning to automatically identify blades and other components within a gas turbine to relieve inspectors of simple tasks and give them time to consider important details,” says Juknat.
Key challenges
Whenever new products or materials are introduced, Reay notes that the main challenge always resides with the designers, who he says insist on being informed of every discontinuity present. He also confirms that composites represent a problem because they do not always conform to the normal rules of NDT.
“Complex structures of hybrid materials represent significant challenges, and our experience shows that many new equipment introductions – whilst encouraging – do not always provide any more capability than our existing equipment,” says Reay.
In addition, Reay observes that additive manufactured parts create additional challenges because of grain structure, surface finish, and topography. “There is still much work to do before this challenge is conquered,” he says.
“Regarding standards and regulations, our internal procedures ensure that international specifications and regulatory documents are embedded into our requirements. This is regularly tested through an extensive audit program,” he adds.
“The implication of non-compliance is additional work to correct the non-conformance, operator training, procedural amendment, or worst case scenario, suspension of the process.”
For Ithurralde, the main challenge currently facing the NDT sector is the scarcity of certified operators. Even so, he points out that compliance with aerospace standards is still ensured thanks to best-in-class training centers and a lot of monitoring conditions for the operators.
“The implication of non-compliance is structure failures, which can be dramatic,” he says.
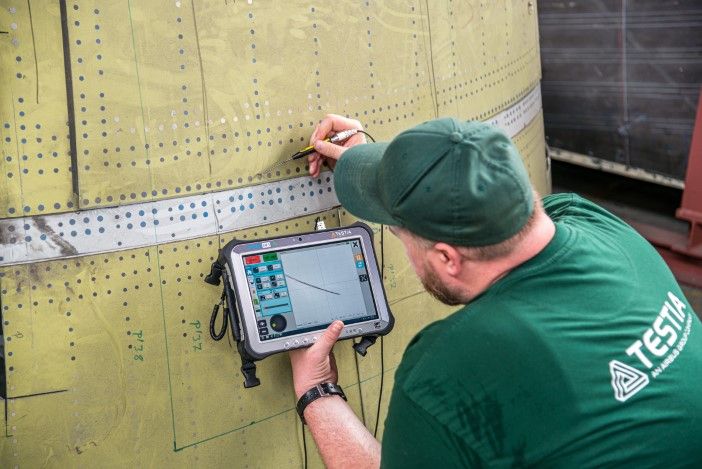
of aircraft skin (Image: Testia)
Common mistakes
Reay thinks the most frequent misconception relating to the use of NDT in aerospace is that it can reveal all the defects in a material. “Outside of the NDT world x-ray is often seen as the cure-all, but there needs to be greater understanding around the advantages and limitations of each method, and the benefits of using multiple methods to complement each other,” he says.
“Education is the key, and training for non-NDT engineers to provide some generic knowledge can be beneficial. The only other advice for young engineers particularly is to lean on the expertise of the experienced Level 3 personnel,” he adds.
Meanwhile, Ithurralde points to situations where engineers could potentially make an incorrect diagnosis despite doubts. In such situations, he urges them to share information with peers or ask for a second inspection.
“The most common mistakes are due to human factors. It is extremely important to stick to technical procedures and if that is not possible then stop, raise a hand, talk to your supervisor, and try to get a solution to the problem at hand,” adds Cadahía.
New possibilities
Looking ahead, Cadahía predicts that AI and machine learning will be a key technology for automatic inspections in the future, mainly to decrease the number of hours of analysis.
“This is something that could be done automatically as it is already being done in a lot of applications today. In addition, the use of sensors in the manufacturing of components will be key to reducing the number of indications,” he says.
Elsewhere, Ithurralde notes that robotics has already influenced NDT a great deal and that AI will do the same, as long as users build robust learning data sets hosted on the cloud and monitor the outputs properly.
“Future trends include more connectivity, more cybersecurity and more methods to qualify AI,” he adds.
Meanwhile, Reay predicts that the future holds promise for NDT – and that emerging technologies like AI and robotics are likely to play a much larger part in testing systems.
“Technology moves so quickly in all our lives, so I see a big role for AI in the evaluation of parts, providing less reliance on the human – the biggest source of mistakes in the industry,” he says.
“Robotics are already in use in many organizations, but this will only develop further as business demands greater efficiencies and cost reduction,” he adds.
Juknat agrees that, as we venture further into the future of aviation and space exploration, advanced inspection technologies will continue to be pivotal – particularly because new materials and propulsion technologies will call for continual adaptation in methods of inspection.
“The evolution of AI and machine learning is set to unlock new possibilities for enhancing efficiency and thoroughness in inspections. We can expect to see sophisticated technologies enable more insightful data from connected inspection equipment, assisted and automated workflows and integrated platforms and collaborations,” he says.
“Regardless of what the future holds, the field of aerospace inspection will remain critical in driving progress in the industry, ensuring safety, quality and productivity,” he adds.