By Frank Millard
3D printers and robots offer a way to remotely build structures such as space stations and satellites in orbit, but first they have to be tested on Earth.
In space manufacturing, where 3D printers and robots construct large structures and parts while in orbit, is being touted by a number of companies and experts as the way to work around expensive and technically challenging rocket launches.
Made In Space is one of the proponents of this new way to tackle and commercialize humanity’s final frontier. The company’s president and CEO, Andrew Rush, asserts that in-space manufacturing (iSM) is not a future aspiration, but a reality today. On board the International Space Station (ISS) astronauts are exploring manufacturing methods and testing hardware.
Rush says, “We pioneered manufacturing in space with NASA in 2014 with the Zero Gravity Printer. Since then we have developed and operated an additive manufacturing facility in space and made advances to robotically manufacture and assemble space optimized structures in space.”
Despite Rush’s claim, iSM can trace its beginnings back to 1973, when a feasibility study for in-space construction was conducted on the Skylab space station. Engineers have always been attracted to in-space manufacturing’s key benefit. “One of the advantages of in-space manufacturing and assembly is that it allows you to overcome the tyranny of the launch fairing. You can deploy structures to orbit that are larger than you can pack inside of a rocket and launch from Earth,” explains Rush.
Archinaut One
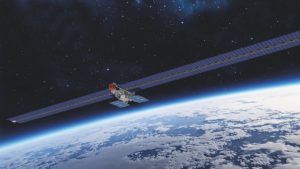
In July 2019, NASA awarded US$73.7 million to Made In Space to demonstrate the manufacture and assembly of spacecraft components in low-Earth orbit. Archinaut One is expected to launch on a Rocket Lab Electron rocket from New Zealand in 2022. The mission will focus on deploying a satellite power system to orbit. Other near-term applications for Archinaut might include antennas, space-based telescopes and large space-based reflectors. “We’re leaning on our existing experience with manufacturing in space and we’re really pushing the boundaries of what’s possible,” says Rush.
Archinaut One will use a robotic arm and their Extended Structure Additive Manufacturing Machine (ESAMM) to autonomously and precisely place components and 3D print two 10m beams, which will deploy two solar arrays while the beams are being manufactured.
“If successful, this has the ability to significantly increase the power capability of existing equivalently-sized spacecraft. Once the arrays are deployed, we are interested in the health of the beams and arrays over time, since there is a desire for long-term use of in-space manufactured structures,” says Charles Adams, senior subject matter expert systems engineering at NASA’s Technology Demonstration Missions program.
Large-scale structures
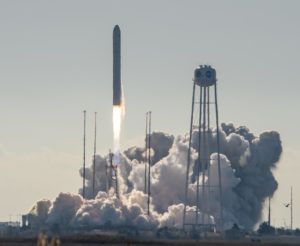
To experts such as Adams and his colleague at NASA, Lawrence Huebner, iSM has the potential to have a profound impact on space. It could enable the remote, in-space construction of communications antennae, large-scale space telescopes and other complex structures as well as be used to deploy large surface area power systems and reflectors for small satellites. As well as eliminating the volume limits imposed by rockets, it avoids the inherent risk of spacewalks by performing some tasks currently completed by astronauts.
The European Space Agency (ESA) also considers iSM a potential “strong enabler” for a wide range of space activities, such as long-term exploration missions, enhancement of telecommunication, Earth observation and navigation satellite capabilities.
In recent years, the ESA has made studies on the subject of in-situ manufacturing and construction using local resources, to support sustainable exploration.
Dr Advenit Makaya, advanced manufacturing engineer at the ESA says, “The ESA’s Clean Space initiative has recently launched studies in orbital Manufacturing Assembly and Recycling, looking at the system-level implications of such capability on the design of satellites.”
In November the ‘recycler’ was launched on board a Antares rocket heading for the International Space Station. The device, developed by Made In Space, turns plastic waste and 3D printed objects into feedstock that serves as the raw material for the company’s Additive Manufacturing Facility on the space station.
On and off-ground testing
Within the Archinaut program, its various systems have undergone extensive testing in a thermal vacuum chamber that simulates the harsh operational environment of space. Rush says, “We successfully demonstrated Archinaut’s additive manufacturing and robotically assembly capabilities within a thermal vacuum chamber in 2018. We have also validated the manufacturing technologies on the ISS.”
Made In Space’s ESAMM was tested in a vacuum chamber in the Engineering Evaluation Laboratory at NASA’s Ames Research Center in Moffett Field, California. Large beam segments were 3D printed and all the components subjected to pressures and temperatures equivalent to deep space. Additional tests will take place to ready Archinaut One for its flight demonstration. Testing in space is the next step to validate the technologies for future mission use.
Aerospace firm Tethers Unlimited uses float tables, platforms that float using air jets above flat granite tables, to test robotics and other elements in 2D simulated zero-g. The company’s engineers also use vacuum chambers to test the impacts of operation in vacuum. Dr Robert Hoyt, Tethers Unlimited’s co-founder says, “Prior to launch we run hardware through exhaustive environmental testing, which can include vibration, shock and thermal testing.
“These laboratory tests can evaluate the impacts of one or two elements of the space environment, but to test them all together we really need to fly experiments in space,” he explains.
Most aspects of system functionality can be tested individually on the ground except those dominated by gravity effects. The effects of gravity on manufacturing processes can be studied in microgravity testing, either on parabolic flight aircraft or suborbital rockets such as Blue Origin’s New Shepherd.
Zero to hero
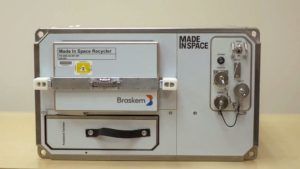
In Space)
There are several ways zero-gravity can affect manufacturing processes. “Where thermal behavior is important, the lack of convection in a microgravity environment can dramatically change the temperature at which components operate,” says Hoyt. “That is difficult to recreate on the ground but can be approximated with insulation or operation in vacuum.”
The forces on mechanical parts can also be much lower without gravity. Gravity offloading rigs that use suspension lines to support robotic arms or other mechanisms can be used to approximate that effect.
Micro-gravity has effects on motion dynamics and control. Professor Kazuya Yoshida from the Department of Aerospace Engineering at Tohoku University specializes in space robotics and the dynamics and controls of space systems. He explains. Testing on robots heading for zero gravity environments is usually done using air-floating testbeds, in a free-fall capsule dropped from a high altitude or in an aircraft during a parabolic flight.
There are also vacuum effects on heat transfer to consider. In the atmosphere, heat can be transferred by conduction, radiation and convection. “In the vacuum environment, convection is not available, so the thermal design of the systems becomes difficult. The vacuum also makes the lubrication of the joints and sliding elements difficult.”
Testing challenges
Hoyt believes that there is a lot of work to be done to ensure manufacturing technologies meet the requirements of long-duration manned missions. “For applications on the ISS and proposed Lunar Gateway, the iSM tools will need to meet very strict requirements for astronaut safety, fit within the power, mass, thermal, and volume constraints of the ISS Express Rack payload systems and achieve the verifiable precision and build quality needed for mission-critical parts,” he says.
For metallic parts, heat-treatment is often needed to achieve the desired material characteristics. However, ways of performing heat treatments in a microgravity environment in a manner that is safe for astronauts remains a large technology gap.
For manufacturing large structures for spacecraft systems, the development of robotic manufacturing and assembly systems and their autonomous control software – especially those that needed to diagnose and resolve anomalous behavior as they operate, pose a significant challenge.
“Previous and ongoing activities have highlighted the technology gaps, which include validation of the developed processes in the relevant environment,” says Makaya. “They are being identified to help define future activities on the topic.”