Lee Human from AeroTec details the firm’s recent flying engine testbed deal with Rolls-Royce and discusses its significance for the future of engine testing.
Starting up a company is something that many people do every day. But few company founders get to fulfil their vision for that company.
Just a week after announcing a major contract win with Rolls-Royce, Lee Human, AeroTEC’s founder and president, is an entrepreneur relishing the realization of his vision for the company. Founded 16 years ago to supply flight test services with just four employees, the Seattle, Washington-based firm has grown to have a 200-strong workforce of engineers and technicians. The company’s clients come from across the world to tap into its knowledge and capabilities within aerospace development and testing.
The multi-million Rolls-Royce deal will see AeroTEC convert a retired Qantas 747-400 into a flying testbed for the engine manufacturer. Rolls-Royce will use it to test the next generation of its more powerful, more efficient and more connected engines. Regardless of if AeroTEC wins the follow-on business to operate the aircraft, the deal is massive for the company and is enabling significant expansion at its Moses Lake headquarters.
Human describes the win as validating for the business: “We have built an organization with all of these capabilities, from initial preliminary engineering through to manufacturing, ground testing, taxi-testing, full-scale flight test to envelope expansion testing. This program is perfectly aligned with what we are as a company and we will be able to leverage all of our skills across it.
The Rolls-Royce job is the first time AeroTEC has been the prime contractor for a flying testbed program. The rival company that was in the running at the end of the tender is one of the biggest companies in the USA. “We are on the world-stage for this type of aircraft now,” says Human. “It opens the door to other projects in the large-scale flying testbed business.”
Only a few other companies in the world have the type of experience necessary to modify and operate large passenger aircraft in the way this contract requires. GE Aviation runs a testbed modified from a 747-400 in Victorville, California and Pratt and Whitney runs a modified 747-SP. “This job was out for tender and we won – technically and on cost,” Human says triumphantly.
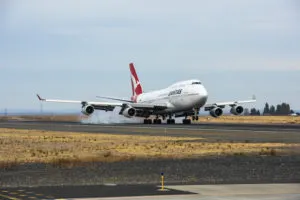
and control
De-Qantasizing
The 747, which has been purchased outright by Rolls-Royce, was delivered to AeroTEC’s flight test center in Moses Lake early in October. The first task in the two-year schedule of work is to “deQantasize” the aircraft – remove the livery and insignias of the previous owner. Engineers are also removing most of the interior of the aircraft.
Around 80% of the subsequent changes will be “under the skin” of the aircraft. Human says, “We will be installing extensive systems for fuel management, electrical power systems and load bank systems that can fully load the generators on the test engine.
“There will be hydraulic systems so we can fully test and fully load the hydraulics on the test engines and simulate various loads. There will be instrumentation and monitoring systems installed on the test engine capable of making thousands of measurements, as well as instrumentation and monitoring on the airframe.
“There will be racks and racks of engineering work stations in the main cabin.”
The airplane is going to be a “generic” test bed – it will use a single data acquisition system and different engines will be bolted on at two different points on the aircraft. On the side of the aircraft hard points are being installed so different stub wings, capable of carrying different business jet-size engines, can be fitted. Each stub wing will be made specifically for each engine – so the aircraft can test both fuselage-mount or wing-mount engines for example.
On the underside of one of the wings more hardpoints are being installed. The number two engine position is for testing larger commercial passenger aircraft engines, but engines can only be mounted onto the fuselage . “The testbed is designed to be reconfigurable,” says Human.
“The first application for the testbed has not been officially announced yet by Rolls-Royce, but the capability to be reconfigured will also make the testbed suitable for other programs, such as Trent series engines, in the future.
Time and money
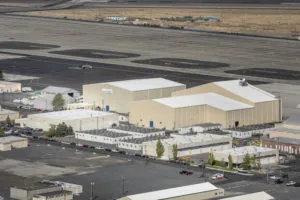
The 747’s modification work breaks down to annual sections. The engineering work to produce the drawings and get it through preliminary and critical design reviews is expected to take around a year. The actual modifications, bringing the systems online and ground and flight testing then happen the year after. Human is aware it is a tight schedule.
“Bolting a fifth engine onto an aircraft is not trivial,” he says. “When you look at the support systems like the fuel and electrical systems, it’s very complicated to do it safely. We have to worry about rotor burst, modern engine control systems that are not native to the 747.
“There are a lot of new things that have to be integrated. This is not a small airplane and it’s going to be very challenging.”
A further challenge is the data acquisition system, which has to be future-proofed to be as advanced as the engines it is testing. Human says, “These modern Rolls-Royce engines are extremely data intensive – they are called the intelligent engine – with terabytes of data coming off them. The engines being tested will be very advanced.
“The testbed will be the most advanced airborne data collection and analysis system ever-produced.”
To meet the demanding schedule and technical challenges, the company is expanding at Moses Lake Flight Test Center, where it has already invested around US$20 million. The Rolls-Royce deal is enabling further expansion at the site. “We have already started building an additional wide-body 70,000ft² hangar, big enough to house a 777X-10 with the wing tips down. The hangar will be occupied by September 2020,” says Human.
Other business
Human is speaking to me about the Rolls-Royce deal on the company’s busy stand at the National Business Aviation Associations annual exhibition. The company’s presence here is evidence of the broad mix of business the company engages in. Most of the work is on Part 25 aircraft, larger business jets. “A lot the business jet OEMs are customers, as are the Tier Ones, companies like Rolls-Royce,” says Human. “There is a lot of innovation at the business jet sector level, more so than at the commercial level.”
AeroTEC’s clients initially approach the company with a product concept, which can be at different levels of maturity. “The first task is to assess if the product is certifiable. We take it through verification and validation. We define all the regulatory, customer, manufacturing or marketing requirements it needs – from the aircraft level down to the component level. We then work out what evidence is needed to meet those requirements,” says Human.
A component could for example need a DO160 quality test or bench test in the laboratory. An example job at the system level might mean developing a test rig. At the aircraft level it could mean flight testing. As well as test results, evidence could be in the form of CFD (Computational Fluid Dynamics) or FEA (Finite Element Analysis) simulation or wind tunnel work.
From this information AeroTEC produces an actionable roadmap to certification for the product. “That’s where the first surprises may emerge,” says Human. “It allows us to recognize what won’t be certifiable because it doesn’t meet this or that requirement. We then make recommendations, such as a redesign.”
A client will then take those recommendations and act on them or partner with AeroTEC to make the adaptations to the component or aircraft. “The shop in Moses Lake says if you need it tomorrow, we’ll build it tonight. It might just be a new wire harness or routing for a hydraulic tube, whatever is needed to keep the test vehicles flying.”
It’s also common for AeroTEC and its clients to hot desk and work side-by-side. For example, at its peak there were more than 100 Mitsubishi employees in its Seattle offices. The MRJ, renamed the SpaceJet, is now in the final stretch of testing for certification. The company is working in a similarly close way with Israeli company Eviation to help it develop and test an all-electric aircraft. Human says a big benefit from partnering so close with clients is the knowledge-sharing amongst the company’s and its client’s engineers that it facilitates.
“Every OEM has a different style and approach. We get to see the strengths and weaknesses of each and see best practice. We can then help our customers with our best practices,” he says.
Electrification
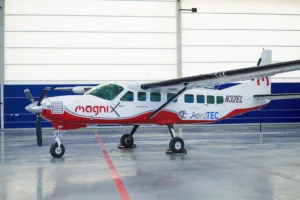
As well as Eviation, AeroTEC is working with separately with electric propulsion system developer Magnix to develop a demonstrator and certification platform for its technology on a Cessna Caravan.
The first prototype of Eviation’s clean sheet all-electric aircraft, which is called Alice, is going through ground testing and will be ready for taxi testing soon. The second prototype aircraft is arriving in Moses Lake during October, will be built there and has its maiden flight planned to place in 2020.
A major theme of the NBAA show was the growing trend of urban air mobility. Hundreds of companies, including the major OEMs, are now developing electric Vertical Take Off and Landing (eVTOL) aircraft. eVTOLs are being designed to hop across or between cities and many believe by the middle of the next decade could represent an entirely new section of aviation activity.
Human believes the work being done on electric and hybrid aircraft, like the Eviation and Magnix projects, has to take place before eVTOLs can become a reality. “Developing and validating the power systems and flight control systems is a pre-requisite for the eVTOL,” says Human. “People underestimate the challenge of the auxiliary systems to the battery, the power systems, the controller, the cooling systems.
He adds that other prerequisites are increases in the energy density of batteries, which he believes will happen in the next five years. Engineers also need to develop the integration between flight control and electric propulsion systems. “The Eviation aircraft will achieve this integration between thrusters and flight control. The eVTOL needs this link to exist. Before it can come into say, Honeywell flight control or BAE flight control systems, there is this first step that has to be taken with the control systems.”
AeroTEC began to work towards becoming a leader in the area of electrification of aircraft around three years ago, says Human. The work with Eviation and Magnix is the result of investment in the infrastructure and engineering skills to support these types of aircraft as a result. But while speaking at the company’s stand at the NBAA show the stand has become noticeably busier. Human is also keen to acknowledge that the company appreciates and understands its core customers: “We are here to partner with OEMs and Tier ones to get their products to certification. New aircraft development programs tend to get all the attention and resources. It’s the modification and the customer service teams that want upgrades that can struggle. We can partner with them to get that stuff done.”