by Ian Goold
In early January, Brussels Airways Airbus A330-303 OO-SFM (manufacturer’s serial number 030) landed at Bob Sikes Airport in Crestview, Florida, for dismantling. To casual observers the arrival of the longest-serving active A330 might have suggested the hangar doors were about to close on the very successful European design after delivery of more than 1,400 machines.
But MSN 030’s retirement does not signal even the beginning of the A330’s end – the marque is alive and well. Indeed, A330-800 F-WTTO (MSN 1888), the latest development of the twin-aisle twinjet, is currently undergoing trials at Airbus’s Flight Test and Integration Centre at Toulouse-Blagnac airport in southwest France.
Establishing the performance envelope
The Airbus A330 family’s latest two members, the A330-800 and the A330-900, have been re-engined under the A330neo (new engine option) moniker. The former has a range of 8,150 nautical miles (15,090km) with a capacity of up to 257 passengers, while the latter can cover 7,200 nautical miles (13,330km) and has a capacity of up to 287 passengers.
Both aircraft use Rolls-Royce’s Trent 7000 engine, which has been developed exclusively for the new aircraft. The Trent 7000 has a 112in (2.8m) diameter fan This doubles the bypass ratio from five to 10.
With the A330-900 having received European Aviation Safety Agency (EASA) type certification on September 26, 2018 and the first customer deliveries of the aircraft underway, the focus of testing engineers has been transferred to the other variant, the -800.
By mid-February 2019, the -800 variant had logged 70.5 flight-hours – equivalent to around 20% of its predicted test requirements – during 22 flights since its first on November 6, 2018. Airbus hopes to receive formal European airworthiness approval before October 2019, ahead of first delivery and entry into service next year.
After a pause following the initial flights, testing has “resumed apace”, according to Airbus. Early test flights enabled the manufacturer to establish the A330-800’s full performance envelope, with high-speed flight “in normal law and direct law, including low speed, and high-speed maximum operating limit Mach number (MMO) and velocity (VMO) and maximum allowable speed (Vmax) and Mach number (Mmax)”.
MSN 1888 is the fourth A330neo and the first -800 to be dedicated to certification. Previously, three larger A330-900s (MSNs 1795, 1813 and 1819) had flown, including the first production aircraft on which Airbus conducted passenger-cabin function and reliability, route-proving trials.
While not all-new designs, the A330-800 and -900 models feature novel sharklet wingtips and are powered by new 68,000-72,000 lb-thrust Rolls-Royce Trent 7000 engines. Airbus cites 99% commonality between the two variants.
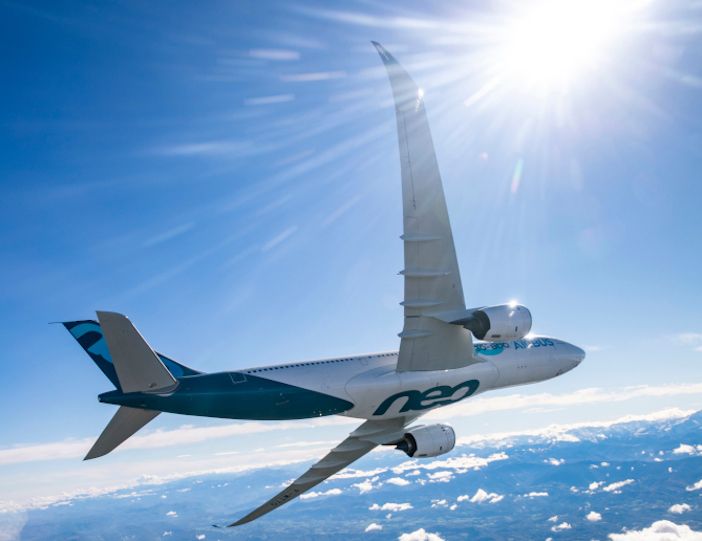
The -800 and -900 are based on the earlier A330-200 and -300. However, the -800 variant is 5m (16ft) shorter than the -900, and hence a taller tailfin is required to provide longitudinal stability compensation. “The shorter fuselage means that the engines are closer to both the front and the back of the aircraft,” points out Jean-Philippe Cottet, the Airbus head of development flight test.
He says that from the front this makes a difference on the air-pressure monitoring anemometry equipment. And from the back it will have an effect on the aircraft’s behavior. Airbus will also have to check the difference in the structural response of the shorter aircraft during flutter testing.
Airbus has optimized the A330neo wing to deliver 4% lower fuel burn compared to the current A330, according to head of A330 marketing Crawford Hamilton. The increased performance is attributed to a 4m (13ft) wingspan increase to 64m (210ft), along with a consequent increase in aspect ratio.
“Span-wise lift distribution is closer to the aerodynamically optimum elliptical distribution – a combination that delivers a more efficient wing,” says Hamilton. “It also has a three-dimensionally optimized twist.”
The A330neo wing introduces reshaped slats on the wing inboard leading edge and modified trailing-edge flap-track fairings. Airbus has fitted a new upper-belly fairing made of composites.
The company claims to have achieved lower operating cost for the A330neo by leveraging the A350’s new-generation technology and the current A330’s exceptional 99.5% dispatch reliability. As well as longer wings and new engines, pylons and nacelles, the A330neo offers new cockpit systems and cabin interiors, providing an extra 10 seats.
Time in the sky
For MSN 1888’s initial four-hour flight on November 6, take-off and landing were performed with the A330-800’s digital flight controls in direct law. During the flight, which went up to 30,000ft, aircraft general handling was explored in all three axes, with other tests covering cabin pressurization.
The opening test sequence of between five and 10 validation flights led what Airbus terms the initial flight test development phase. This was aimed at exploring the flight envelope, including performance flights that involved stalls and flutter tests.
Flight testing of the A330-800 in December 2018 and January 2019 included aerodynamic identification for development simulator modeling, additional flutter tests, and unspecified uncategorized effects – the latter including Mach, landing gear and center of gravity effects.
At the beginning of February, Airbus was preparing for the next phase of the campaign for characterization tests, including lateral and longitudinal identification; handling qualities testing for flight-control laws tuning; and more detailed handling quality checks. Certification tests, including autopilot trials, crosswind and minimum-speed checks, and systems tests are still to be conducted.
In addition to the high-speed flights to confirm MMO, VMO, Vmax and Mmax values, and the low-speed regime, initial test operations covered first-flight flutter, aerodynamic modeling identification flights, and airspeed calibration flights.
The passenger cabin of MSN 1888 has been fitted with instrumentation and a single station for the two flight test engineers. Cottet says, “Testing of the prototype is mainly dedicated to flight physics, handling qualities and performance.”
A 9 metric ton weight increase to provide a 251 metric ton maximum take-off weight for both A330neo variants – announced in 2017 and available from mid-2020 – is to be obtained through a stronger (but not heavier) structure, supported by an upgraded, more robust landing gear, according to A330neo chief engineer Francois Kubica.
The manufacturer is also planning to enhance the A330neo’s structure through local minor reinforcements to the wing and fuselage, but without increasing aircraft empty weight. “All weight from reinforcements will be fully compensated for by weight savings made elsewhere in the aircraft,” says Kubica.
Local reinforcement is required for both main and nose undercarriage units and is complemented by new brakes and tires on the adapted wheels. Improved corrosion- and fatigue-resistance have been planned
for the heavier aircraft.
A330-800 follows -900
As A330-800 flight testing began, airframe and engine manufacturers were completing formal airworthiness approval of the A330-900 and both variants’ new Trent 7000 high-bypass turbofan engines. The A330-900 accumulated 1,500 flight test hours during 450 flight tests in just 53 weeks with the three A330-900 test aircraft. This work validated the re-engined A330neo family’s common cabin, flight and ground operations, powerplants and systems.
At the end of January 2019 Airbus also received its extended-range, twin-engine operational performance standards (ETOPS) clearance for the A330-900, which is awarded in two stages.
The initial EASA approval – for flight up to a maximum diversion time of 180 minutes from a suitable landing ground at single-engine cruise speed – was released in mid-November, subject to a restriction. Approval was restricted to engines incorporating work outlined in specific service bulletins. Unrestricted approval, which permitted a 330-minute diversion, followed six weeks later.
Airbus delivered its first A330-900 to TAP Portugal in late November 2018. The European carrier received two more in January and expects to receive 17 more before next year. During 2019 Airbus expects to increase A330neo manufacture. Meanwhile, Rolls-Royce has been accelerating Trent 7000 production.
The next three aircraft to be produced are earmarked for Icelandic low-cost, long-haul operator Wow Air, São Paulo-based Azul Linhas Aéreas Brasileirasa, and Air Mauritius.
For their inaugural A330-900s, each of these operators has adopted the Airspace-by-Airbus furnishings that the airframe manufacturer says provides “more personal space, larger overhead storage bins, advanced lighting, and the latest generation of in-flight entertainment and connectivity”.
According to Airbus, the first examples of cabin layouts for the four customers have successfully undergone final cabin inspections, meaning that the customers are happy with the standard of passenger accommodation.
And as for how the A330neos fly, Airbus no doubt hopes each customer will echo the words of experimental test pilot Malcolm Ridley on landing the A330-800 after its first flight: “It flies just like an A330, only better.”