Ariane 6’s core stage is powered by the Vulcain 2.1 engine, its upper stage is powered by the reignitable Vinci engine. Strapped on to the core stage will be two or four P120C solid-fuel boosters, a technology shared with Vega-C, to provide thrust at liftoff.
Latest developments
In the last six months, Ariane 6 has moved to the final stage of development, where tests qualify the designs that will guide production.
At DLR-Institute of Space Propulsion in Lampoldshausen, Germany, hot-firing tests of the Vulcain 2.1 engine are close to completion. Vinci engine hot firing tests have finished successfully. A team of experts there is now examining the results of these tests and once these reviews are successful, these two engines will be qualified for flight.
A new test facility, the P5.2, at Lampoldshausen was inaugurated in February and will host the testing of the complete Ariane 6 upper stage. This upper stage will be delivered from the ArianeGroup in Bremen, Germany which is currently focusing on engine integration, final operations and testing. MT Aerospace, also in Bremen, are supplying the fuel tanks.
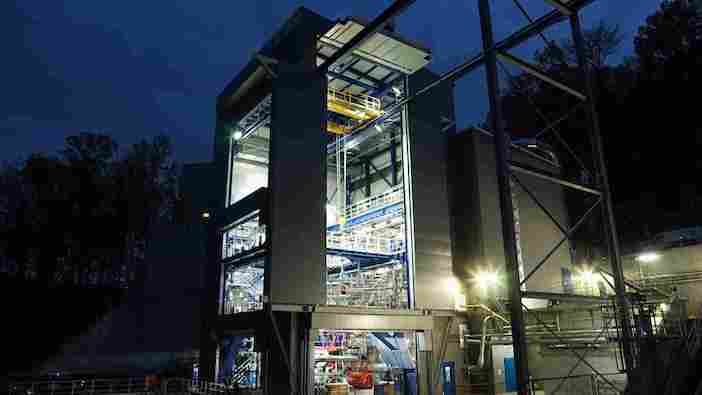
An ArianeGroup facility in Les Mureaux, France, hosts the largest friction stir welding machines in Europe for producing the Ariane 6 cryogenic tanks used in Ariane 6’s core stage. The aft bay, which secures the Vulcain 2.1 engine to the core stage is in production and being integrated at the same location.
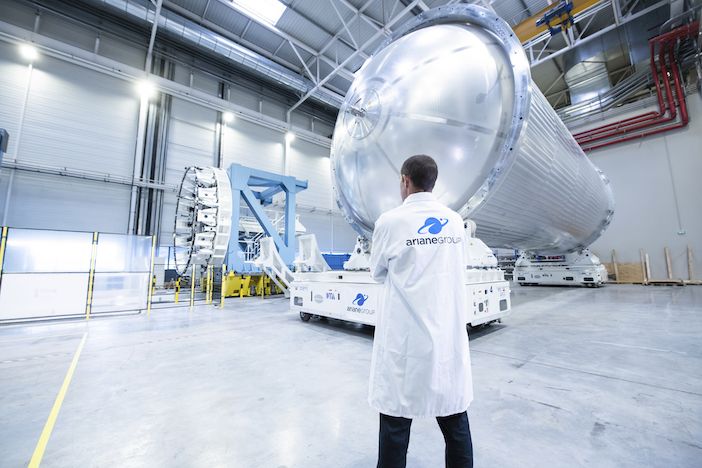
The first qualification model of the P120C strap-on booster configured for Vega-C was static fired in January on the test bench at Europe’s Spaceport.
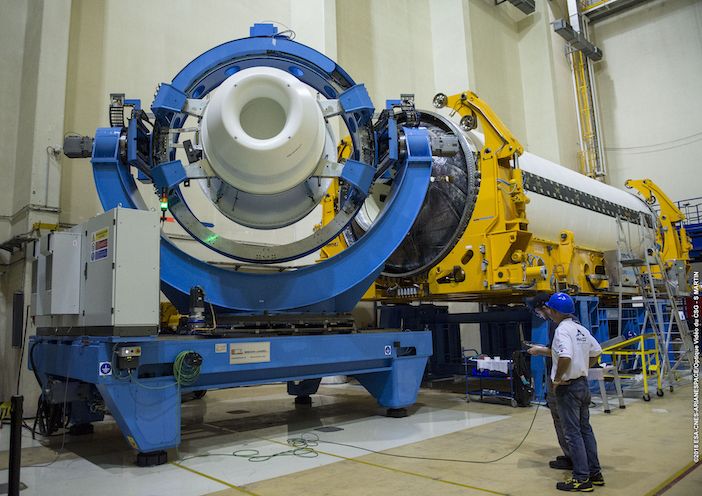
The second qualification model, configured for Ariane 6, will be tested at the beginning of next year. The 11.5 m long and 3.4 m diameter insulated P120C motor case is made of carbon composite built in one piece by Avio in Colleferro, Italy.
Meanwhile at ArianeGroup in Issac and Le-Haillan, France, fully robotic production lines have the capability of increasing production by 30% to assemble the rear skirts and build nozzles for the P120C strap-on solid rocket motors. MT Aerospace in Augsburg, Germany, are supplying the rear skirts.
RUAG Space in Switzerland has also recently produced the first large half-shell of the fairing for Ariane 6. Built in one piece using carbon fibre, it was cured in an industrial oven instead of an autoclave.
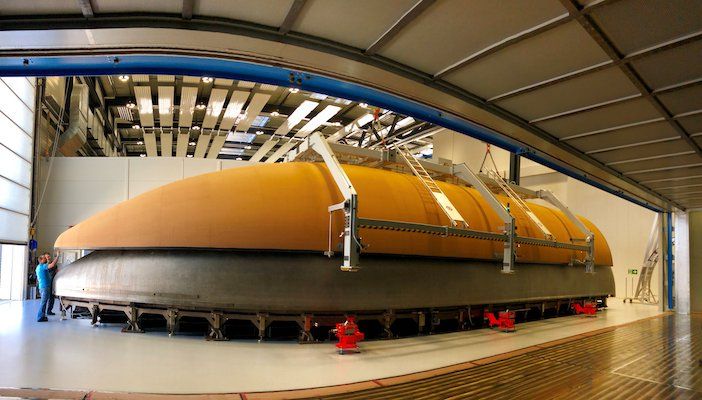
Preparing for flight
Early next year, the P120C solid rocket motor configured for Ariane 6 will be test fired in Kourou, French Guiana, to qualify it for flight. Ariane 6’s upper stage will be test fired at the DLR-Institute of Space Propulsion in Lampoldshausen, Germany. A test model Ariane 6 will also start combined tests in Kourou, including a static fire of the core stage engine, the Vulcain 2.1.
Ariane 6 launch base nears completion
The Ariane 6 launch base at Europe’s Spaceport is also enarly complete. The main structures include the Launch Vehicle Assembly Building, the mobile gantry, and the launch pad.
The launch vehicle assembly building used for horizontal integration and preparation of Ariane 6 stages before rollout to the launch pad, is complete and tools are now being installed.
The 90m tall metal frame of the mobile gantry is fully constructed and in February cladding started. The mobile gantry houses Ariane 6 until it is retracted before launch. The first rolling test of this 8200-tonne structure will be performed this summer.
The launch pad flame deflectors were installed at the end of April. They will funnel the fiery plumes of Ariane 6 at liftoff into the exhaust tunnels buried deep under the launch table. The nearby water tower has also been installed.
The first four levels of the mast have been mounted and welded and in February the integration started of the fluidic lines that will interface with the launch vehicle.
The LH2 and the LOX plants that produce and store the liquid hydrogen and liquid oxygen needed to fuel the launcher’s engines are complete.
This article was originally published on the European Space Agency website here.