Words by Jonathan Dyble
Alternative fuel in aviation is beginning to gather momentum. In November 2021, engineers at Rolls Royce broke the electric speed record with Spirit of Innovation. The modified sports kit plane, equipped with the latest in battery technology and an all-electric powertrain, reached a speed of 555.9km/h (345.4mph).
It’s now well over a year since this feat was achieved, and the technologies for electric and hybrid aircraft continue to mature. For example, NASA’s experimental X-57 all-electric aircraft, which uses lithium batteries to run electric motors for 14 propellers and is focused on examining the effects of distributed electric propulsion is expected to fly soon.
Despite the issues around electrification, industry insiders believe that electric airplanes are suitable for commercial short-haul flights in the medium term.
However, there are still many challenges that airframers developing electric propulsion systems, both hybrid and electric continue to face. From deciding what battery cells to use, to configuring cells, optimizing size, weight and power, and assessing exactly how the batteries perform in real-world use cases, engineers still have many new technologies and approaches to explore as they develop their test strategies and final products.
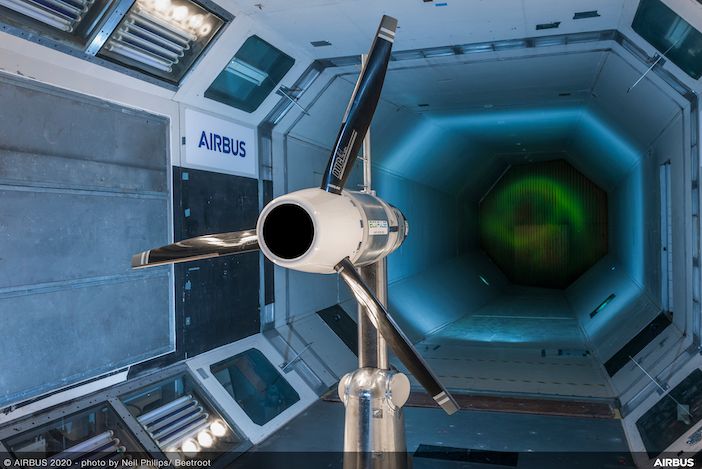
From EV to aviation
Fortunately, the electric vehicle (EV) sector is paving the way for faster progress. Lithium-ion battery technologies, primarily for EVs, have evolved dramatically over the last 15 years. The US Department of Energy (DOE) estimates that the price of lithium-ion batteries for EVs was around 89% lower in 2022 than in 2008. Bloomberg predicts that lithium-ion battery costs will fall below US$100/kWh this year and US$61/kWh by 2030, by which time they will reach price parity with conventional fuel models if they haven’t already.
However, it is difficult to transfer this progress from the automotive into the aerospace sector. It’s not simply a case of scaling up those batteries approved for the automotive sector for use in aircraft.
“The technology underpinning batteries at cell level is fundamentally the same for aerospace and automotive. But in the first incarnation of aerospace electrification the different applications drive significant changes in all elements of the design, development, manufacturing and certification processes,” explains Martin Dowson, chief engineer and head of battery systems engineering and research at WMG in the UK.
WMG is an academic department at the University of Warwick that has been testing EV battery packs for car companies since their introduction and is now increasingly serving the aerospace sector. Dowson is well versed with the technical and regulatory challenges surrounding battery use in aircraft.
“Aerospace players need to actually prove batteries are safe, whereas automotive players are
more focused on passing discrete safety tests,” he says.
“Cars just have one battery pack per vehicle, while planes require an energy storage system comprised of multiple packs, configured in a manner that is robust to the failure of individual elements. Further, at both a system and pack level, key features from an automotive pack will become safety critical in an aerospace application.”
Here, Dowson points to the importance of SOX (State Of X) a model-based estimation of different battery states such as state of charge (SOC), state of energy (SOE), state of power (SOP), and state of health (SOH). SOX provides insights into the health and performance of cells in modern battery management systems.
“In automotive, SOX has a failure mode,” Dowson says. “This can lead to customer dissatisfaction, where vehicle performance can dip a little at low states of charge, for example.
“But in an aerospace application, this data becomes critical for the capability for an aircraft to land safely or perform any abort landing scenarios – energy and power hungry operations. In automotive applications, drivers can slow down and limp home. Aircraft aren’t afforded this luxury.”
Higher standards
The higher risk scenario of flight means that alternative battery technologies and techniques are required by the aerospace sector. Testing standards are significantly higher where failures and errors have a higher probability of causing catastrophic incidents.
“Battery tests will typically determine the suitability of the battery for its intended application, a process known as qualification testing,” says Michael Galea, professor of electrical machines and drives for the department of industrial electrical power conversion at the University of Malta.
“During qualification testing battery capacity, internal resistance and the amount of self-discharge which are all indicators of the battery state of health, need to be ascertained, with tests including cycle testing and measurement of battery parameters, such as heat generated during use.”
Without a universal best battery technology for electric aircraft, and because different use cases require different solutions, much of the challenge for engineers lies in assessing the suitability of batteries for their aerospace applications.
Key decisions must be made on the most suitable type of battery cells for their aircraft, how they are configured, integrated and how their size, weight and power are optimized while prioritising safety.
Galea says, “An engineer needs to consider performance in terms of power density and energy density and safety in terms of adequacy, reliability, monitoring of state of charge and state of health, with associated backup plans in case of degradation.
“With that said, safety and performance are two design objectives that quite often contradict each other in aerospace. While a battery’s rating in kWh/kg is attractive to the industry, increased kWh/kg can mean a heightened risk of thermal issues and a loss of power supply to drive the aircraft systems.”
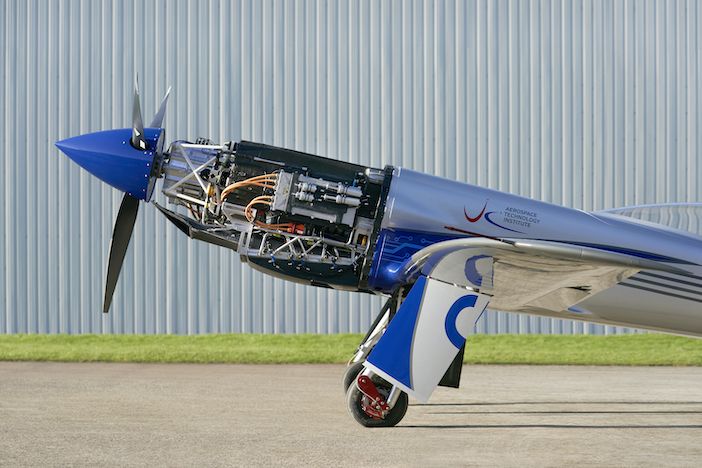
Balancing act
Pipistrel, maker of the Velis Electro, the world’s first and only type-certified electric aircraft, has worked hard to find that balance performance and safety. The company was acquired by US aviation giant Textron in 2022.
“We began the journey of Lithium battery development from commercial off the shelf cells more than 15 years ago,” says Tine Tomažič, group chief technology officer and director of R&D at Pipistrel Vertical Solutions.
“Pipistrel has developed processes to identify suitable battery cell candidates. These tests include performance screening during different environmental conditions and battery aging with different charge/discharge profiles. We also test for robustness in hot and cold environments and soaks, test venting characteristics, and do calorimetric discharge evaluations.”
Galea believes that the best way to successfully test each of these characteristics as well as others is to build accurate models of the battery cells themselves, packaged as battery packs and integrate those models into the aircraft or the aircraft sub-system models.
“Electro-chemical models that are validated experimentally are the most accurate and can be used for design and for lifetime analysis,” Galea says. “As early as possible, a shortlist of candidate cells should be tested against the mission profiles to understand the performance and degradation before going too far down the sourcing and pack design process.
“To fully characterize a cell is a three-to-six-month process. This is because a cell’s behaviour is sensitive to state of charge, temperature, power output and aging.”
Bridging the power gap
Pre-application testing is only one part of the puzzle. Analysis is as important as implementation to assess if a battery has been successfully deployed because it enables the identification of improvement opportunities or applications where alternatives may be required in future projects.
For this reason, it is critical that engineers work to assess how batteries perform in real-world use cases alongside initial testing efforts. Activities are expected to ramp up in this area during the coming years as electrified aircraft move closer to market.
Again, engineers at Pipistrel are working hard on this front and have identified several key focus areas where improvements to its existing models are possible.
“We’re working in several different trajectories when it comes to battery development at the moment,” Tomažič explains. “This includes several research programs around battery chemistry, structural integration optimization, thermodynamic optimizations such as liquid and hybrid cooling, on demand maintenance with increased battery life periods, and lifecycle sustainability considerations with solutions for battery second life.”
Progress across these fronts is positive. But the aerospace industry must map out its own transitional journey towards net zero applications. Furthermore, engineers must explore exactly which technologies work most effectively for aircraft given the nuanced requirements of the sector.
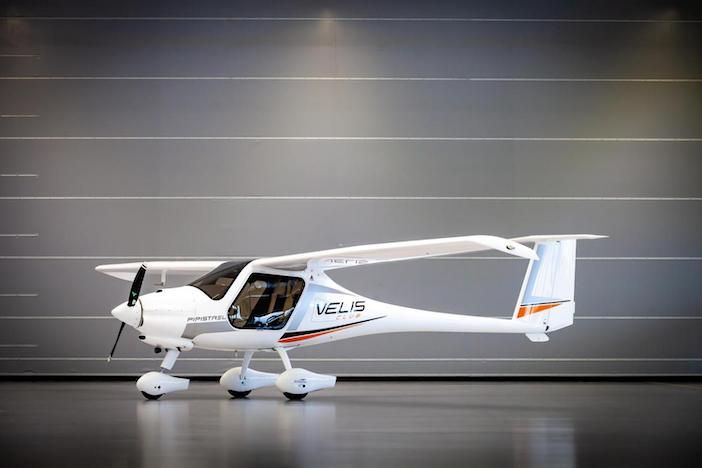
For Galea, this will require outside creative thinking and the use of novel, innovative development techniques and technologies such as digital twins, highly accurate models and hardware in the loop systems.
“In the future, testing of batteries should only be used for experimentally validating certain aspects of new products, and to prove correct data being inputted to the systems mentioned above,” he states, outlining his vision.
“The requirements of electric aircraft need an order of magnitude improvement in terms of energy density capability, and in terms of reliability for certification.
“This can only be achieved by changing design processes today, from the traditional design, build and destruction-test of samples, to processes where all design objectives are included from the start of the development process.”
Without question, a combination of methods will be required, and there is still a long way to go to bridge the current power gap in aircraft. Galea points to hybrid applications as the most realistic solutions for commercial use in the near future.
“The highest electrical energy demanding aircraft in use today demands a total electric power generation capability of 1MW on board. However, it is estimated that for commercial aircraft such as an A320, B737, the propulsion power required for a fully electric version would be something in the region of 40MW,” says Galea.
“From a battery perspective and an electrical components perspective, the way forward is probably not going to be fully electric vehicles, except for the cases of light aircraft and up to 50-100-passenger models.
The probable solutions are going to be hybrid or turbo-electric type aircraft.”
Galea estimates that the industry needs battery cells capable of at least 400Wh/kg – something we can only truly expect to see in around five years’ time – to achieve these platforms. In this sense, the industry remains in very much a state of watch this space when it comes to batteries.