On 19th February 2018, a CRJ900 jet experienced difficulties during take-off at Kigali International airport in Rwanda. The crew suspected that an object had entered one of the jet’s engines, causing potentially serious damage, so the aircraft was grounded and an urgent call was made to Skywards, requesting internal inspection of the affected engine.
Skywards Aviation is EASA Part 145 approved for borescope inspections according to the Aircraft Maintenance Manual and the requirements of specific Service Bulletins and Airworthiness Directives. The company’s capabilities cover over 40 different types of engine and auxiliary power units.
“In these circumstances, it is important for inspection work to be undertaken as quickly as possible,” says managing director of Skywards Rob Ward. “We knew that this engine would require a borescope with a 4mm diameter, which we don’t have in-house, so we rang Ashtead at 8am and by 10am they had rung back to confirm that an instrument would be ready for collection.
“We hire inspection equipment from Ashtead Technology because it provides us with access to the latest technologies. As a result, we are able to employ the best instrument for every job, without having to pass on the costs of purchase and ongoing maintenance to our customers.”
Following a call to Ashtead Technology, Ward was able to collect the IPLEX NX borescope on his way to the airport before travelling to Rwanda, and the engine inspection was undertaken the following day.
Damage discovery
The CRJ900 jet is powered by two turbofan engines mounted on the sides of the rear section of the fuselage. The inspection took around 6 hours. Ward says, “It was clear that the engine had suffered catastrophic damage. Using the stereo measurement capability of the IPLEX NX, it was possible to measure the flaws and compare them with the limits specified in the maintenance manual.
“Damage was found in the blades of the high pressure compressor. There was no evidence of a bird strike, so the damage may have been caused by a small item of debris on the runway. Occasionally, borescope inspections find damage such as an imprint for which the damage can be identified; from a nut or a bolt for example, but in this instance the damage appeared to have been caused by a stone, or a similar object.”
Ashtead Technology’s Rebecca Stanley says, “The IPLEX NX is ideal for this type of work; it combines a high-pixel digital image sensor, an ultra-bright laser diode light system and a unique ‘image-noise reducing’ PulsarPic processor to automatically adjust light output, to deliver the clearest images possible in changeable inspection conditions. As a result, users are able to study the subtlest defects in the darkest or most reflective places and over wide areas; producing clear, bright images.”
With wide-field stereo measurement capability the IPLEX NX measures a range of defect characteristics including distance, point-to-line, depth and area/Lines. The instrument’s multi spot-ranging function enables real-time measurement of the distance from the scope tip to multiple points on the inspection surface. This provides surface shape information with no pause or break in the inspection.
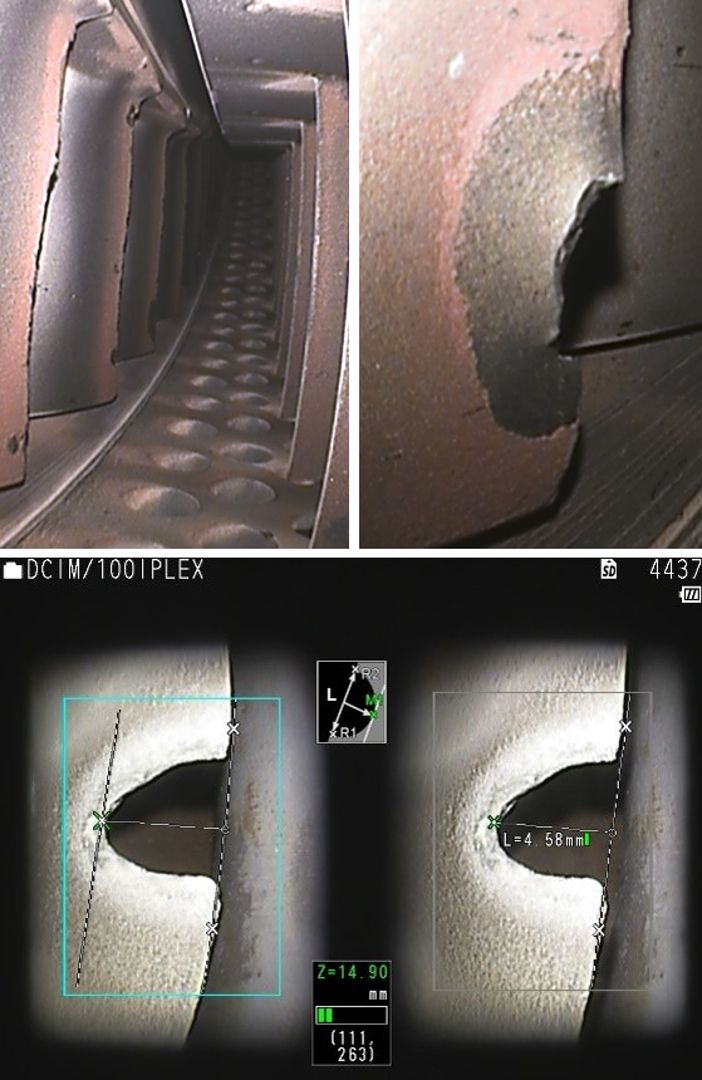
Evidence for repairs
Detailed reports, including images from the borescope were provided to the aircraft operators. Ward says, “The ability to take precise measurements and to support them with high quality images and video means that our clients are able to make important decisions with the highest degrees of confidence.
“There are basically three possible outcomes from an inspection. The aircraft may be given a clean bill of health to continue flying, or it may be authorised for a single flight back to base so that repairs can be undertaken. Or, as was the case in Kigali, the aircraft was grounded so that the engine could be replaced.
“The repair bill for this engine is likely to exceed US$1 million, so it is extremely important that the operator is provided with accurate, clear evidence of failure, and the IPLEX NX is essential for the achievement of that goal.”
Written by Steve Drake, Ashtead Technologies NDT Market Manager and has over 35 years of non-destructive testing experience, mostly with Carestream and Kodak Digital NDT.