Many engineers around the world have been forced to work from home because of restrictions put in place to stop the spread of the Covid-19 virus. The pandemic has forced companies that previously only let engineers work on-site to let them work from home.
Evidence of this is that while in lockdown, the home use of computer aided engineering (CAE) software has increased, with suppliers of modelling and simulation software, such as MSC Software, noticing a significant increase in the use of their products from home.
MSC’s Multiphysics modelling and simulation software is used throughout industry, but one of the company’s largest customer bases is in aerospace.
Engineering at home
Roger Assaker is CEO at e-Xstream engineering, which became part of MSC Software in 2012 and is MSC’s chief customer engagement officer.
“Luckily we are in the virtual world and don’t need to do a lot of prototyping and testing. All you need to do simulation is a computer, a software license and knowledge,” said Assaker.
MSC Software is helping companies around licensing restrictions to enable home working. A software license is related to the location of the company, but MSC Software has removed geographical restrictions. Where access to a company’s license server is restricted for security reasons, MSC is offering an emergency license server for people to use. The company’s support teams have also been redirected to prioritize helping people working from home.
Finally, MSC is offering free access to its e-learning resource center for as long as Covid-19 confinement continues. “We’ve seen a lot of uptake. Our e-learning is being used 30% in Asia, 20% in the US and 50% in India. 20% of the courses accessed have been about aerospace. On our license server 25% of the access is coming from the US and 30% from France, with the majority working in the aerospace sector,” said Assaker.
Remote access
Stress engineers, acoustics engineers, materials and process engineers alike can use CAE at home, remotely access the data they need to design in 3D and run simulated tests on the models using multi-physics simulations.
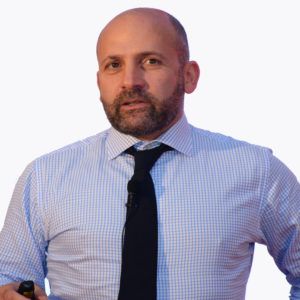
A laptop is capable of pre or post-processing a model and doing some visualizations. Typically, high performance computers (HPCs) are used in the office. Some simulations, such as for additive manufacturing or a full evaluation of an aircraft, require a lot of resources. However, users can access their own HPC through a VPN, or use cloud computing for extra processing power.
“You can do almost anything apart from go to the laboratory and perform a physical test on material product prototype or some kind of inspection with a CT scan or some other NDT. The results of tests can be analyzed at home, but at some point, if you don’t have the data, you need to create a coupon and test it on a machine,” said Assaker.
A lasting change?
Anecdotally, it would seem that most companies can cope with more people working from home. Assaker believes that handling the change in working arrangement will be important as the pandemic progresses.
“In traditional large manufacturing companies, you have to go to the office every day. It’s these companies, that are being forced to have people work from home, where it will show that you can be more efficient than at the office by saving time on travel and personal interactions. So, we are seeing an increase in the amount of simulation being done,” said Assaker.
Furthermore, he believes that when chief financial officers and CEOs see that travel and entertainment spending is shrinking and the same work is being done, business travel and commuting will be impacted. “I think some of these changes will last – the companies that were reluctant will allow home working and save on office space and expenses – why not?”
New materials
The light weighting of aircraft and their components to reduce CO2 emissions is still the general goal in aerospace. This is mainly being achieved through the use of new materials.
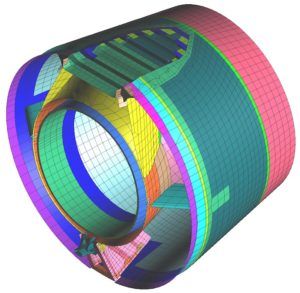
However, the cost and effort involved in using new materials in aerospace applications is very high. The use of modelling and simulation can help reduce that.
The narrowing down of suitable materials for a part or structure can be achieved using parameters that are tested in the “virtual world” with models and simulation, reducing the time spent on physical testing and prototyping. For example, with a 3D woven composite it can take two months to choose the architecture and cost US$40,000. With modelling and simulation, the same can be accomplished in half a day.
Another major driver in the sector, at least pre-Covid-19, has been the aim of improving the cadence and cost of manufacturing by refining the material choice and automating and improving manufacturing processes. Assaker is technically focused on integrated computed materials engineering (ICME), where the aim is to assess how manufacturing has influenced a material’s microstructure and the final part performance.
“Within our ICME concept we try to connect manufacturing to the material to the part performance, for example introducing the use of chopped fiber thermo plastics and injection or compression molding in aerospace from automotive, which can save up to 30% of costs on the part and up to 20% on its mass,” said Assaker.