While some would prefer to inhabit a world free from agricultural chemicals, it may not be a world where farmers could feed a potential population of 12 billion by 2100. Chemical treatments including pesticides, herbicides, fungicides, and fertilizers must be applied at scale to support yields sufficient to slake humanity’s voracious appetite.
Crop-dusting or aerial application, whereby contractors spray vast tracts of land with purpose-built aircraft, is a market worth US$6 billion worldwide – US$3 billion in the USA alone. The European Union outlawed most crop-dusting in 2009, meaning European farmers must rely on self-propelled or tractor-drawn ground-based sprayers.
Crop-dusting costs more than running a sprayer, but rapidly covers ground. “Tractors cause crop damage,” says Nathan White, head of flight operations at autonomous UAV developer Pyka. “They can’t run in wet or boggy conditions, or through higher crop canopies.”
Aircraft cause zero soil compaction and are untroubled by ground conditions, but present other limitations. “Because they have smaller tanks, crop dusters have limited application rates,” says agricultural machinery manufacturer New Holland’s crop application specialist, Alex Caldwell. “Ground rigs are more precise. Farmers can control exactly when the chemical is applied without being subject to a crop duster’s schedule.”
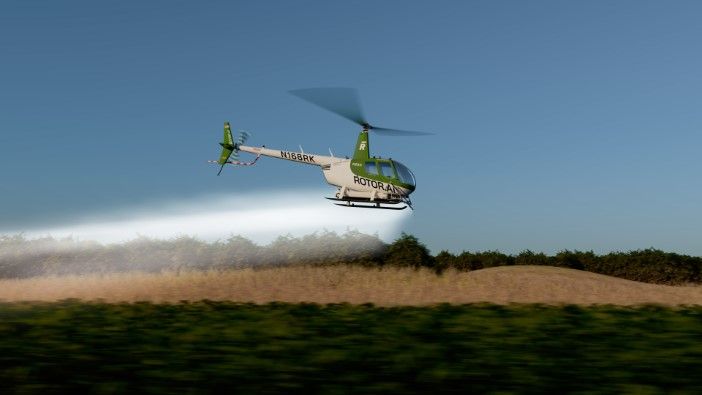
Saving lives
For crop dusters, meeting demand depends on pilot availability. “Pilots flying 20ft above ground at 100mph and pulling up sharply to avoid trees or poles are killed more often than police officers,” says co-founder and CEO of engineering firm Edison Aerospace, Gene Avakyan. “It’s like flying a combat mission.”
Saving lives is motivating companies like Pyka and Edison Aerospace to develop UAVs large enough to replace piloted crop-dusting aircraft. Pyka’s 38ft (11.5m) -wingspan Pelican Spray is an electric UAV with 620 lbs (280kg) chemical capacity. Purpose-built for agriculture, it travels at 70 to 80mph (112 to 128km/h), spraying 160 to 210 acres/hour in 59ft (18m) wide swathes. Already operational in Brazil, Costa Rica and Honduras, in 2023 it became the largest UAV to obtain FAA authorization for commercial operations.
Pyka analyzed different aircraft applications to find those most suited to electrified autonomy. “Crop-spraying was the resounding winner,” says White. “Range, the one downside of electric aircraft, just isn’t an issue, since crop-dusters can easily swap batteries when landing to refill chemical tanks. Spraying is also dangerous and requires repetitive precision, something robots excel at.”
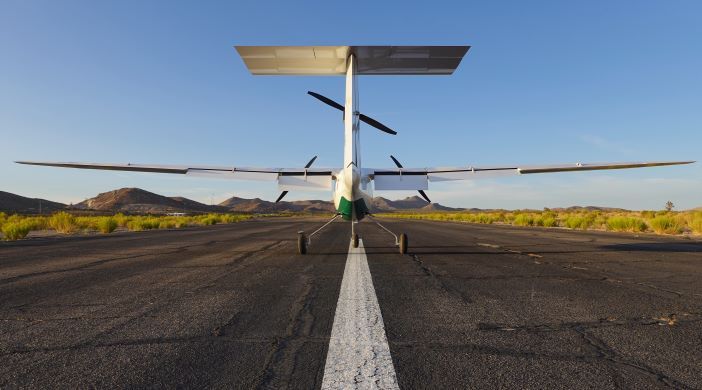
Application-specific design
Pelican Spray’s distributed architecture ranges four electric motors across its wings, providing 100kW of total power to composite, fixed-pitch propellers. If a motor experiences an outage, the plane can safely continue its mission. Distributed propulsion also delivers a cleaner airflow.
“A traditional aircraft’s single nose propeller creates a downwash which disturbs spray from the boom, but our propwash stays above the boom,” White explains. The Pelican needs only a 600ft runway, far shorter than gas turbine aircraft thanks to its superior peak power-to-weight. It doesn’t use visible light to fly, enabling nocturnal operation.
“In Costa Rica, flying at night is too dangerous and the days too hot for spraying. Pilots are limited to narrow, windows during dawn and dusk and have to tolerate less-than-ideal wind conditions to avoid chemical drift. Pelican Spray allows them to apply at night, when winds are low and many plants absorb chemicals more efficiently.”
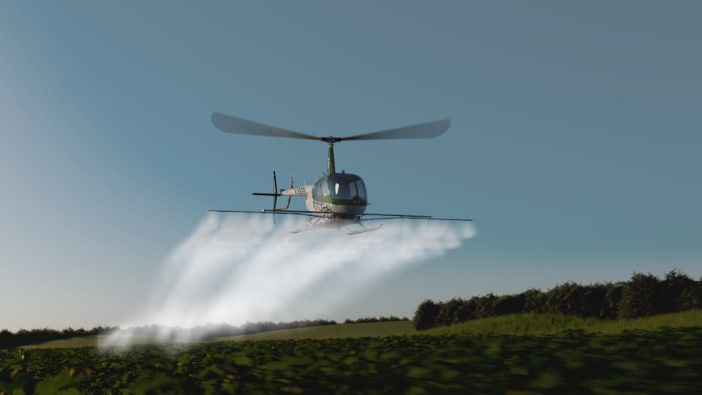
Six processors on two separate computers process millions of sensor inputs per second. Redundant inertial measurement units and air data booms replicate a pilot’s instruments and orient the aircraft. Forward-facing lidars for obstacle detection and downward-facing 3D lidars for field-scanning work are separate systems each with self-contained logic.
“Each mission begins with a scan-pattern flight at 100m,” White says. Downward-facing lidar captures and condenses all the obstacles and topography into a map. “The plane then computes a path based on a required spraying polygon and takes off and lands autonomously.”
A previous Pyka aircraft, the Egret, was certified for commercial operation in New Zealand. Swapping from tail wheel to nose wheel landing gear between the Egret and Pelican eliminated directional stability and yaw control issues. “We used an iterative development process light on simulation and reliant on real-world flight-testing,” says White.
Structural ground tests subjected wings to the loads they would encounter in aggressive maneuvers or gusty conditions. “We had some prototype wings fail load testing, made corresponding design changes, and now have a solid structure locked in.”
Certification efforts entailed prescriptive flight-test campaigns. New Zealand’s regulators interrogated the Egret’s stall characteristics, maximum speed and stability conditions across forty flight hours. The FAA began by reviewing the Pelican’s concept of operations.
“That determined how rigorously they needed to regulate it,” White explains. “Our proposed mission, flying low in sparsely-populated areas, has low air- and ground risk.”
After this an exhaustive review of Pyka’s flight, maintenance and training manuals, with FAA departments suggesting improvements was done. FAA flight tests focused on emergency procedures outlined in the flight manual. Pyka injected faults by disabling a motor, sensor, or servo, to ensure system logic responded correctly and safe flight could continue. “It’s about showing the airplane handles potential failures as described,” says White.
FAA approval means the Pelican may be flown by operators with an exemption certificate, but not yet by individual farmers and Pyka delivered its first US plane to Heinen Brothers, a Kansas crop-spraying service provider in February 2024, after a three-year certification process, although certification in other regions should be faster. Certification in Costa Rica and Honduras resembled the FAA process, whereas to promote a technology perceived as low-risk, Brazil allows agricultural drones to operate without an airworthiness process.
Pyka conducts ongoing flight-tests in central California to validate software updates. “We have a certificate of authorization and run operations five days a week, all year round,” says White.
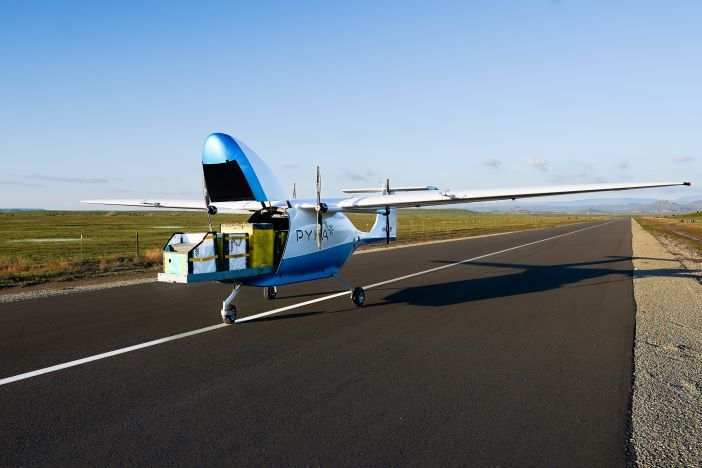
Market growth
According to Edison Aerospace, its Heavy 1 electric UAV will be cheaper to build than the Pelican with off-shelf components and offer a more competitive 200 gallon payload. “Pyka created a Rolls Royce, but we want to make a Ford,” says Edison CEO, Gene Avakyan. “Something simple, robust and widely affordable — a tractor that flies.”
The 40ft (12m)-wingspan Heavy 1 will also leverage distributed electric propulsion. Its architecture features four propellers across each wing driven by eight separate motors. “That creates a blown-wing effect, improving the airfoil’s efficiency and allowing it to fly more slowly without stalling,” says Avakyan. “It eliminates the P-factor, whereby increasing RPM creates a spiraling airflow which causes single-propellor aircraft to yaw to one side.”
Avakyan’s airframe design is patent-pending and he is seeking funding for a half-scale prototype, having developed a semi-autonomous flight control system using open-source software. “It’s a human-in-the-loop system which automates takeoff and landing,” he explains. “A pilot controls it remotely, but if they let go of the sticks, it automatically levels itself to fly steady.”
Avakyan has so far flight-tested in Florida with 2ft (0.6m) models. “We used generic aircraft because our goal was to test navigation and flight control systems not the propulsion. I have no doubt about that, because NASA has tested similar propulsion technologies and all the numbers work.”
Once built, Avakyan plans initial flights under an experimental license with a pilot flying the Heavy 1 from a trailer-based ground control station. A person will remain outside to maintain visual line-of-sight.
Crop-dusting operators represent Edison’s target customers for an aircraft intended to replace their conventional planes and be flown by commercially-licensed pilots from a cockpit-like control station. By contrast, the Pelican can be operated via a laptop after some basic training and may be marketed to operators or directly to large farms.
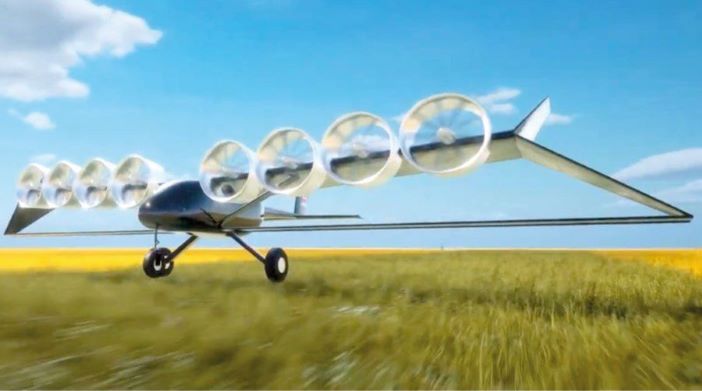
The backdrop to Pelican Spray’s advancing deployment is an emergent US market in smaller UAVs with spraying capabilities. Developed in partnership with Chinese manufacturer XAG, a New Holland drone spraying solution showcased alongside the Guardian will be available to Brazilian customers in 30 litre and 70 litre models later this year.
“The New Holland Spraying Drone completes a 30 litre to 4,500 litre range of spraying solutions aimed at every type of producer,” says Eduardo Kerbualy, New Holland’s vice president for Latin America. It is expected to excel on smaller plots, uneven topographies and fields inaccessible to tractors following rainfall.
John Deere and German multirotor drone company Volocopter started working together on an agricultural drone in 2019, but Volocopter paused its pursuit of agricultural applications precluded by European regulations. While skeptical about the precision of small UAV sprayers, James acknowledges the potential for UAVs in scouting applications like providing weed maps to inform ground-based spraying.
“The problem then is data-processing time,” says Caldwell. “If a drone produces a weed map for a 160-acre section, the file may take so long to download that new weeds have appeared in the meantime.”
Pray and spray no more thanks to academic researchers
Chair of agricultural and biosystems engineering at North Dakota State University, professor Leon Schumacher is assisting Edison Aerospace in testing the spray performance and operation of its proposed Heavy 1 autonomous aircraft.
“A field sprayer may have 15 or 20in nozzle spacings, but an aircraft may need nozzles 6 to 9” apart to reduce the impact of winds on the spray pattern. Spray width is generally three quarters of the wingspan, from which we can determine the required pump size. We need to keep product agitated in the tank, so it remains suspended to produce a uniform application.”
Pyka’s Pelican Spray UAV crop-duster combines variable-speed rotary atomizers with a high-speed centrifugal electric pump in a spray system allowing users to adjust the flow rate and droplet size for optimal application efficiency. Iterative flight tests may perfect the spray patterns delivered by Edison’s system. “We can put water-sensitive paper at different locations in the field to test uniformity of application across the boom,” says Schumacher.
Schumacher argues that Edison should aspire to incorporate sense-and-act technology capable of detecting and spraying individual plants to provide an environmentally friendly and range-extending solution. “It wouldn’t be impossible in a two-drone approach, with a smaller drone first spotting the weeds to generate a prescription for the aircraft applying the product.”
Schumacher observes that the FAA currently prohibits the use of spraying drones above 50lbs in total weight without a special license. Depending on application rates, this may only provide the capacity to spray a single acre. “We should think more about spot-spraying, combining additional drones with AI to pinpoint trouble-spots and apply product only where needed,” he says.
World’s largest agri-spray drone unveiled by US company
Equipped with 33ft (10m) booms and a 110 gallon (500 litre) capacity tank the new Sprayhawk drone is being classed as the biggest agri spray drone on the market.
Designed and developed by Rotor Technologies, based in New Hampshire, USA, this new UAV has just been released onto the market with a hefty introductory price tag of US$900,000.
The machine is based on a full-sized Robinson R44 helicopter and is fully controlled by a two man operator crew on the ground.
With a spray rate of 240 acres per hour, the Sprayhawk can take off and land vertically. It features autonomous spray path and terrain following algorithms, as well as camera and LIDAR sensors for detecting wires and avoiding obstacles.
Powering the Sprayhawk is a Lycoming six-cylinder aviation engine that can propel a spray rate to over 80mph (112 km/h). It has a flight time of 50 minutes between refuelling.
Impressively, the Sprayhawk matches the spray speed and capacity of manned aircraft, while offering significantly lower operating costs and improved safety.
Rotor’s CEO Hector Xu said, “The Sprayhawk represents a leap forward in agricultural aviation. We’ve combined the capabilities of a full-scale helicopter with the cost-effectiveness and safety of a drone. There’s nothing else on the market that’s as productive, reliable, and future-proof as this.”
Rotor was founded by a team of MIT aerospace engineers and aerospace industry veterans. The company manufactures the most capable commercial UAVs in the world, designed for challenging and dangerous missions like crop dusting, aerial firefighting, and utility work.