Several technologies and methods are used to test a material’s capability to withstand the extreme temperature fluctuations, pressure differentials and vibrations it will experience during flight. Engineers also assess a material’s ability to resist corrosion to ensure reliability and longevity using long-duration exposure to extreme conditions.
One of the key methods for evaluating the long-term performance of new and existing materials used in the aerospace sector are tests to assess their ability to withstand extreme changes in temperature during flight. This includes the high temperatures near engines and the low temperatures at high altitudes.
According to Chris Bowles, environmental test supervisor at global product testing and certification organization TÜV SÜD, laboratory testing for temperature extremes and temperature fluctuations is generally performed in climatic chambers that have a temperature range matching or exceeding those found in flight.
“For commercial aircraft, temperature extremes of -55°C to +85°C and rates of change of 10°C per minute are common. Achieving these temperature extremes and fast temperature transitions requires complex refrigeration plant and often liquid nitrogen injection,” he says.
Typical test methods, test temperatures and rates of change in temperature are detailed in standards like RTCA/DO-160. These are derived from known natural environmental meteorological conditions and induced environmental conditions, which vary depending on the position and application of an aircraft.
“In some development projects, compliance with a standard is not required. In these cases, temperature extremes and fluctuations may be increased outside of those defined in the standards.
“The objective in these cases is to accelerate the aging of the sample, identify failure modes and understand the absolute limits of the materials in and beyond its useful life,” says Bowles.
Elevated Temperatures
Another company with a range of experience in temperature testing is Germany-based maker of materials testing machines ZwickRoell. As Hannes Körber, global industry manager for composites at ZwickRoell explains, since the mechanical response of fibre-reinforced polymer matrix composites is strongly affected by temperature, the composites used in aerospace structures need to be tested at low and elevated temperatures.
Moisture uptake over the lifetime of a composite structure is also known to have a detrimental effect on mechanical behavior and material properties. Körber notes that standardized static testing is carried out to obtain the mechanical response of the composite lamina, and for multidirectional laminates at different temperature and moisture levels. The exact temperature regime depends on the scope of application, with a typical temperature and moisture range for aviation structures from -55°C (-67°F) dry to 121°C (250°F) wet.
“This covers the temperature range from during flight at cruising altitudes to elevated temperatures on the ground in hot climates,” says Körber. “For the wet testing condition, the test coupons are conditioned for several weeks until moisture uptake in the material has reached an equilibrium.
“The moisture conditioned samples are then tested at the desired temperature using a static testing machine with temperature chamber.”
Typical static tests include unnotched tension and compression, in-plane shear or short beam shear strength, open and filled hole tension and compression, pin bearing, and curved beam strength or compression after impact.
For metal materials like those that are used in aircraft engines, the temperatures for typical elevated temperature tensile tests are much higher compared to what is necessary for fibre-reinforced polymer matrix composites.
“Elevated temperature tensile tests on metals can therefore go up to 1200°C. A wide temperature-range from low temperatures up to 1200°C can then be achieved by combining a static testing machine with a standard temperature chamber and a hot temperature furnace,” says Körber.
Under pressure
In addition to carrying out comprehensive temperature tests on a range of samples of composite materials extracted from fiber-reinforced carbon or glass fiber panels, Element Materials Technology also subjects on-board systems and other aerostructures to both negative (vacuum) and positive (overpressure) pressure cycling. Here, the equipment or structures are assembled into a test bench that simulates real operating conditions for a material’s whole operational life.
“This is achieved with perfectly synchronized flow control valve systems and pressure sensors. It is common to combine such a system with mechanical or thermal loads and to intersperse unexpected overpressures during this cycling to assess damage tolerance,” says Rocio Ocaña, technical manager – materials testing at Element.
“Structures are periodically inspected during the test to ensure that they are
not damaged or that damage is of an acceptable level.”
Meanwhile, at TÜV SÜD, altitude chambers are used to test components at different pressures. These sealed chambers use vacuum pumps to reduce internal pressures to those encountered during flight. The chambers also simulate unusual or unplanned events that may happen during flight, like rapid or explosive loss of cabin pressure. In these cases, components and assemblies need to demonstrate an ability to survive the event and remain fit and serviceable to land the aircraft.
“These types of events are more challenging to accurately replicate using computer simulations, and too risky to perform in flight trials, making laboratory trials an essential part of development and compliance,” says Bowles.
All shook up
Vibration tests are run using shakers. These electrodynamic devices drive recreate vibration test profiles as defined in standards such as RTCA/DO-160 or MIL-STD 810, or at aircraft specific levels. Vibration profiles are generally confined to Sinusoidal, Random, Sine on Random, Mixed Mode, and Shock, and replicate the mechanical vibrations found in flight and any unplanned flight events.
“A challenge for the laboratory team is the mounting of the sample, so it can faithfully transmit the vibration profile. The ideal mounting fixture transmits the vibration into the sample in an identical manner to which it would if in service. Accelerometers are responsible for closed-loop control of the vibration profile and to take response measurements directly off the sample during test,” says Bowles.
“Any change in response measurement can indicate the onset of failure. Many failure modes may be observed during a vibration test, so it is equally important to clearly define pass-fail criteria, ensure that sufficient performance assessment data is captured, and evaluate the sample performance during and after the vibration test,” he adds.
Dynamic Testing
Servo-hydraulic testing machines are commonly used for dynamic materials testing because of their versatility in terms of load range and testing frequencies. “If needed, they can also be used for static testing,” Körber says.
For the load range of 100kN, typically used for fatigue testing of metals and composite materials on the coupon level, ZwickRoell has developed a compact dynamic testing machine with an integrated hydraulic power pack. As Körber explains, the compact design makes the machine independent from a centralized hydraulic supply, so it has a lower footprint compared to setups where a separate hydraulic power pack is placed next to the machine and operates at a noise level of less than 58dB.
“An integrated cooling system prevents heating of the laboratory and an integrated power pack serves as a substructure for the storage of an also available temperature chamber for non-ambient testing when not in use,” Körber says.
Moisture and Humidity
Another important type of laboratory test, known as fluid susceptibility testing, assesses a sample’s capability to withstand the effects of exposure to fluids. According to Bowles, the fluids selected for such tests are those that may have contact with the sample in its final installation, including aviation fuel, hydraulic oil, cleaning products, or even beverages such as coffee or cola. “During testing, fluids are applied to the surface of the sample and conditioned at an elevated temperature to accelerate material degradation effects. At the end of the test an assessment is made,” he says.
Since composite materials are hydroscopic, Ocaña stresses that it is important to assess the influence of humidity on their mechanical and physical properties. During the material qualification phase, samples at Element are exposed to moisture absorption in climatic chambers before testing. These chambers remain at constant and moderate temperature and humidity, typically around 70°C (158°F) / 85%HR until the material is saturated in water. To control moisture absorption witnessing samples – geometric squares from the same plates as the specimens – are introduced in the chamber and weighted at regular intervals.
“The equilibrium criteria are defined by formulae based on the difference between weights. During the conditioning, mass increase is monitored through tabular data and graphical representation and when the equilibrium criteria is reached, the material is ready to be tested,” says Ocaña.
Composite materials on an aircraft may also be exposed to other chemicals like hydraulic fluids such as skydrol, jet fuels or even cleansing agents that could be reactive.
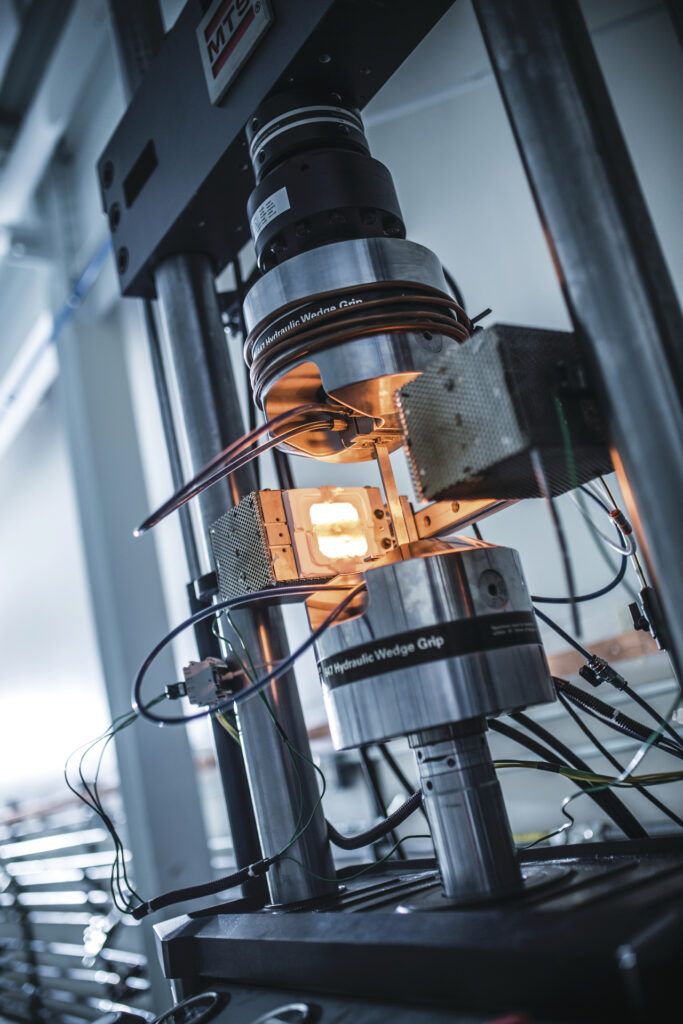
“To consider how these chemicals affect the properties of the materials, a set of samples are immersed in the different fluids and tested when they reach the number of hours required by the material specification,” Ocaña says.
“For certain moving structures, such as wing flaps, it is common to perform dynamic testing where flap movement is combined with the application of water and dust during the movement, to ensure that no wear is caused that could affect the performance of the flap,” she adds.
Creep Testing
To ensure reliability and longevity under long-duration exposure to extreme conditions, such as prolonged exposure to high-temperature environments, high-temperature metals are also creep tested to obtain creep limits and strengths for different temperature levels.
“This helps engineers select the right material for a specific application and provides suitable data for the design of high-temperature structures,” Körber says.
Uniaxial tensile creep testing is carried out according to ISO 204 and ASTM E139 standards. For creep loading of more than 10,000 hours, electromechanical creep testing machines can be used, which further allow strain-controlled fatigue testing as per ASTM E606 and creep-fatigue testing as per ASTM E2714. For extended creep testing of up to 100,000 hours, a low-maintenance lever arm creep testing machine can be used.
“The mechanical load bearing capacity of ceramic matrix composites is tested at ultra-high temperatures of up to
2,000 °C. This involves evaluating the suitability of CMCs for specific applications using tensile, compression, shear, flexure, creep and creep fatigue testing,” says Körber.
“To ensure that CMCs are tested under real operating conditions, these destructive test methods are carried out in vacuum and inert gas conditions in a temperature range from 650°C up to 2,000°C.”
Recreating Extreme Conditions
Moving forward, one of the latest advances in the specialized testing equipment and facilities used to recreate extreme conditions in the laboratory is the recent addition of a cryogenic testing cryostat at the NLR testing facility in the Netherlands. This machine enables users to test coupons at -253 °C (-423.4°F), while applying a tensile or compressive load to measure the failure stresses of the material at these temperatures. The machine is effectively both a testing machine and a thermal testing chamber.
Hosam Ebrahim, senior project engineer at NLR says, “By vacuuming the inner chamber of the cryostat,
pre-cooling it with nitrogen, supported by a cold finger [a piece of laboratory equipment used to generate a localized cold surface], then further cooling it down to -253 °C, we can perform the mechanical tests as required.
“The cryostat is a vacuum-insulated environment that uses liquid cryogens to cool the temperature of a sample,” he adds.
Elsewhere, one of Element’s latest advances in the qualification of novel aircraft structures is multi-axial test rigs that enable the application of operational conditions load cases synced with inner pressure for full-scale sized structures.
“These test rigs combined with bespoke environmental aging capabilities and are used to proof novel structural concepts by validating static and dynamic service loads, as well as an airframe’s damage tolerance,” Ocaña says.
Meanwhile, Bowles highlights ongoing advances in the control and data logging software driving equipment, as well as in amplifier technology, which has seen efficiencies pushing above 90% compared to where they used to sit at around the 50% mark.
Looking ahead, Ebrahim observes that developments in composites technology and additive manufacturing are increasingly assessing the performance of materials in cryogenic conditions (sub -200 °C).
“Research opportunities in hydrogen technologies are emerging, due to environmental initiatives. Chemical behavior and permeability with hydrogen is increasingly important too,” he says.
Ocaña believes the sector is united in its efforts to continue to improve composite airframes, reducing weight and improving fuel efficiency. “It is a vital process as we shift to greener aviation. Ceramic Matrix Composites, or thermoplastic-based composites are great examples of technologies showing promise in important aspects such as hot environment performance, recyclability, and repairability,” she says.