by Paul Willis
With airlines still reeling from the economic repercussions of the global pandemic the next few years will be a time of belt-tightening for the aviation industry, placing pressure on maintenance, repair and overhaul departments.
Part of the solution is predictive maintenance – engineers and technicians within maintenance, repair and overhaul (MRO) are increasingly relying on predictive maintenance techniques to identify and manage problems in aircraft in advance.
Among these techniques, vibration-based condition monitoring is one of the most important. Vibration is a common problem on aircraft, both in the airframe but most significantly in the propulsion systems. Most modern jet engines are comprised of two or three concentric shafts inside of which are the compressors, fans and turbines. Known as spools, these shafts are aerodynamically coupled, meaning that each spool rotates at a rate variable to its fellow spool.
The larger the diameter of the spool section “the more sensitive it is to vibration,” says Ken Ameika, executive director of global sales at MTI Instruments, a global manufacturer of condition-based monitoring systems. Ameika gives the example of the Boeing 737 engine, the CFM56 turbofan engine that was created by CFM International.
According to Ameika this engine is “most vulnerable to vibration at the fan, in the engine’s front, and at the low-pressure turbine in the rear section, since these are the largest diameter sections of the engine.”
Vibration can be caused by an imbalance in one of the engine’s blades affecting the rotation, leading to vibration. Even a tiny imbalance can have an impact. “The diameter is large and the rotational velocities are high, so an imbalance of only a couple of grams on one of the engine’s 24 blades would result in vibration,” he says.
The imbalance can be due to a number of factors: burns, dust, or just general wearing down of the blades over time. The impact of engine vibration on the aircraft varies in severity, says Ameika.
At its more benign level it can result in discomfort for the airline crew. Left untreated for too long the vibration begins to put stresses on the bearings and seals within the engine and in the worst-case scenario “you could have in-flight shutdown, where the engine needs to be shut off and the airplane must operate on one engine until it makes an emergency landing at a local airport,” says Ameika.
Sensors and analysis
Routine vibration analysis is carried out on aircraft engines to check that vibration levels are within tolerable levels mainly using two types of sensors: tachometers to measure the rotational velocity of the spool in revolutions per minute (rpm) and vibration sensors attached to the engine case.
Newer, larger commercial aircraft tend to come already fitted with most of this sensing technology. But for older and smaller airplanes it may need to be retrofitted, says Ameika. There can be up to six vibration sensors fitted on each engine. This allows staff “to identify where in the rotational cycle vibration is and get an approximation as to where exactly in the engine it is,” he says.
Data from the vibration pick-ups and tachometers is then fed through complex algorithms to give a detailed picture of the vibrational health of the engine. Ameika says, “We measure the vibration as the spool turns. So, if you were looking at it in slow motion you would see that we’re actually measuring vibration through a full rotation.
“There is an immense amount of algorithmic horsepower in the analysis software that allows us to both isolate the location of the vibration as well as its overall magnitude.”
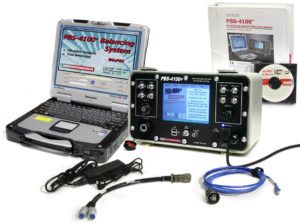
The vibration analysis is carried out whilst the aircraft is on the ground using one of MTI’s data acquisition units – small, lunchbox-sized systems that connect directly to the aircraft’s on-board hardware. Since not all jet engines are configured in the same way, the user is prompted to identify the engine type and the unit retrieves the operating characteristics for that engine.
The engine is then started up and the analysis carried out. When the survey is complete the unit will output a report, showing where any imbalance is located and providing a balancing solution. Re-balancing is mainly achieved is by adding weighted bolts as counterbalance. To explain this concept Ameika uses the metaphor of children on a merry-go-round. A second vibration survey is then conducted to verify that the re-balancing has resolved the vibration.
A vibration survey and balancing of an engine can be achieved within a couple of hours. Just 20 years ago a vibration survey would have grounded the aircraft for at least a day and often required the involvement of specialists, says Moshe Binyamin, MTI Instruments’ president. “If you look at the units from 20 years ago, you’ll see they required manual entry of very technical data,” he says. “Today, as long as you know where to connect the connectors everything uses a graphical user interface. This reduction in complexity means less expertise is needed to operate and successfully perform balancing.”
Health monitoring
There is growing recognition within aviation of the economic gains that predictive maintenance technologies can bring. For example, a recent study by the US Army’s Third Aviation Brigade found that health monitoring systems installed on its fleet of Apache helicopters had helped reduce mission aborts by 30%, cut maintenance test flights by the same figure and reduced the need for scheduled maintenance by up to 10%.
The systems installed on the Apaches were health and usage monitoring (HUMS) hardware developed by United Electronic Industries (UEI). Like MTI’s data acquisition units, a HUMS device pulls raw data from the aircraft’s on-board sensing technologies. The raw data is collected from more than 100 different signals which can be downloaded and run through analysis software on the ground.
Among these datasets the most important relate to the helicopter’s powerplant, says Chris Hallinan, a senior sales manager for UEI. Hallinan says, “It includes engine operating parameters like temperature, pressure, oil temperature and pressures and rpm. When you get to turbines the inlet temperature is a critical parameter because typically the hot section of a turbine engine is running at or near the limits of the metals that it’s made out of. There are probably a dozen parameters for a given engine that are critical to flight safety.”
There also many datasets collected relating to the airframe itself, which is usually outfitted with various sensors to measure airspeed and the aircraft’s altitude, velocity, direction and position among other things, adds Hallinan.
In order to detect anomalies from any of these channels the hardware needs to be sampling data at a rate of at least every two seconds. With so much sampling going on, each flight generates large quantities of data, which can only be handled due to advances in processing technology. Erik Goethert, senior director of business development and strategic marketing at UEI says, “Today’s processing technology is smaller, uses less power and is more powerful, meaning that you can now apply these large algorithms to huge datasets to identify anomalies What you would have had to do on a mainframe fitted with multiple processors, you can now do in the palm of your hand with a smartphone.”
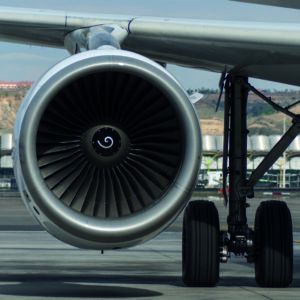