The aero-engine manufacturer’s director of development and experimental engineering – civil aerospace, details the physical design challenges of Testbed 80 and its links to the virtual world
Q: What was the main design challenge with Testbed 80?
Our most recent engine, the Trent XWB-97, has increased thrust compared to other recent engines such as the Trent 1000-TEN and Trent 7000. Our UltraFan demonstrator will also be within the known thrust range, but a larger fan diameter will require a greater mass of air to travel through the bed.
Testbed 80 has therefore been designed using the latest techniques to improve the aerodynamic performance of the bed, which will deliver an undisturbed flow of air to the engine. As well as delivering air to the engine, the design of the testbed focuses on removing energy from the exhaust, which ensures the testbed runs silently. This is important as we run a 24-hour operation at our site in Derby.
Q: Do larger engines have any other effects on the physical testing process?
The testing process is the same for engines with a larger fan, but by having a larger testbed the engine has to have sufficient clearance from the walls and floor to avoid any interaction when carrying out performance testing.
Our most recent and future engine demonstrators have larger fans which move air slower than previous engines. As the airflow speed is slower, it becomes more challenging to draw in and move sufficient air to achieve a stable operation and avoid damaging aero-acoustic phenomena such as ultra low frequency (ULF) tones.
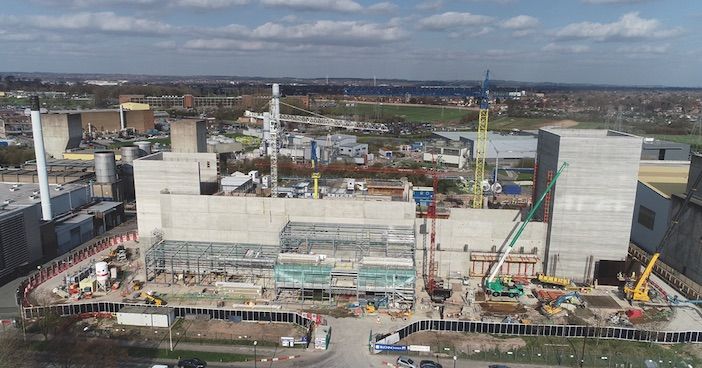
Q: Can you describe the digital technology the new test centre
will use?
Testbed 80 will be the first of our testbeds to transmit data directly into our secure cloud environment. This will allow us to link the physical and functional data we measure with our analytical models, which form the engine’s digital twin. To achieve this, Testbed 80 will be fitted with a next-generation digital data acquisition system, which will enable emerging new measurement and signal conditioning technologies to be integrated seamlessly.
It’s a natural progression as we continue to invest in more representative models of our engines, which are linked to the physical and functional data from our development engines, as well as those in service. This approach also supports our continual move towards physical testing being used to validate the integrity of the digital model.
Q: What are the benefits of having a digital twin?
The ability to carry out virtual testing of the engine and facility, before any physical testing. It allows us to assess multiple design solutions, leading to product design optimization in a reduced period of time, and significantly reduces uncertainty when we carry out the physical test.