In this Q&A with Manuel Vögtli, head of business development at Kistler’s Test and Measurement Business Unit, the topics of discussion include how to best select different types of sensor and instrumentation for different applications and how engineers are innovating to test drones and VTOLs .
Q: Which sensors and DAQ equipment from Kistler are used for aerospace testing?
A: We have a broad portfolio of products backed by a long track record of working in the aerospace sector all around the world. We draw on our accumulated industry expertise to offer a tried-and-tested range of force, torque, pressure and acceleration sensors specifically designed for aerospace testing. These sensors are based on several technologies: piezoelectric (PE), integrated electronic piezoelectric (IEPE), strain gauge, and piezoresistive (PR).
Aerospace testing covers a variety of functions: for example, drone and VTOL testing covers mechanical, electrical and optical aspects, RF/IF communications and operational conditions. Solutions from Kistler are especially appropriate for mechanical and operational or environmental testing.
We offer the entire measurement chain from sensors and cables through to DAQ and software. Our range includes sensors for single and multicomponent forces (PE/IEPE), pressure (PE/IEPE and PR), acceleration (PE/IEPE/MEMS), rotary torque (strain gauge) and also reaction torque (PE).
Our signal conditioning portfolio comprises analog laboratory charge amplifiers as well as multipurpose integrated amplifiers/DAQ units with LabAmp technology, the KiDAQ data acquisition system and jBEAM analysis software. Integrated signal conditioning /DAQ technology from Kistler features simultaneously sampled and scalable 24-bit solutions with each channel synchronized to better than 1 µsec.
Q: What type of testing is performed?
A: The aviation industry uses our products for ground and flight testing during the development phase and for upgrades and certifications across all operational scenarios. The scope includes ground vibration testing, tests on aircraft landing gear, brakes and hydraulic systems, the jet engine itself, flight vibration testing and also wind tunnel testing.
Space testing covers an equally wide range including environmental vibration testing for space payloads, micro-vibration and jitter testing, rocket engine tests and thermal vacuum chamber testing.
For tests on drones and VTOLs, sensors can be mounted on the fuselage, control surfaces, propulsion system, landing gear and brakes, the payload release mechanisms or the ridged body motion at the center of mass.
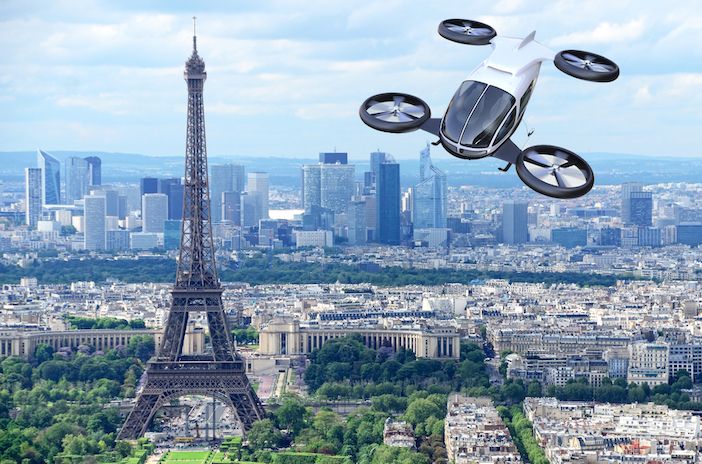
Ground testing can include structural vibration tests on propulsion systems – for instance, measuring the vibrations of propellers after they are integrated into the aircraft structure. Other examples include wind tunnel testing to assess aerodynamic loads, the use of force dynamometers to measure multicomponent thrust and moments, and also component and subsystem tests.
Our equipment is also used extensively for in-flight testing. Aspects covered here include landing loads and structural integrity, propulsion system /propeller imbalance, dynamic in-flight vibration, turbulence / buffeting (including maneuvering and control surfaces), the effects of ordinance / payloads, low altitude/low airspeed deployment, and high-altitude vibration testing at temperatures well below –55°C.
Our sensors have been tried and tested at high altitudes based on the work we do in the spaceflight sector.
Q: Can you tell us a little about your collaboration with your aerospace customers?
A: Kistler has a global presence, and our teams work closely with our customers to assist them with specific products or applications. We engage with our customers to offer them technical advice at the earliest possible stage of a program – that helps us to understand what they really want to test so we can guide them to select the right product.
Kistler’s product portfolio covers many applications, but there are always situations that call for solutions tailored to customers’ specific needs. This is where Kistler’s Custom Product Lane (or CPL) steps in to provide a fast-track customization service. Through our Tech Centers spread across Europe, Asia and North America, we offer system solutions that may combine equipment from Kistler and other manufacturers to meet overall test requirements. The Tech Centers also offer a wide range of calibration services including ISO 17025 accreditation with fast turnaround to meet time-critical testing schedules.
Q: Has your company seen an upturn in drone and VTOL aircraft testing?
A: Yes. Drones – or unmanned aerial vehicles (UAVs) – represent an emerging global market that is expected to grow significantly in the next decades. People are familiar with the use of these vehicles for military purposes, but there is also a growing number of commercial applications for many purposes ranging from delivery drones to eVTOL air taxis.
Q: What are the new challenges facing drone and VTOL testing?
A: Drones or UAVs are smaller than conventional aircraft, so the size and weight of sensors and instrumentation must be reduced to prevent any influence on flight testing. This is reflected in growing demand for smaller and lighter sensors.
It’s important to have a clear understanding of mission requirements and operational envelopes when selecting sensors and instrumentation. Test plans don’t have infinite budgets, so “good enough” can all too often be taken as a selection criterion to keep costs under control.
Kistler’s application engineers tackle these issues head-on by providing technical advisory support and identifying options for test engineers to consider. Testing in this sector can also face challenges related to human-in the-loop operation: one example of this is navigation/attitude control as opposed to fully autonomous operation.
Q: What are the benefits of using Kistler products for drone and VTOL testing?
A: First and foremost, customers benefit from our application know-how, which can guide them in their selection of sensors or instrumentation. We can also provide samples of sensors and instrumentation to support proof-of-concept demos and confirm the choice of a particular option.
One of Kistler’s key strengths is our PiezoStar piezoelectric crystal, used in IEPE accelerometers and for other measurands as well. This technology ensures ultra-stable sensitivity at temperatures experienced by test objects at various altitudes and in diverse operational environments. Then there is our K-Beam MEMS capacitive accelerometer technology, which supports flight testing by providing a static / dynamic response with high linearity, low noise and thermal stability. Accelerometers and the other products already mentioned are specifically designed and tested for the intended use and the specific handling, operational and environmental conditions.
Q: Are you introducing any technical improvements or products for this specific segment?
A: Yes! We’re constantly improving our portfolio to meet market requirements. One example is the new version of our popular triaxial IEPE accelerometer, with noise performance reduced by a factor of four. Then there’s our latest single-component PE force sensor, which is ten times more sensitive than its predecessor. And finally, we’ll soon be launching a miniature 6 mm cube triaxial accelerometer featuring our PiezoStar technology – with a mass of less than one gram. This will give engineers the advantages of flexible installation combined with reduced size and mass as well as the accuracy of triaxial technology. The first prototypes are already available.
Q: In your view, which trends in the aviation sector are having an impact on testing? And how is Kistler developing its products in response?
A: It’s important to listen to our customers and steer our R&D in the right direction to meet their needs. These are exciting times for the aerospace industry. The commercialization of space thanks to concepts such as second-stage combustion and reusable rockets is just one area where we are working with OEMs, suppliers and emerging companies.
Another example: electric aircraft and eVTOL, where green technology is evolving at a rapid pace. We must be able to meet the challenges of electrically driven propellers with higher rpms, and we have to adapt to the new certification environment for drones and electrification.
There is also definite demand for higher capacity: smaller batteries with lower mass are needed to ensure drone / VTOL aircraft operation over longer periods. The automotive and cell phone industries are driving the optimization of battery technology ahead, and these advances can be leveraged to benefit drones and VTOL aircraft.
Especially in eVTOLs, pancake motors are now being used to drive tilt propellers while larger motors provide forward thrust propulsion – but for these applications too, vibration characterization will still be required with rotary torque sensors and DAQ.
Flight, maneuvering and operational mission requirements are key factors in pushing the limits of sensor and signal conditioning technology. We look forward to developing new products and upgrading our current range in response to emerging performance criteria for measurements throughout this sector.