The Munich, Germany-based company 328 Services changed its name to Deutsche Aircraft in October last year.
The renaming was a significant milestone in its transition from a company that maintains Dornier 328 (D328) aircraft to one which is making a new eco-friendly version of the D328. That aircraft is planned to enter into service in 2024.At the same time Deutsche Aircraft is developing a hydrogen-fuel version of the D328eco. That aircraft’s first flight is also planned for 2025.
Martin Nüsseler joined the company from Airbus in February to help drive these development and certification programs. Aerospace Testing International talked to him about improving the D328, the prospects for more environmentally-sustainable aircraft and transitioning from a support company to an OEM.
Q: WHY DID YOU JOIN DEUTSCHE AIRCRAFT?
For two reasons – for the last six years I was leading a group-wide initiative to develop new propulsion systems at Airbus. Part of that was looking at what the right platforms are to explore these new technologies. It was very clear to me that regional aircraft are the right introduction for new technologies in the CS 25 class.
The opportunity to apply these lessons in a much smaller, leaner organization better suited to implement disruptive technologies was very attractive. Also, it was a good opportunity to lead the complete
CS 25 / Part 21 design organization, be responsible for a program while the company beceoms to a production OEM and work on the R&T for a future aircraft program.
Q: WHY CHOOSE THE D328 TO IMPROVE?
The regional aircraft market is driven by running older aircraft. The challenge of reducing the impact of climate change will affect it a lot and there is a lot of work on other mobility concepts that will compete with them. The regional market is therefore in need of new aviation concepts and technologies. Regional aircraft are also a good size of aircraft in which to implement new efficiency-improving technologies. It’s much harder to do that on larger aircraft.
A modernized turboprop version of the D328 compared to the jet version burns 16-20% less fuel for the same missions and payload. Combined with stretching the fuselage for 10 more passengers and adding the capability to use 100% sustainable aviation fuel, the 328 represents the best way to update the market with a green aircraft in the shortest time possible.
Q: WHAT IS THE OPPORTUNITY FOR A MORE SUSTAINABLE AIRCRAFT?
The management team here is convinced that the 5,000 regional aircraft – props and jets around 50 seats – in the air today will not be replaced with old technology. In the future there will be more environmental-related taxes. The regional market wants a more sustainable solution and will be the first part of the aviation market to see it.
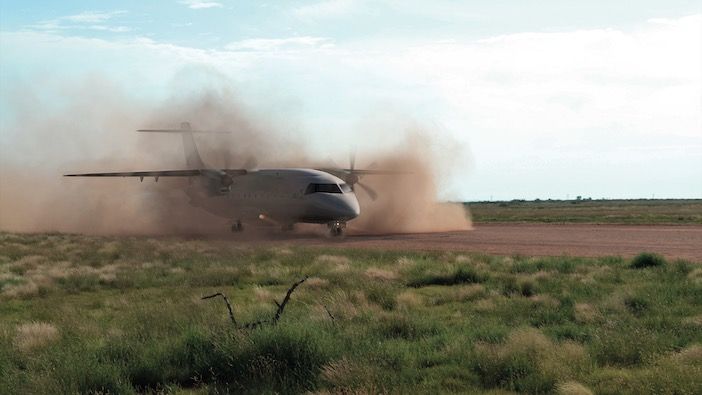
Q: IS THE D328eco PROGRAM LIKE AN AIRBUS NEO PROGRAM?
In one way it is because we are changing the propulsion system and making it SAF-compatible. But we are also adding the stretch to reduce the cost per seat down, integrating new avionics, a new cabin, and new landing gear. There are more system improvements then with a NEO. It’s more like a NEO+ program.
Q: WHAT IS THE STATUS OF THE D320ECO’s DEVELOPMENT PROGRAM?
In January we passed the main system requirements milestones, which defines the baseline design of the aircraft and its systems. We have selected the key main components, airframe and systems suppliers. This is the second part of the concept phase towards PDR (preliminary design review), which will happen during Spring 2022. PDR is the end of the concept phase and is when the aircraft’s systems are specified.
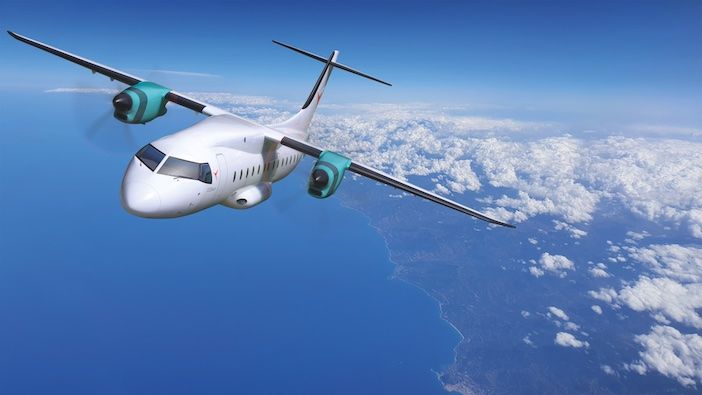
next step for many regional operators
Q: WHAT ARE THE ADVANTAGES OF UPGRADING VERSUS A CLEAN SHEET DESIGN?
The focus needs to be on your market objectives, and our aim is to bring to market as quickly as possible a regional aircraft that is more efficient and produces less emissions than what is currently available.
There is nothing wrong the D328’s airframe and its aerodynamic performance. Its validated performance is still the benchmark when it is compared with other regional aircraft.
So, taking that aircraft configuration to its limit with the stretch and adding a modern propulsion system is a winning combination compared to a clean sheet design, because we don’t have to do all the static fatigue testing. We can reduce the lead time to market.
On the other hand, many of its systems are obsolete. We have to upgrade the avionics and the electrical system. This integration presents a real challenge.
Q: WHAT IS THE MOST IMPORTANT AND MOST DIFFICULT IMPROVEMENT TO MAKE?
We are being very ambitious with our aim of single-pilot operation. Our flight deck is already compatible for single-pilot operation with functionalities such as emergency autolanding. But integrating the new avionics throughout the architecture of the aircraft is posing a real challenge.
The most complex part of integration is connecting the flight control system, which is partly mechanical and partly electric, with the new avionics to enable single pilot operations.
This is also a key reason we have decided to use an integrated iron bird test rig, because we cannot rely only on component-level bench and flight testing to meet this challenge. It is much better to test the entire integrated system on the ground before it goes into the aircraft for flight testing.
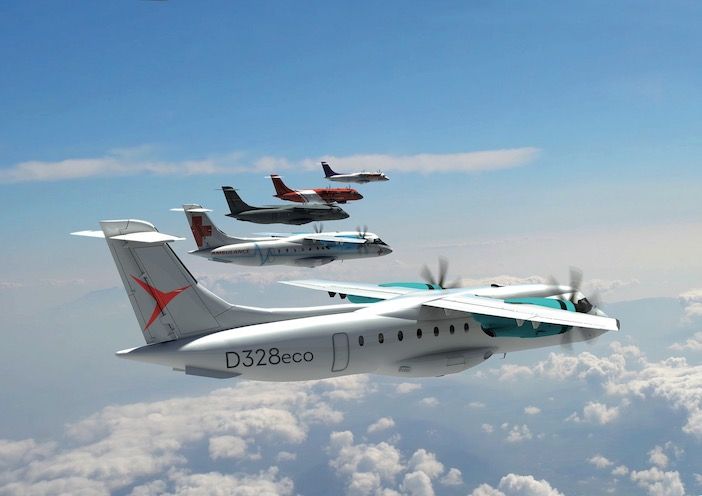
Q: WHAT EXPERTISE DOES THE COMPANY HAVE TO BECOME A MANUFACTURER AGAIN?
328 Services provided in-service support for the D328 fleet for fifteen years, so we have an engineering team that understands the legacy aircraft inside-out. There is also a design organization already in place that needs to grow but provides a great starting point.
We need to add more capability for flight physics, loads and sizing new systems and the industrialization aspects of design. One of our key challenges is converting the 2D drawings in the aircraft’s definition dossier to 3D CAD drawings, so we can have a paperless industrialization process.
Q: ARE YOU RECRUITING A LOT?
This year alone I have recruited 60 people and I need to recruit another 100 by the middle of next year for the D328eco and our R&T demonstrator program. We need people familiar with new technologies, loads, stress, fatigue, flight physics, handling quality, as well as product safety.
I’ve recently recruited a great director for flight and integration test and we now need to ramp up the complete test department. We want a good mix of new and experienced people. Young people can advance very fast in a company like this, working closely with more experienced people to widen their scope and understanding of the whole aircraft. The team is growing in a diverse way, with people who can understand the complexity of aircraft integration.
I’d like to take this opportunity to invite people to join us and work towards developing a more sustainable type of aviation. The team is growing fast.
Q: CAN YOU TELL ME ABOUT THE R&T PROJECT?
I want to be clear – our R&T project isn’t about electrification. Our objective is to produce an aircraft that impacts the environment less. We do that with two steps, first by achieving more efficiency and then by tackling emissions.
We are looking one step ahead so we can industrialize quickly and bring an aircraft to market as soon as possible.
The 328 in a hybrid configuration with a prop gives a good opportunity to think about the next steps for propulsion and energy systems. The platform is compatible with the many different architectures that might appear.
There are options with hydrogen. It could be applied through fuel cells to electrify the propulsion system, either as hybrid or full-electric. It could also be used in the engine for combustion. The key technical challenge for both is the hydrogen’s storage and distribution system.
We have launched with several partner companies a demonstrator program to move hydrogen propulsion forward. The demonstrator will have the full chain of a hydrogen tank, fuel cell system and a hybrid engine, to power the aircraft with electricity generated by a fuel cell during flight.
We plan to fly the demonstrator in 2025. We have already started on the hybrid engine design – we are reviewing the design of how the engine will integrate into the nacelle now. We are just starting on the fuel cell system, and we are working on the hydrogen storage system with our partners Universal Hydrogen.
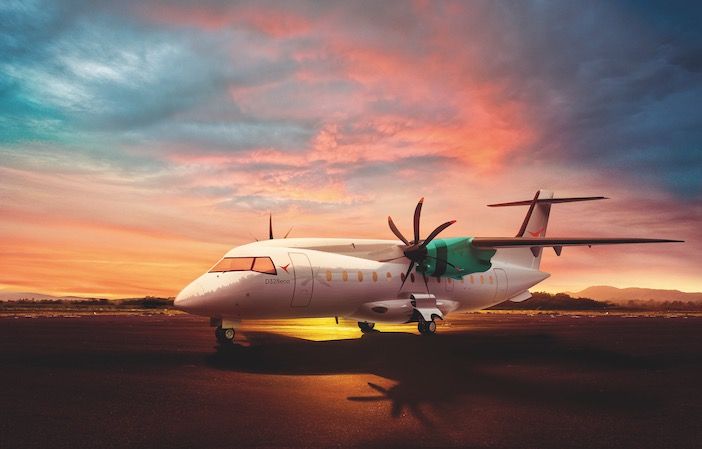
Q: WHY DO YOU FAVOUR HYDROGEN OVER BATTERY-ELECTRIC FOR FUTURE AIRCRAFT?
Looking ahead for the next ten years, battery technology just will not offer a solution for aircraft. You simply eat up all the payload with batteries, it’s an easy calculation. Overall aircraft efficiency needs to be judged by payload per kg in an aircraft, not just by the emissions produced.
If you are using three times the energy to transport 1kg, it’s not climate friendly. Yes, it may be
zero-emissions at the point of use, but consider the production of the batteries, the after-market impact and the efficiency. At the moment, for an aircraft larger than four seats batteries aren’t ready, even as a complementary energy source.
Nobody has been able to demonstrate on a real-world scale a propulsion system where the impact of the weight of the batteries is low enough to not impact on the commercial viability of the aircraft. So it was a simple decision to make.
Q: WHAT IS YOUR DAY-TO-DAY WORK LIKE?
I’m very busy because the topics I am managing are very wide. I spend a lot of time on recruiting for the team. Everyday I communicate with people on topics we decide together, it’s an inspiring environment. The company is a good mix of a startup and an established company. It means we already have aircraft in the hangar flying.
We have a lot of tasks ahead, but it’s a team challenge, and if the team is good we can achieve our aims and be satisfied with our job. The right team must have the right balance of experience from older engineers and ambition from new recruits. But the essential thing is that we are all passionate about what we do
CV: Martin Nüsseler, CTO of Deutsche Aircraft
Nüsseler is responsible for Deutsche Aircraft’s product strategy and technology road map. He is also has oversight of the company’s engineering development team.
He joined the company after working for Airbus for 17 years. The last five of those years were spent leading the Airbus alternative propulsion systems and technologies unit. He worked on the A350XWB as head of engineering the fuselage at the Airbus subsidiary Premium-Aerotec and as the A350XWB’s head of airframe architecture. Before that he was head of A400M fuselage engineering at Airbus
Nüsseler also worked for the aircraft company Fairchild Dornier in the late 1990s.
Related Stories
328 Services renames to Deutsche Aircraft for aircraft development