Words by Ben Sampson
If you looked up during April in Deelen, the Netherlands you might have spotted a single-aisle passenger aircraft that looked like an A320. Not the most noteworthy of occurrences admittedly. After all it is the world’s most popular short-haul aircraft. But a closer look would have revealed something unusual.
This aircraft flying above Deelen Airbase was in fact an almost perfectly miniaturized replica of an A320 on a 1:8.5 scale. Instead of a wingspan of 34m (112ft) this aircraft measures just 4m (13ft) across – instead of 40,000kg (88,000 lbs) it weighs just 140kg (310 lbs).
The aircraft, the Scaled Flight Demonstrator (SFD), was loaded with sensors and instruments designed to monitor, track and record 150 parameters of its movement and status during flight. The SFD has taken six years to develop and is insured for €2 million (US$2.1 million). It is the first version of a test aircraft designed and built by engineers from several European aerospace research institutes and companies as part of a six year project organized by ONERA under the EU’s Clean Sky 2 program.
The first version of the SFD aims to accurately determine the extent to which flight test data from a scaled model can be used to de-risk and reduce the development costs of the next generation of more sustainable aircraft. The second version, which is currently under development will be used to flight test one of the most advanced aviation concepts – Distributed Electric Propulsion (DEP), next year.
Flight test measurements
Building and flying scaled prototypes is not a new idea. According to industry research there has been an increase in the use of scaled prototypes in the last 15 to 20 years, mainly thanks to the miniaturization of instrumentation and aircraft components, as well as advances in manufacturing methods.
Crucially, the SFD is more test aircraft than it is model. Its flight test instrumentation (FTI) measures over 150 parameters – inertial data, pressure, air speed, temperature and control surfaces, the engine and exhaust gas temperature. The focus is on measuring aircraft dynamics and controls.
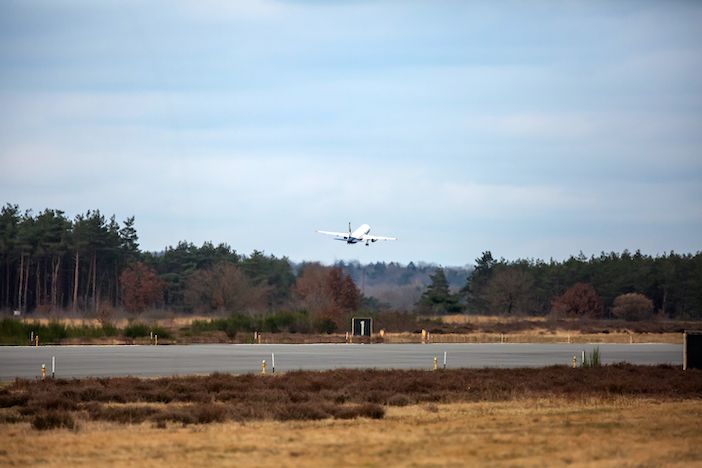
Fitting in the FTI and meeting weight targets was a challenge. Henk Jentink, senior scientist at the Royal Netherlands Aerospace Centre (NLR) is responsible for the FTI. He says, “We researched what is best to use in the aircraft and did not have to make too many compromises. Small enough equipment is readily available on the market nowadays.
“We wanted the scaled aircraft to be as large as possible. The larger it is, the more accurate and similar the data is to the full-size aircraft. On the other hand, the smaller it is, the easier it is to handle and the cheaper it is. The size was considered a lot.”
Leo Timmermans, NLR’s project manager for the SFD says, “We did not want to go above 150kg (330 lbs) because of the regulations around flying drones. It has been scaled for a specific purpose, examining aircraft behavior after take-off and on descent at Mach 0.4.
“Many people believed it should be a bit larger – such as 1:8, because the smaller you get the more difficult it gets to fit all the cabling and instrumentation inside. But importantly at this size it can fit in the wind tunnel.”
Similarities
Reusing the model from wind tunnel testing for initial flight testing will reduce costs. Timmermans says, “The normal development process is to start with calculations, then move into the wind tunnel with a prototype. But you cannot test everything in the wind tunnel, things like flight dynamics and controls.
“So, the next step in a program should be to test those things using the same scaled prototype, which reduces the risk and cost compared to using a full-scale prototype.
“The purpose of the current SFD is to validate scaled flight testing. People already believe in the concept, but we want to know to what level we can take
the similarity.”
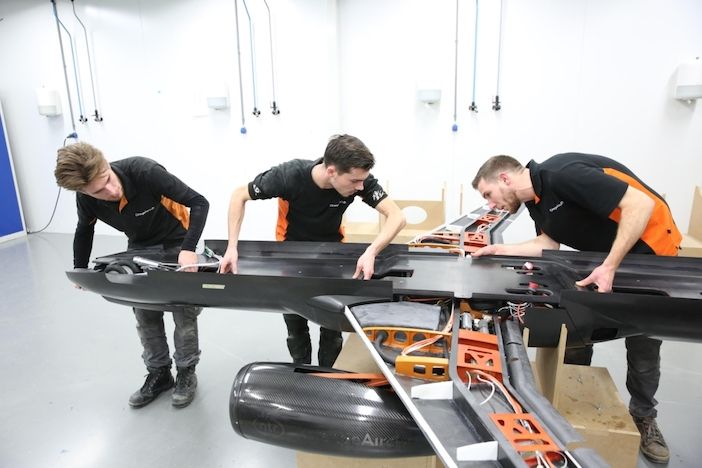
The researchers have copied an existing aircraft about which there is a lot of known data and will compare flight data from that scaled version to the known data from the full-size version. The refined transpositions laws between the scales are investigated by ONERA using CFD computations. “The data will also be used as a baseline for new developments, such as distributed electric propulsion,” says Timmermans.
The replication extends to the control surfaces. The flight controls, rudder, ailerons and elevators are scaled to the reference aircraft. The shape is not 100% identical to an A320, but good enough to calculate a delta for the validation process. Jentink says, “In addition, the wing is not identical. We have to fly the SFD at lower speeds, not the transonic speeds a single-aisle passenger aircraft achieves, so it has to be different.”
The aircraft is made from carbon-fiber-reinforced polymer not aluminum. The engines used are commercial-off-the-shelf small low-bypass turbojets, fueled by kerosene, which are produced by Netherlands-based company AMT. The SFD is capable of a cruise speed of 160km/h (100mph).
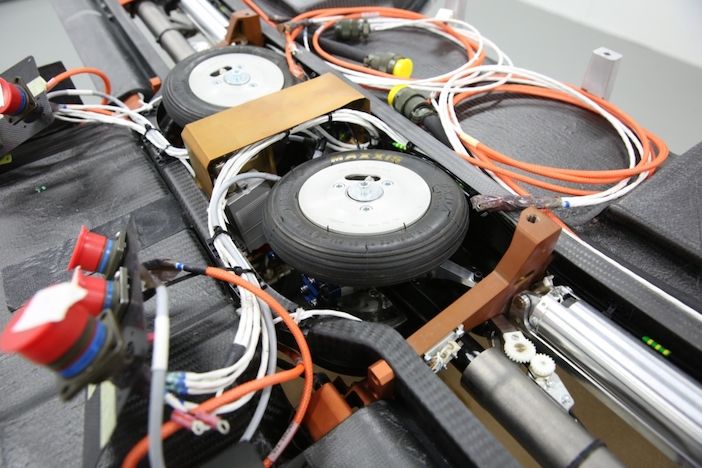
Controls and Instrumentation
During development another key decision was the position of the camera, which was shifted from the nose to the tail. This has resulted in a slightly different nose shape. The project will assess the extent to which the lower speed capabilities affect the data.
Timmermans says, “During the project we have learnt that the SFD is truly a test aircraft – not a model. We can measure almost everything.
“As well as the instrumentation on board there is the autopilot [MicroPilot] for the control that records a lot of data. The dedicated guidance navigation control computer will record even more data.”
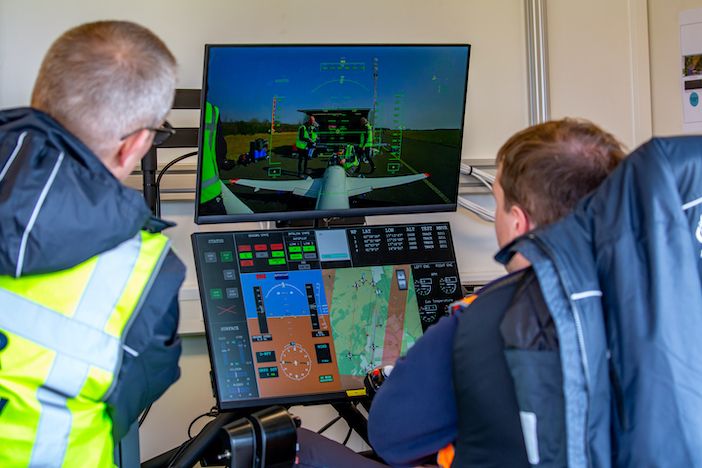
A trailer houses the ground control station, the pilot’s station and the telemetry equipment. During the mission flight maneuvers performed by the aircraft are commanded by a guidance navigation and control (GNC) system developed by the Italian Aerospace Research Centre – CIRA. The GNC was designed to execute accurate and repeatable tests and enable a reliable measurement of the aircraft’s dynamic performance.
The pilot station is closed during flight. “The pilot experiences the control of the aircraft like they are doing a simulation, with a head-up display and live camera,” says Timmermans. “There is crew as there would be in a full-size aircraft, just on the ground.”
Also present during the SFD’s flights is a co-pilot, an engineer focused on the ground control systems and an FTI engineer. Data is primarily recorded on board the aircraft and stored locally during a flight, although essential parameters are also telemetered to the ground station. The maximum flight time of the SFD is 30 minutes. This is restricted by the size of the fuel tank and the weight of the fuel.
Next Steps
Version two of the SFD will test DEP during a series of test flights. The wings and fuselage of the SFD were designed to detach for ease of transport and the initial concept was to replace the wing with one that features the propellers for DEP arrangements. But delays in the SFD’s development caused by the pandemic forced the researchers to make a second fuselage and just the avionics and FTI will be transferred.
The DEP wing will use battery electric power instead of combustion and six propellers instead of the mini-jet engines. Researchers are aiming to increase knowledge about how to control DEP and how it reacts under different thrust possibilities.
Jentink says, “The main aim is to find out how we can de-risk this kind of DEP configuration. It is potentially much more energy efficient.”
“We also want to know what new things we can do with controls. Having differential thrust on either wing means you can distribute power between propellers to improve efficiency and new control possibilities.
“With the right rotation on a wingtip propeller you can prevent loss of energy. With six propellers you have a lot of airflow being accelerated a little compared with less air being accelerated when using jets, which could increase efficiency. Its these kinds of aspects of flight handling and efficiency that we want to measure.
“Scaled flight testing is the way that many new radically different aircraft designs could be developed,” adds Timmermans.
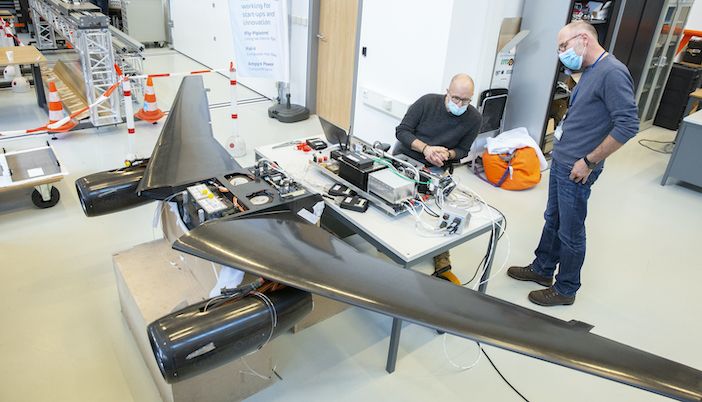
The SFD work is being done in parallel to research being conducted by NASA with its X-57 program. NASA researchers have already done scaled flight testing to research DEP and are now preparing a full-scale X-57 for its first flight. “They have done more scaled flight testing than in Europe, which is another reason to kickstart the use of SFD in Europe,” says Jentink.
The hope is that aircraft OEMs will use SFD more in the future and with more confidence. Airbus is a lead partner in the project. “The SFD approach will not be useful for developing variants, but for unconventional aircraft design it is much more interesting. We believe it is a very valuable tool for developing the next generation of more sustainable aircraft,” says Timmermans.
Controlling electric aircraft
Electrically-driven aircraft require physical actuators to move control surfaces such as the rudder, elevator and high-lift systems, as well as systems such as landing gear and braking. Curtiss-Wright develops and supplies actuators for commercial and military aircraft.
A major trend for several years has been a move away from the use of hydraulics in aircraft actuator systems towards electromechanical actuation. This looks set to continue with electric and eVTOL aircraft. Ollie Green, business development director for Curtiss-Wright’s actuation division says, “Electromechanical actuators give better energy efficiency, better fuel burn and better reliability. The trend is well established on the commercial side and the military is also adopting the same technology. New types of aircraft will hardly use hydraulics or pneumatics.”
Curtiss-Wright is involved with several electric and eVTOL aircraft developers, many of which are using some kind of distributed electric propulsion. These include Washington, USA-based Eviation. The company has supplied the primary flight control actuators for the startup’s first aircraft Alice, which is currently going through taxi testing.
The development of flight control actuation systems for eVTOL and electric aircraft differs considerably from conventional aircraft. Green says, “Flight controls are being developed in innovative and varied ways for these vehicles for two main reasons.
“These new aircraft have very different characteristics, they look and maneuver differently. When you have ten propellers on the leading edge of the wing, they can play a significant role in the maneuvering of
the aircraft.
“Also, there is a blurring of the boundaries between the propulsion system and the flight controls.”
Modern conventional aircraft use FADEC to control the engines and have a separate flight control system, with its own computers and actuators handles the moving surfaces. Advanced flight control systems control both propulsion and moving surfaces.
“We are increasingly seeing companies use a single computing platform to control both the propulsion and flight control surfaces simultaneously,” says Green. “It can make the control of the aircraft more efficient, elegant and reduce the aircraft’s overall weight.
“For example, some of these vehicles control thrust through varying the speed of the propulsion motors. Others use a pitch change mechanism in the propellers in the same way a turboprop would.”