Since the official launch of the A321XLR at 2019’s Paris Air Show, there has been more than 420 orders and commitments from over 20 customers, including legacy and low-cost carriers as well as leading lessors for the extra-long-range version of the A320neo family’s longest fuselage aircraft.
Such demand clearly underlines its appeal as a bridge between Airbus’ single- and twin-aisle aircraft offerings. Its extra reach and 30% lower fuel burn per seat than previous-generation aircraft will enable airlines to operate a lower-cost, single-aisle aircraft up to 4,700nm on longer and less heavily travelled routes – many of which can now only be served by larger and less efficient wide-body aircraft.
Despite being designed to maximize overall commonality with the A321LR and the rest of the A320neo family, incorporating the same kerosene-saving P&W- or CFM-supplied engines and sharklet wing-tip devices, the A321XLR boasts several unique, distinguishing features.
“The main differences are the rear center tank integrated in the aft fuselage, the larger waste water tank, a reinforced nose landing gear and main landing gear, including brakes, allowing for an increased MTOW from 97t up to 101t,” says Gary O’Donnell, head of the A321XLR program.
In particular, the optimized rear center tank (RCT) holds more fuel than several optional additional center tanks did previously, while taking up less space in the cargo hold – thus freeing-up under floor volume for additional cargo and baggage on long range routes.
Meanwhile, aerodynamic improvements include a new single-slotted flap and enhancements on the aerodynamic cleanliness of the surfaces of the aircraft, as well as new flap / slat configurations adapted to the characteristics of the A321XLR.
To provide extra comfort on longer flights, the A321XLR will use Airbus’ latest Airspace cabin, which features enhanced mood lighting, onboard connectivity and larger bins offering 40% more capacity installed as supplier-fitted equipment.
“The cabin provides passengers with the best travel experience, including seats similar to those used on a wide-body aircraft,” says O’Donnell. “Airspace is already in service on A350 and A330neo aircraft and will be fully available for A321XLR.”
Major component assembly
Industrialization and parts production for the first A321XLR is underway across Airbus sites and its supply chain, with major component assembly of the first forward fuselage, center and rear fuselage sections and the wings expected to occur before the end of this year. Airbus is targeting an entry into service for the A321XLR of 2023, although this may be delayed depending on how fuel tank testing and certification proceeds.
“The production of components and systems for the first A321XLR flight-test aircraft is progressing at sites across the world,” says O’Donnell. “In parallel many parts are already being tested and demonstrated – on both the aircraft structure and on the systems side – to validate the functionality of all those first aircraft components.”
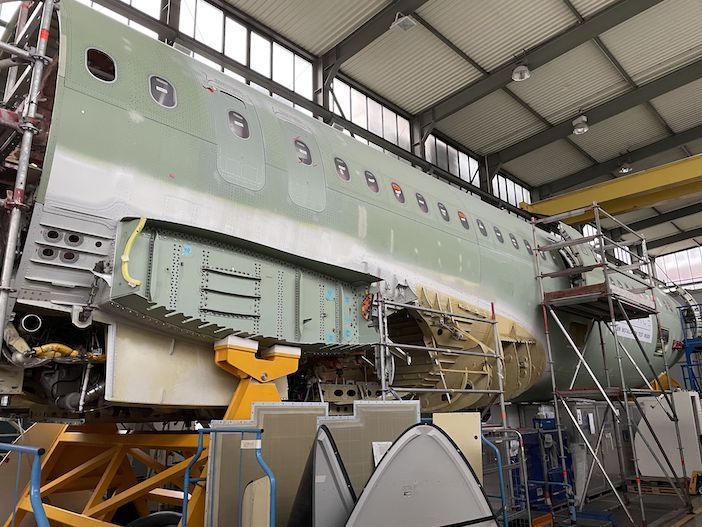
Airbus has demonstrators for structure, system, equipment and the cabin spread across its facilities in Hamburg in Germany, St. Nazaire in France and Broughton, UK as well as at key supplier sites. “These range from detailed material coupons to full section demonstrators,” says O’Donnell.
“The production system in particular is coming alive, with our teams receiving the design drawings both internally and from key partners and bringing them into physical reality.
“This is enabling our factories across Europe and the UK to prepare their pilot operations for the major component assembly phase to begin later this year, and in turn, for the subsequent induction of the first completed major component assembly into the final assembly line at Hamburg in the second part of the year.”
Line of attack
While all major sections of the A321XLR contain significant design changes versus the current A321neo / A321LR aircraft, the XLR’s centre and aft fuselage deviate the furthest because of the integral RCT and associated fuel management systems. In a bid to avoid any disruption to the existing single-aisle production rates, a separate structure pilot line dedicated to assembling the A321XLR’s centre and rear fuselage sections has been built at the Hamburg Finkenwerder production facility in Germany.
The pilot line has been fully designed in 3D, with A321XLR-design data used to digitally validate ergonomics, operations and logistics beforehand.
“The pilot line in Hamburg means that we can have a stable factory,” explains O’Donnell. “It will allow us to start ramping-up production of the A321XLR’s aft fuselage major component assembly using longer cycle times to begin with and with an increased level of engineering and support – to ensure the smooth integration of the new rear center tank and its new fuel systems.
“Importantly, it will also avoid us putting at risk the rest of single-aisle production. And then, once we’re happy that everything is mature enough, we can transfer it with confidence into the main production system.”
Multi-site approach
Meanwhile, the A321XLR’s centre and aft fuselage’s production cycle continues to progress, with work split across several key sites. Manufacturing of the subassembly of the center wing box started in mid-November 2020 in Nantes and will soon be delivered and integrated into the aft fuselage major component assembly section at Hamburg.
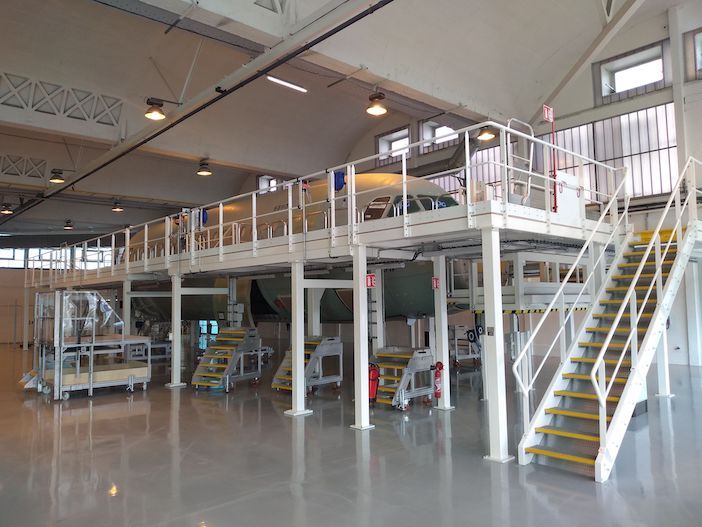
At the same time, Premium Aerotec Group in Augsburg, Germany is completing the final parts for the RCT and is readying the tooling and shop floor for the fuel tank’s assembly. At Premium Aerotec Group’s other sites in Nordenham and Varel in Germany, various large centre and aft fuselage components are also beginning to be produced.
Parts production for the aircraft’s nose and forward fuselage section is underway at Stelia Aerospace. Once completed, they will be transported to Saint-Nazaire, France for the nose and forward fuselage major component assembly stage.
Another key major component assembly structure is the aircraft wing set, for which the Broughton, UK team’s particular focus is the A321XLR’s flap configuration. To this end, the associated tooling trials are in progress for the new inboard and outboard flaps, which are being performed in conjunction with Spirit AeroSystems in Malaysia and FACC in Austria respectively.
The wing’s more conventional fixed components, such as spars and stringers, are taking shape in Broughton and in the associated supply chain. Likewise, production is underway for the landing gear components at Safran, Collins and Triumph, fuel and inerting systems at Collins and Parker Aerospace and the engine pylons at Airbus’ dedicated production plant in St. Eloi, Toulouse. Cabin and cargo systems are currently in the testing phase to validate the A321XLR’s extra-long-range passenger comfort elements.
Demonstrators play key role
Airbus is using dedicated demonstrators to validate the design and assembly processes ahead of final manufacturing. The same full-size demonstrators are also used to pre-train the production-line staff at the final assembly facility in Hamburg, where the first A321XLR will be built.
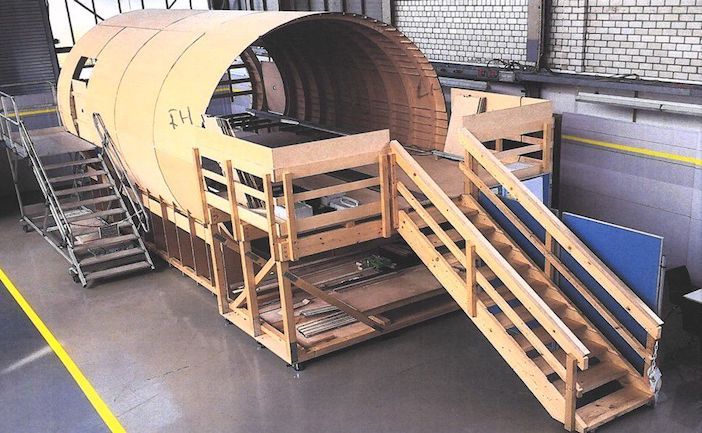
“We have been using a mixture of virtual and augmented reality [VR and AR]to demonstrate the 3D digital model for some time already,” says O’Donnell. “We have also been using early physical demonstrators, wooden mock-ups and 3D printed parts.
“More recently, we have developed the full-scale production demonstrators which we see more and more of today – primarily at Saint Nazaire and Hamburg,” he says. “The early physical demonstrators and the virtual demonstrators enable us to validate our design decisions. Most of that was completed in 2020.
“The production demonstrators primarily support the training, the industrial process maturity and help to secure our ramp up, because we run them at production rate. This is happening across the assembly areas.
“Then we are running demonstrators for maintenance, repair and customer support teams, so they can create the airline documents, other technical documents and repair manuals.
“We use physical demonstrators with VR and AR so the teams can test how they change and fix parts – whether in a hangar or on the apron, so that when they are writing technical documents, they have already been able to check on these virtual references.”
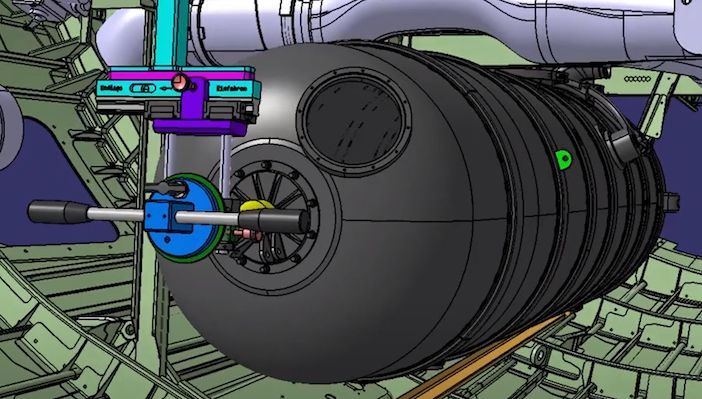
Ratings war
Such attention to detail is designed to ensure Airbus can maintain its aggressive delivery targets for an aircraft that continues to win orders. “Currently, we are at rate 40 for the overall A320 family with a plan to ramp up to 45 by the end f this year,” reveals O’Donnell.
The two large fuselage structures and systems demonstrators located in Hamburg, Germany and in Saint Nazaire, France, are the current focus. Respectively, these physical mock-ups (PMUs) are the Pre-Industrial System Accelerator (PISA) for the centre and aft fuselage (CAF) section, and the nose and forward fuselage (NFF) section.
“In the PMU demonstrator for the forward section we are focused on the XLR’s structure reinforcement due to the different loads, and also on the new systems improvement for cabin comfort,” says Martin Schnoor, the A321XLR airframe leader at Airbus. “The PMU gives us the opportunity to bring all of the modifications together from airframe, systems and cabin to confirm the industrial interfaces,” he continues.
“Meanwhile the PMU in Hamburg is focusing on the XLR’s major components including the rear-centre-tank integration, water tank integration, the extended fuel system and the modified hydraulic system. Here, we take full advantage of the proximity of the rear fuselage PMU to the final assembly line to provide production operator training before they go into the first serial produced aircraft.”
Airbus plans to keep and update the PMU demonstrators over the life of the XLR program, to perfect future modifications as well for shop-floor training purposes.

“All of these demonstrators help us to observe the systems, activities and workflows under holistic real conditions at an early stage before the start of production,” says Hauke Delmas, head of single aisle XLR equipping at Airbus’ Hamburg Finkenwerder facility.
“The demonstrators, along with classroom training and VR / AR training, will be an integral part of our employee training and onboarding in the future,” says Delmas. “They provide a protected space for learning and further development and make it possible to learn from mistakes, without endangering production or safety.”
Structural assembly
At the end of June, production of the A321XLR had started on the dedicated structure pilot line inside Hangar 260 at Airbus’ Hamburg plant, responsible for the structural assembly of the centre and rear fuselages.
In parallel to this, the structural assembly of section 15 had started in mid-April with the integration of the shells from RUAG, as well as the centre wing box from Airbus Nantes, and the keel beam and rear flange module supplied by Premium Aerotec.
In the coming weeks, the teams will finalize the integration of the RCT module into section 17, with the structural assembly of the second flight test aircraft. The equipment assembly phase of the first aircraft is planned in the fall, followed by a dedicated period for flight test equipment installation
Fuel for thought
Premium Aerotec in Augsburg, Germany is responsible for the production of the A321XLR’s rear center tank (RCT) – a permanently installed high-capacity fuel tank that makes maximum volumetric use of the aircraft’s lower fuselage. The RCT structure, which is integrated in fuselage sections 15 and 17 is located behind the main landing gear bay and holds up to 13,100 liters of fuel.
However, Boeing recently raised concerns with EASA that integrating the new fuel tank into the fuselage “presents many potential hazards”, suggesting that such a design provides less redundancy than structurally separate fuel tanks and offers less protection against structural disruption due to an otherwise survivable off-runway or landing gear failure event.
To ensure safety, EASA has imposed special conditions to protect the lower half of the fuselage around the center fuel tank from fire penetration.
In May, Premium Aerotec delivered the first fully equipped RCT to Airbus’ Hamburg site, heralding the start of the assembly of the aircraft’s rear fuselage and the center fuselage on the plane maker’s dedicated pilot line.
“It’s a major milestone for the A321XLR program,” says Martin Schnoor, head of A321XLR program development airframe program at Airbus. “The teams can be proud of this achievement and the overall speed of industrialization.
“We are on track with our planning and the pilot line dedicated to the A321XLR is ready and waiting to operate the assembly phases for the first flight test aircraft, all the way through to the entry into service.”
Related Stories
Airbus launches even longer range A321
Behind the scenes at Airbus’ Airtec testing facility in Filton
Airbus releases flight testing video series