Any modern tech guru will readily tell you that data is the most valuable asset to a business in the 21st century. That may well be the case, but to an engineer like Rick Stiers, instrumentation solutions architect at Boeing, it’s old news. During his 40-year career in aerospace testing, data has always been a precious commodity.
Boeing Commercial Airplanes has never been busier. Engineers are currently working on the 777X. The 737 MAX 10 and potentially the NMA (New Mid-Market Airplane) are in the pipeline. These aircraft will cost many billions of dollars to develop. The cost puts tremendous pressure on the flight test programs for these aircraft, which will cost hundreds of millions of dollars through to certification.
At a recent event organized by aerospace equipment company Zodiac in Paris, the question “How can industry help the aerospace test community?” was posed. Speaking at the event, Stiers described how data – what it is being used for and by whom, and its costs – shape the specification, design and installation of the flight test instrumentation (FTI) used during the modern day flight testing of Boeing’s commercial airliners.
Customer satisfaction
The first step in defining the FTI is to define the testing requirements. This starts with identifying who will use the data and defining what they want. Stiers says, “When working out the testing requirements for FTI, there are lots of customers and consumers to consider. It’s a very complicated environment and some of the customers are completely disassociated from what we do.
“The aero-performance people care about steady-state pressure-altitude down to centimeters. The stability and control team operating in a dynamic environment with accuracies in the range of 5-10 meters. These are fundamentally two different requirements. How do you rationalize all of the data acquisition and the varying requirements for the same single parameter of pressure-altitude?”
A dozens-strong team collates the requirements for the data from the various groups, categorizes all the tests and produces a comprehensive plan. The flight test program starts with the safety tests, then the basic performance characteristics such as inflight restarts, and then moves on to the performance-related categories such as fuel consumption and roll-rate responses.
As part of planning, the FTI team validates the requirements, the system design and allocation, and accounts for any new product introduction issues and the costs associated with them. Preparations for a flight test program can start up to three years in advance. “Once we know the requirements we start making design decisions for the FTI and physically modifying a commercial jet. The certification organizations also have to be provided with documentation of all the changes,” says Stiers.
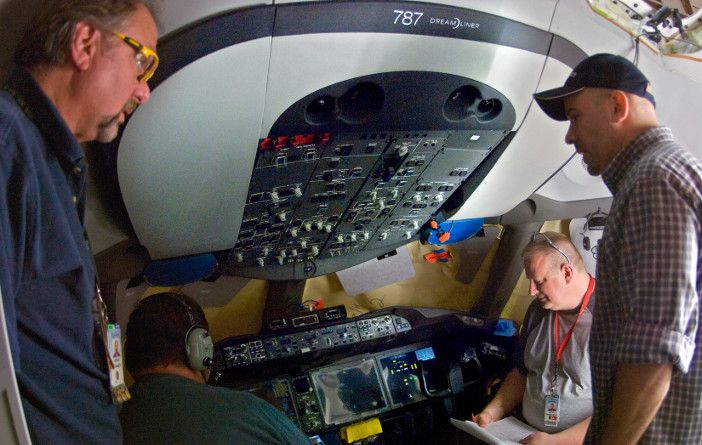
The FTI team will examine if it is possible to reuse existing flight test installations and aircraft for flight test programs at this stage to reduce costs. For example, when flight testing the next-generation 737, the team was able to reuse some existing testing installations. But some things, such as the instrumentation interface designs, had to be completely new. Similarly, another cost-associated decision made during the planning stage was whether to use custom new hardware and software, which is more expensive and has longer lead times, or to use COTS equipment and software.
“All our systems are used to take certification data for new production introductions, so they have to be calibrated and certified for accuracy,” says Stiers. “That means pushing calibration systems to the limit. In some cases the calibration systems are no better than the data acquisition systems themselves, which is a conundrum.”
Multipurpose data
A primary driver when designing FTI is what the data will be used for, such as flight manuals, certification, troubleshooting and computer models. The data is also often used to improve simulators for pilot training. “The data has to validate the structural design, performance and stability and control. Then we demonstrate the aircraft to the certification organization,” says Stiers.
“The data we produce is put into simulators to refine computer models for the next product. Terabytes of data are put into a big data warehouse. It’s used for computational fluid dynamics, the aero-models, the kinematic models, the structural loading, the wing bending and twisting, and dynamic flight models. These uses are perhaps the greatest value the data has.”
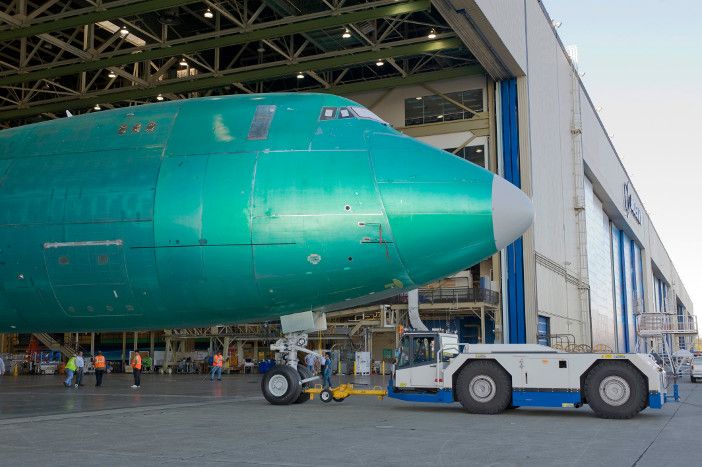
According to Stiers, the data from flight testing has a long life and is used decades later. Data recorded during flight tests of the Boeing 747-400 in 1990 were recently used to compare with the results from flight tests of the Boeing 747-8.
Reducing costs
The instrumentation has to cater for each different stakeholder’s requirements and the competition to meet these requirements can sometimes create cost pressures on budgets. Innovation within the FTI can provide a solution to mitigate high costs. Stiers explains, “For example, a consideration may be where to position the pressure/altitude sensor. If you just put flush-mounted ports on the skin, the data is okay for some users but not others.
“In particular, aero performance work requires a trailing device with a precision fidelity of 4cm [1.6in], it is a complex and expensive measurement.”
Another challenge for the FTI team is validation. It is essential that the team can validate that they are measuring the correct things, and not performing too many tests. “We test really big airplanes with up to 5,000 analogs and 250,000 digital parameters,” says Stiers. “But we also have to do quick-and-dirty tests with just 10 parameters.
“How can industry help? We need systems that are scalable in fidelity, bit rate and accuracy so we can pick the correct systems and hardware for particular test cases. There is a constant balance to be struck between cost versus value and cost versus affordability.”
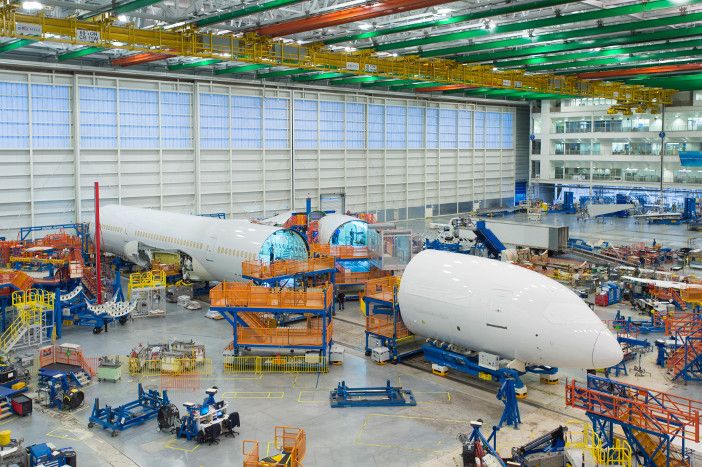
For a typical flight test program, Boeing will fly four to six jets for up to 12 months. The FTI configuration and the work required to install it is started up to a year before they are scheduled to fly. For a major test campaign FTI is installed in the factory in parallel with the production build.
“Depending on what instrumentation you are installing, you might have to go into the factory six to eight months early,” says Stiers.
Despite the numerous internal pressures on flight test programs, Stiers still welcomes competition from Airbus. “There is huge competition between cost, affordability and performance between Airbus and Boeing for commercial jets,” he says. “Without a good competitor you can become stale.”
The competition is having a direct effect on FTI in three areas, measurement system accuracy and fidelity is increasing at the same time affordability is becoming more of a concern. Performance margins on aircraft are tighter. Manufacturers also have to be able to make guarantees to customers on performance-related aspects of aircraft, such as mileage, passenger loading and speed of boarding.
“At the same time, every generation of aircraft incorporates new technology,” says Stiers.
“The 787 used graphite and had new engines. The 737 has very compact engines, which presented their own unique set of problems.
“And the whole time, everything has to be done better, faster and less expensively. We have to be more flexible, adaptable and we have to be able to create new versions of our test systems quickly and efficiently.”
Stiers believes that one of the best ways for FTI engineers to deal with new technology and the challenges it brings is to adapt a flexible approach to data acquisition. Boeing has been using Zodiac XMA data acquisition systems “in a lot of nasty places”. This includes in engines and wheel wells to measure temperature at an accuracy of 1,000 parts per million, across a temperature range of -40°C to +85°C (-40°F to 185°F).
An advantage of the XMA DAU (Data Acquisition Unit) is the firmware can be changed and adjusted to handle a variety of different parameters. The module’s personality is configurable through the firmware and can be reprogrammed through the setup process to measure a whole host of data types, from millivolt level strain gauges to thermocouples, all on the same hardware. “These capabilities enable us to do more things with the hardware, making us more agile,” says Stiers. “The firmware change capability provides a plethora of digital filters that can emulate other parameters.
“Flight test instrumentation requires flexible, adaptable solutions that are less hardware-intensive, with a wide variety of data acquisition and processing options that can be exercised after the hardware is done. It needs scalable solutions that can deal with 10 to 5,000 parameters.”
With lead times years in advance, demanding airline customers, internal stakeholders that require more data for more different purposes – as well as external competition – the pressures have never been greater on flight test programs. It would seem that remaining agile and affordable with the use of new and COTS technology is essential to meeting test requirements and dealing with competing pressures.
This article was originally published in the September 2018 print issue of Aerospace Testing International. To view more and subscribe go here.