Experts predict that by 2030 people will be able to book flights on hybrid-electric airplane. There is continuous progress on a variety of eAircraft (electric Aircraft) projects and several propulsion systems for flying demonstrators in the pipeline.
Siemens is involved in several eAircraft projects, including the E-Fan X partnership between Siemens, Airbus and Rolls-Royce, the CityAirbus demonstrator, and the Extra 330LE aircraft.
The further electrification of aircraft requires a lot of innovation to take place, but the developments are necessary so the future global aviation community can satisfy sustainability, environmental, noise and pollution issues. Despite the many challenges, the pace of eAircraft development is accelerating. Less than a decade ago in 2011, the world’s first hybrid-electric aircraft, the DA36 eStar, took its maiden flight. Inside this airplane was an integrated drive train from Siemens’ Drive Technologies Division in Erlangen, Germany.
Within just three years, a team of experts went from the electric concept stage to developing a working digital twin and flying two-seater, the Extra 330LE. Weighing approximately 1,000kg, the Extra 330LE serves as a demonstrator and testbed for Siemens’ new electric drive system. Since the Extra 330LE is an aerobatic airplane, it is suitable for taking the system to its limits to test and enhance the design.
Test flights in the Extra 330LE last about 20 minutes, including take-off, climbing and five minutes of full-performance flight. The airplane successfully completed its maiden flight on July 4, 2016 in Dinslaken, Germany. It was the first time an electric plane had been flown in the performance class of a quarter of a megawatt.
The electric motor in the Extra 330LE weighs just 50kg and supplies permanent electrical power of 260kW– five times the level of comparable drive systems. The underlying technology it uses has formed the basis for several of Siemens’ other e-flight partnerships, including the CityAirbus and the E-Fan X.
The beauty of electric drives is their scalability. Siemens expects to see the first hybrid-electric planes with 100 passengers and a range of about 1,000 kilometers by 2030.
Behind the scenes in Erlangen
The team responsible for the digital twin development of the Extra 330LE is based in Building 32 on the Siemens campus in Erlangen, Germany. Once you clear the security post, it is just a short walk down the street that you find the real hub of Siemens eAircraft activity.
Siemens’ Simcenter software played a big role in developing the Extra 330LE. Engineers created an accurate digital twin that let them design everything in the virtual world before building it in reality. From an engineering standpoint, Simcenter provided an all-encompassing solution.
“The setup is special because all the software is connected,” says Toni Amende, an engineer with the Siemens eAircraft team. “We come from Teamcenter, where the data is stored, and then we go to the NX CAD application, and from this application we jump into CAE, which, in this case, is the thermal simulation. From here, we can go bi-directionally into Simcenter STAR-CCM+. This gives us more CFD capabilities in terms of bigger models, simulating all systems, and a greater degree of accuracy in the details.”
Although today the team is focusing more on the details, when they started the process, Simcenter was a critical tool, especially when tackling the overall weight reduction required for the Siemens eAircraft. During the early development phase, the team used the topology optimization tool within Simcenter to investigate which type of structure would be optimal.
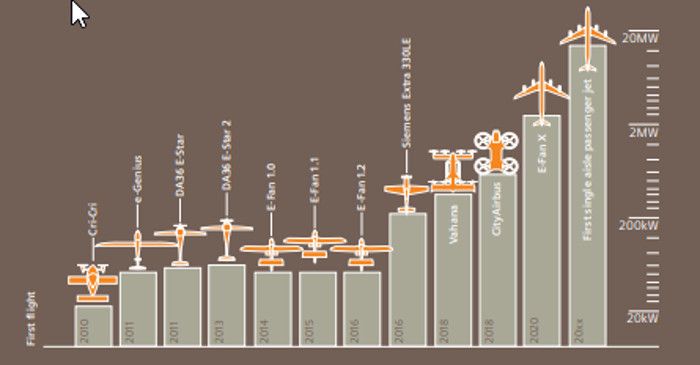
Dr. Gunar Reinicke, lead engineer of the Siemens eAircraft team, says, “We are always interested in having the lightest components to fulfill our needs. Simcenter gave us the right tools in order to develop, investigate and understand the product in detail and also deliver the product on time.”
Another area in which the team developed the process was systems architecture engineering, using Simcenter Amesim software, a suite of tools for modeling and analyzing multi-domain systems. Using a set of libraries containing predefined components for different physical domains, system architects could model, analyze and predict the performance of the mechatronics system in the Extra 330LE.
“I have to look at many different architectures and configurations. To do this I need to be able to quickly rearrange the model. With the tools we used before such as in-house codes and 3D simulations, this would take weeks. With Simcenter Amesim, we can do this in a matter of days,” says Marcus Sons, system architect, Siemens eAircraft team.
Simulation advantage
Engineers are now using the 1D solution Simcenter Amesim to test physical components individually by simulating the surrounding individual components within Simcenter Amesim.
“So we do hardware-in-the-loop and software-in-the-loop testing. And we only have one physical component and Simcenter Amesim can do the rest. For me, 1D simulation is all about speed and flexibility,” adds Sons.
As the team starts the journey towards final testing and flight certification, the LMS testing solutions in the Simcenter portfolio will help to verify and validate the eAircraft.
The evolution of the various e-planes continues to progress not only in size, but in power as well — and all in a rather short period of time. This will be especially challenging because even though there are established procedures for testing aircraft that have been developed over generations, this is not the case for electric aircraft. Since the certification standards still need to be worked out, it is important to have the right testing tools.
“The LMS SCADAS XS is very nice because it is small and light. We just have to worry about putting sensors into the airframe,” says Anton Dilcher, integration project manager. LMS SCADAS XS can be put almost anywhere. By combining this with a LMS Test.Lab system, we are able to very quickly look at test data right after the flight to make sure that the data is right and that we have good data. At the same time, it remains a very powerful tool so that we can do detailed analysis when we are back in the office.”
“And this is the real secret. You can only take such big steps by simulating all the effects that dominate the design of such a machine at the same time in a consistent environment. This is how Simcenter has helped us do this leap ahead,” concludes Dr. Frank Anton, head of Siemens eAircraft.
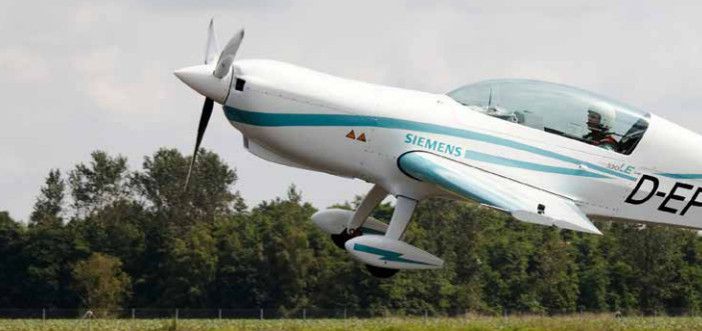
Q&A: Dr. Frank Anton Head of eAircraft, Siemens & Dr. Jan Leuridan – Senior Vice President, Simulation and Test Solutions
How did Siemens become involved in the eAircraft project?
Dr. Anton: The first discussions started around 2010 with the former CTO of Airbus Jean Botti. Both of us felt that electric propulsion could be feasible. We started with very small test flights: just a 60kW motor glider. We realized that there was more potential than we thought. Today, Siemens, Airbus and Rolls-Royce have started a bigger partnership, the E-Fan X, to show the feasibility of using even more powerful two-megawatt electric generators on board a regional plane by 2020.
How is the Siemens eAircraft influencing new concepts in aviation?
Dr. Leuridan: We will see aircraft evolve into different structures, like blended wing structures and more distributed propulsion. It will push the systems that are integrated into the aircraft as well in terms of new technology. On the production side, we will see progress with additive manufacturing and new materials, like components. New aircraft design will also take advantage of connectivity, like the Internet of Things and cloud computing. This can be used to optimize lifecycle management when the planes are in service. This information will be used during the next stages of development as well.
What are some of the challenges facing electric propulsion?
Dr. Anton: There are two challenges. The first is that the power density needs to be one degree of magnitude higher than a normal drive train. For example, one kilogram of machine weight usually required one kilowatt, but for electric propulsion we have to count on 10 kilowatts or even more. This is challenge number one. The second challenge is certification. Aviation needs absolute safety. All subsystems and components have to be certified. This is the second and maybe the bigger challenge that we are facing.
What still needs to happen from an engineering point of view?
Dr. Leuridan: There is definitely a further need to integrate systems engineering into the design process. By coupling systems engineering with product lifecycle management, we can provide more capabilities for end-to-end traceability from requirements to functional analysis and logical system design. This is also critical when meeting safety standards.
What is key technology-enabler for the Siemens eAircraft?
Dr. Anton: I get asked what the secret to this machine is quite often. Yes, of course, we are using the best available materials. We are using the best technologies. The most important thing is that we simulate all the effects of the electric drive train – the machine, the power electrics, the magnetic effects, the stress-strain balances, the cooling – everything at the same time in one Simcenter environment.
Most of the design work happens on the digital twin and not on a physical prototype, correct?
Dr. Anton: The digital twin changes along the way. As the engineers come up with better ideas, we test these ideas on the digital twin to find out whether the idea is good enough or not. At the end, we have our final digital twin and the real prototype, in this case the Siemens eAircraft. So from this point, the development works in parallel. We use the Simcenter portfolio to prepare the digital twin and prepare for the physical testing phase.
As the industry shifts towards simulation, what happens to testing?
Dr. Leuridan: Obviously, you will never fly a plane before completing an elaborate certification process. Testing will continue to play an important role in this process. Within the Simcenter portfolio, we have a number of solutions that are already used throughout the industry worldwide for certification like ground vibration testing (GVT) and flutter testing. Of course, with the Siemens eAircraft, you can think differently about fly-over noise, another industry challenge at the moment. We have been working together with Dr. Anton’s team and I think we’ve done the first-ever fly-over noise measurements on an electric airplane in the world.
So when will we all be flying a Siemens eAircraft and where will we be able to go?
Dr. Anton: We share the vision with Airbus that by 2030 hybrid-electric aircraft will be carrying 100 to 150 passengers over typical regional distances of 500- to 600km, maybe even 1,000km. We are seeing this developing very fast. My personal goal is in my lifetime I will buy a ticket for a hybrid-electric flight between Nuremberg and Paris. I will be sitting in a hybrid-electric plane with 50 other people who have bought a ticket for the same purpose – to get from A to B and finding this absolutely normal.