Embraer subsidiary Eve Air Mobility achieved two significant milestones in the development and testing of its eVTOL last month, completing wind tunnel testing and the first phase of ground testing the aircraft’s propellers.
Eve’s eVTOL aircraft features a lift+cruise configuration, using dedicated rotors for vertical flight and fixed wings to fly on cruise. Able to carry four passengers plus a pilot, the range of the aircraft is around 100km (60 miles).
The company plans to start building its first full-size eVTOL prototype later this year, to commence a flight test campaign next year, and to have the production aircraft certified and in service during 2026.
Alice Altissimo, vice president of program management and operation of Eve said, “We are very pleased with our program development activities to date and making very good progress as we move toward the selection of primary suppliers and finalize the definition of our aircraft systems architecture.
“We continue to invest and our team is working hard with the goal of developing a mature aircraft for certification and entry into service in 2026.”
Propeller and truck-testing
Ground testing of the eVTOL’s propellers was conducted in Brazil to measure the propeller’s aerodynamic performance and sound properties. The company said that the data gathered is being used for modeling and development. The testing involved testing multiple models on a rig to improve efficiency and reduce sound footprint and operating costs.
The company also recently began truck testing its vertical lift rotors to evaluate the performance of rotors during the transition phase of flight.
Truck testing – traveling up and down a runway with the test rig – enables engineers to replicate environmental conditions during take-off and landing so they can test full-size parts or aircraft structures outside of space-restricted wind tunnels. According to Eve engineers have already begun gathering data on the aerodynamic characteristics of rotors in forward flight using truck testing.
Wind tunnel testing
Eve has recently completed wind-tunnel testing, at a wind tunnel near Lucerne, Switzerland using a scale model.
The main objective of the test was to investigate and validate how components including the fuselage, rotors, wing, tail, and other surfaces would perform in flight. The data will be used to validate production solutions, development tools, and models which also include other test articles such as fixed and moving rigs, flying vehicles, and other wind tunnel tests.
“The completion of wind tunnel testing is an important engineering milestone as we continue the development of our eVTOL,” said Luiz Valentini, chief technology officer at Eve Air Mobility. “The information we obtained during this phase of development has helped us further refine the technical solutions of our eVTOL before committing to production tooling and conforming prototypes. Our goal is to design, produce and certify an aerodynamic and efficient eVTOL that will be used for a variety of urban air mobility missions.”
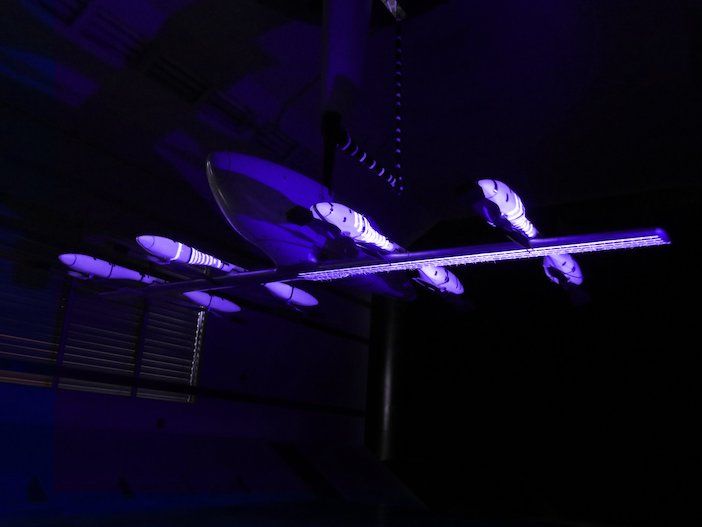
Eve’s said its engineering team would also use the data gathered through wind tunnel testing to continue to develop the eVTOL’s control laws leading to optimize performance and passenger comfort.
Data from the wind tunnel tests, the propeller, and truck-testing are being combined to increase the fidelity of Eve’s flight simulator and fly-by-wire system. Meanwhile, Computational Fluid Dynamics (CFD) simulations are ongoing in an effort to mature the analysis of the transition between the hover and cruise phases of the flight.