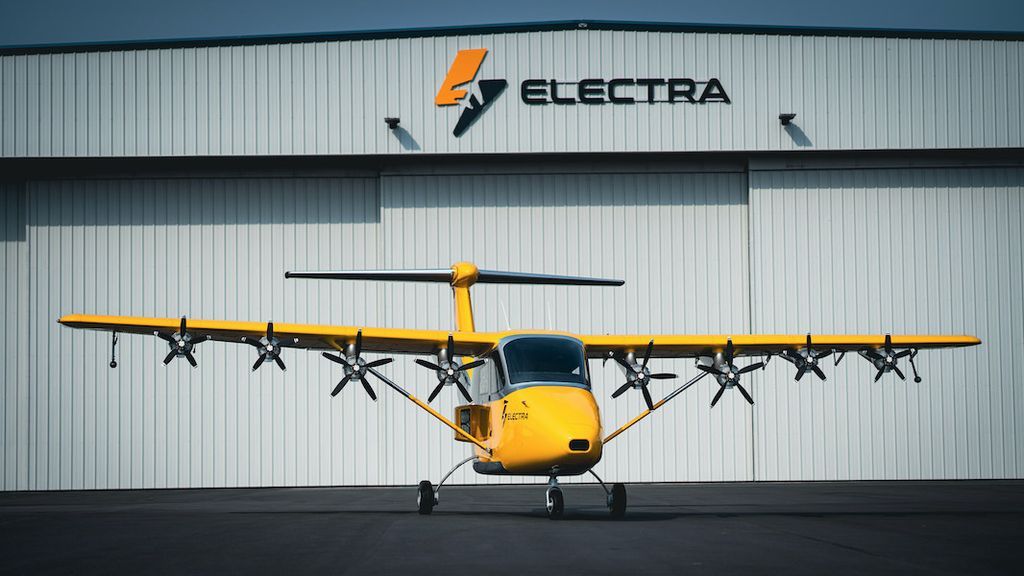
Electra.aero has revealed its first full-size aircraft this month, a two-seat demonstrator to validate the company’s innovative short take-off and landing technology.
The defining feature of this aircraft is its use of an aerodynamic concept called blown lift to operate from exceptionally small places, with take-off ground rolls of just 150ft (45m).
For comparison, one of the aircraft with the shortest minimum take-off and landing distances on the market is the Pilatus PC-6 STOL single engine turboprop, which requires a minimum runway length of 640ft. A single aisle airliner such as the A320 requires a 6,000ft long runway.
The blown lift technology will be used in a nine-seat hybrid-electric regional airplane that the Virginia, USA-based startup plans to certify in 2028.
Electra’s first commercial aircraft will be certified under FAA Part 23 and will use a 600kW hybrid-electric powertrain. The electric Short Take-Off and Landing (eSTOL) aircraft will be the first of its type and have a range of 500 miles (800km) plus 45 minutes reserve. It will be capable of carrying nine passengers plus a pilot, and have a cruise speed of 200mph (320km/h) at 10,000ft.
According to Electra, its eSTOL aircraft offers key advantages over eVTOL aircraft during flight, such as increased range and comfort. In addition, the eSTOL aircraft’s capability to take-off and land quietly from short runways will enable it to be used in and from urban areas in the same way as eVTOL air taxis or regional shuttles.
At the end of last year, the company had letters of interest for 1,214 aircraft from 32 operators based around the world, including launch customer helicopter operator Bristow.
Blown lift validation
Although aircraft have flown before that use blown lift, the test aircraft revealed this month will demonstrate Electra’s implementation of the aerodynamic concept at full size for the first time. The first flight of the demonstrator will be a key milestone for the company.
The blown-lift concept uses propellers on the leading edge and large flaps at the rear of the wing to blow more incoming air downwards. This enables the aircraft to lift off the ground at slower speeds and therefore use shorter runways.
Electra, which was founded in 2020 has so far conducted computer simulation and modeling, run wind tunnel test programs and has flown scaled models of its eSTOL design. The company’s engineers have also built and tested a 150kW hybrid-electric propulsion system for the test aircraft and performed iron bird testing.
The two-seat, piloted, technology demonstrator aircraft revealed this month uses modified wings from a Cessna 172 while the rest of the airframe is new. The airframe is completed and the team is currently integrating and testing systems in preparation for its maiden flight.
“The original concept was to start with a Cessna 172 as the basis for the whole airframe to reduce cost, but early in design it became clear that the systems integration favored a clean-sheet design,” said JP Stewart, vice president and general manager of Electra.aero.
“The two-seat demonstrator is about showing we can make a full-scale ‘real’ aircraft that takes off in 150ft and enables us to learn everything we need to know about the performance, control, and systems management to move confidently to the next larger aircraft. It’s about methodically reducing the risks in development performance, schedule, and cost.”
A key decision for the program was that the demonstrator aircraft should be piloted instead of unmanned. Stewart said, “There is a lot of insight that an onboard pilot brings to the table that you do not get with an unmanned aircraft. If the aircraft is unmanned, the decision to take more risk becomes more of a financial decision to cover the cost of a crash and replacement.
“We have a clear flight date target but safety is absolutely primary, and we will fly when the aircraft is ready. One of our team members and friends will be flying onboard this aircraft on day one so safety is everything.”
The demonstrator will also play a crucial role in flight testing of the novel hybrid-electric propulsion system. Electra worked with partners to develop the propulsion system to provide a more detailed understanding of it but does not intend to make its own propulsion system in the future.
“There isn’t a complete propulsion system that you can just plug into this airplane, and you don’t have an aircraft without a propulsion system,” said Stewart. “Once we had a propulsion system working, we built the aircraft around it.”
Propulsion integration
The blown-lift aerodynamic concept was first devised more than 100 years ago and is applied to a certain extent in large modern airliners. However, attempts to take advantage of the concept in a STOL have never really been fully realized. The most successful is the Breguet 941, developed by a French company in the 1950s and 1960s (see pg82: Aft Cabin).
According to Stewart the use of distributed electric propulsion (DEP) technology makes blown lift viable in the 21st century. The use of eight electric motors along the wing significantly simplifies the engineering required. A major drawback of the Breguet 941 was the complicated mechanical gearbox and powershaft arrangement it required.
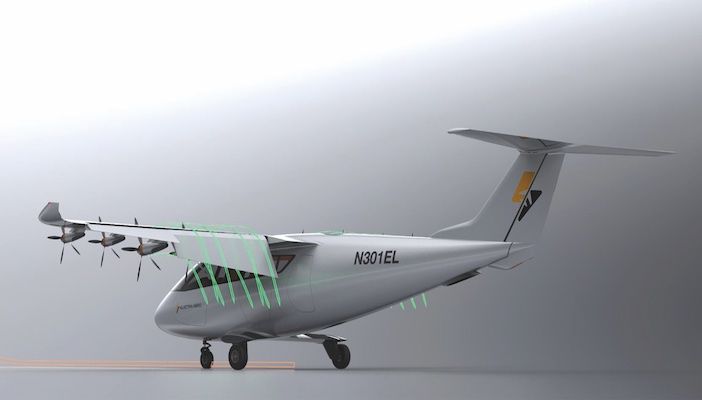
He said, “What makes this possible now is the use of DEP. To make blown lift work best, you need to be able to bathe the whole wing in the propeller airflow – in the past, this was accomplished with turbofan and turboshaft engines directly on the wing. But you can only make turbines so small and when you do, they become expensive, less reliable, and increase specific fuel burn.
“With electrification, we can have high power in a relatively small package and we do not need the mechanical complexity of shafts and gearboxes to distribute the power and provide redundancy.
“The hybrid system then has an efficient turbine designed to run at one optimal operating point to provide nearly ten times the range of battery-only aircraft.
“We can also make the aircraft more efficient by integrating the propulsion into its design. How we place the motors and design the wing and flaps in consideration of the motors is the propulsive
aero-integration advantage of DEP.
“This DEP-enabled blown lift lets us increase the lift coefficient of the wing roughly three to four times that of traditional aircraft. In effect, it makes the wing much bigger aerodynamically than it is physically. That lets you take off and land at very low speeds around 30 knots, [35mph, 55km/s].
“You can then take off and land at very short distances with comfortable accelerations akin to a car at a stop sign.”
Electra has conducted truck testing of the eSTOL’s wing. This entailed attaching the wing to a trailer with ballast and driving down a runway up to 35mph (55km/h).
Truck testing is being used to help validate the concept before the first flight. “Effectively truck testing is an external wind tunnel, a shortcut for validating the concept,” said Stewart. “The most important data is the force and moments from the high lift system and the motor powers, so there was instrumentation within the wings, strain gauges, and load cells, to measure the flap moments and the aileron moments.”
“Truck testing cuts down on the amount of flight testing. It’s a way to get the data you care about in a cost and schedule-effective way.”
Potential markets
According to Stewart, DEP is best suited for smaller regional aircraft. The 32 operators who plan to use the aircraft will offer regional passenger and cargo transport, VIP, and medical flight services. He said, “For Advanced Air Mobility [AAM] to work for the end user you need to be saving passengers time by being close to where they are, which means being able to operate from smaller areas.”
“You do need VTOL to access some small spaces like the top of a tall building, but our research found that many of the use cases do not exclusively require it.
“By using eSTOL, you save the weight of a full vertical propulsion system and can get a much more effective aircraft – two and a half times the payload and ten times the range. In the aviation business where thin margins represent profitability, this is a huge difference.”
Despite the shorter runway advantage, of the operators who have signed letters of intent two thirds are not building new infrastructure to operate the eSTOL. Stewart said, “We believe uptake of eSTOL will start with operators on existing routes operating from airports before evolving into new take-off and landing sites that use the full capability of the aircraft.
“Our entry point to the market is fixed-wing aircraft with less than 20 seats, Beavers, Otters, King Airs, Cessna Caravans and Pilatus PC-12s.”
Electra was founded by John Langford, an aviation pioneer and the founder of Aurora Flight Sciences, which Boeing acquired in 2017. Last year, Electra acquired competitor eSTOL aircraft developer Airflow, a startup founded by engineers formerly in a STOL program that was part of Airbus’ Vahana Silicon Valley technology incubator.
Stewart said R&D has shown that the blown lift concept can be effectively applied to much larger regional aircraft and that there is historic evidence in the Breguet 941, which was designed for nearly 60 passengers. Electra has also received US Government funding from the Department of Defense and NASA in the form of R&D contracts. “There is lots of interest from defense, particularly for distributed logistics and special mission operations,” he added.
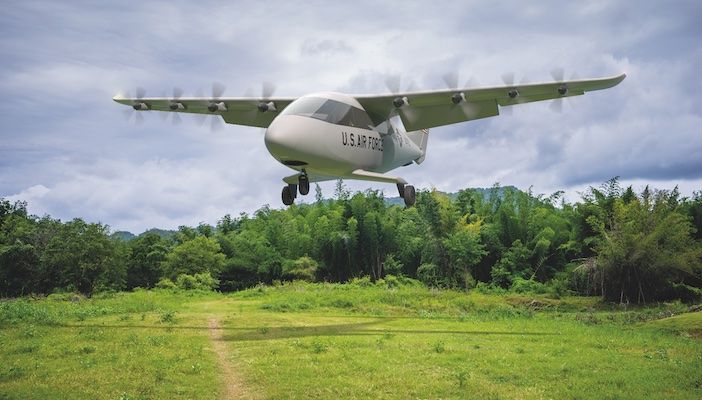