Spanish startup Pangea Aerospace is to ground test the aerospike engine for the reusable rocket it is developing at the German Aerospace Center (DLR’s) Lampoldshausen site.
The aim of the program is to test several aerospike engine designs which engineers at Pangea believe can improve rocket engine efficiency by up to 15%.
Hot-fire tests will be carried out from next month using several technology demonstrators developed by Pangea Aerospace and installed on the European research and technology test stand P8. The comprehensive functional tests will be an important step for Pangea towards a first flight.
Stefan Schlechtriem, director of the DLR Institute of Space Propulsion at Lampoldshausen said, “By working together with start-ups, we can make the next launcher generation more efficient and competitive. The microlauncher segment is particularly interesting in this regard. These are small launch vehicles carrying payloads of a few hundred kilograms into low-Earth orbit. Innovative propulsion technologies are often used here. At DLR Lampoldshausen, we are ideally positioned to test these.”
Adrià Argemi, CEO of Pangea Aerospace said, “The space industry is drastically being transformed and new solutions are sought to be more competitive. The aerospike engine has been considered as a most promising solution in rocket propulsion for decades, but it is only now that this technology can be built and engineered, thanks to new materials, and the design freedom that additive manufacturing provides.
“It is great to be working with DLR and to be able to fire the first copper additively manufactured aerospike engine in the world.”
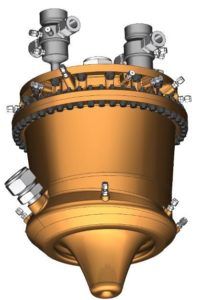
Pangea’s two-stage Meso rocket is expected to carry up to 150kg of payload into low-Earth orbit and features an engine with a nozzle in the shape of a spike, enabling it to adapt more flexibly to different flight altitudes.
The company has the exclusive capabilities in Europe for a new material called GRCop42, a powder copper alloy optimized by NASA for additive manufacturing and will be 3D printing the Meso rocket engine’s combustion chambers. The rocket will use liquid oxygen and liquid methane as propellants.
The company is one of several around the world developing so-called microlaunchers to improve access to space.
“Our test facilities already cover the entire portfolio of tests on engines of all types and sizes. They are available to small and medium-sized enterprises and start-ups,” added Schlechtriem. “With every test on one of our test stands, we gain valuable new knowledge together. This in turn flows into the development of new engines. This makes us a unique and valuable partner for institutional and private space transport.”