The US Air Force Research Laboratory is investing US$60 million into research to develop improved anti-corrosion coatings for aircraft and upgrading its Supersonic Rain Erosion Test Rig at Wright-Patterson Air Force Base.
The five-year, $60 million research program is being led by the Nonstructural Materials division University of Dayton Research Institute (UDRI). Researchers on the project will develop, test, evaluate, qualify and integrate the new coatings on to US Air Force aircraft as part of the program, to reduce system maintenance time, cost, and down time and improve safety to personnel and the environment.
Researchers will also work to develop testing that will better predict the lifespan of new protective systems and materials in the field.
Matt Rothgeb, group leader for coatings, corrosion and erosion at UDRI and principal investigator for the new program said, “One of the most important ways to help extend the life of an aircraft is to prevent damage from corrosion and erosion.
“We’ve led research, development, testing and evaluation of coatings and corrosion-prevention technologies for nearly 20 years, so we’ve seen first-hand the effects corrosive damage can have on the safety, affordability, and availability of aerospace systems across the Air Force and the aerospace community as a whole. Aircraft coatings are critical to mitigating corrosion and erosion of structural components.”
New test methods and equipment to evaluate and qualify erosion-resistant materials will be developed as part of the project, using the erosion labs at Wright-Patterson Air Force Base. Researchers will also aim to develop accelerated testing and tools to better predict how new coatings systems will hold up over time and in service conditions, such as extreme temperatures and humidity. “Understanding the phenomena of corrosion and erosion is key to developing better protection materials, designs and systems,” Rothgeb said.
Supersonic rain
Meanwhile a key part of Wright-Patterson Air Force Base’s erosion labs, the Supersonic Rain Erosion Test Rig (SuRE) is being upgraded. The SuRE is used to evaluate structures and coatings under the effects of high speed flight through rain for transonic and supersonic speeds up to Mach 2.3 and has been used to test missiles, Navy propellers and commercial space launch vehicles.
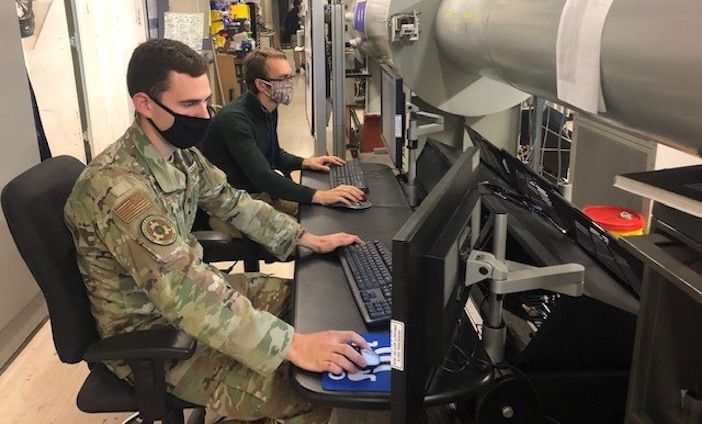
The SuRE is used to test components and coupon specimens such as radomes, leading edge materials, and window materials. The only other method to reach this speed for component testing is with a rocket sled or flight testing, both of which are expensive and time consuming.
The improvements underway include features to introduce flexibility in the executed erosion pattern, and the replacement of the current control hardware with NI’s LabVIEW interface .
“The rig upgrades are really taking shape,” said Dr. Matthew Hartshorne, Erosion Area Lead. “With two out of three phases complete, we were able to put the control and automation upgrades to the test during a recent run. The control system performed very well and the advantages of modernizing the rig to current technology were evident. We were able to change operating parameters on the fly and monitor the system from a central station instead of walking around the large rig to individual gauges. I am excited to offer the final product to our customers. The team has done a great job making this happen, all during the Covid-19 restrictions.”
Learn more about rain erosion testing, here