GE Aerospace’s is opening a testing facility and rolling-out a new x-ray based device for inspecting engine parts to its global network of repair shops.
The Service Technology Acceleration Center (STAC) is to open in Springdale, Ohio this September to help deploy new inspection and repair processes to its MRO (maintenance, repair and overhaul) shops globally.
Amongst the first tasks of engineers at the STAC will be to help introduce new NDT (nondestructive testing) technology in the form of an open beam x-ray fluorescence spectroscopy (XRF) inspection device.
The XRF device has been developed by GE Aerospace in partnership with Bruker to detect microstructural variations in metal parts and improve the quality and detail of part inspections.
GE Aerospace said the XRF will help reduce costs by ascertaining airworthy repaired parts more clearly so that they can be returned to operation in lieu of replacing them entirely with new parts.
XRF is also used by museums and auction houses to identify forged artwork.
Nicole Jenkins, chief MRO engineer at GE Aerospace said, “We’re excited to be opening our new STAC facility, which will serve as a major accelerator for scaling and deploying cutting edge inspection and repair processes to market.
“We have already begun moving equipment into the facility and preparing to launch our first inspection process, that takes a page from the art world to improve the quality and speed of detecting chemical anomalies in metal parts.”
Thomas Schuelein, president of Bruker’s Nano Analytics Division said, “We are excited to extend our most advanced XRF technology into the aerospace industry, contributing to set a new standard in nondestructive chemical analysis techniques and therefore helping to support aircraft component re-manufacturing quality.
“This first successful program under the joint technology development agreement with GE Aerospace underlines Bruker’s commitment to innovation, and we look forward to further breakthroughs in this sector.”
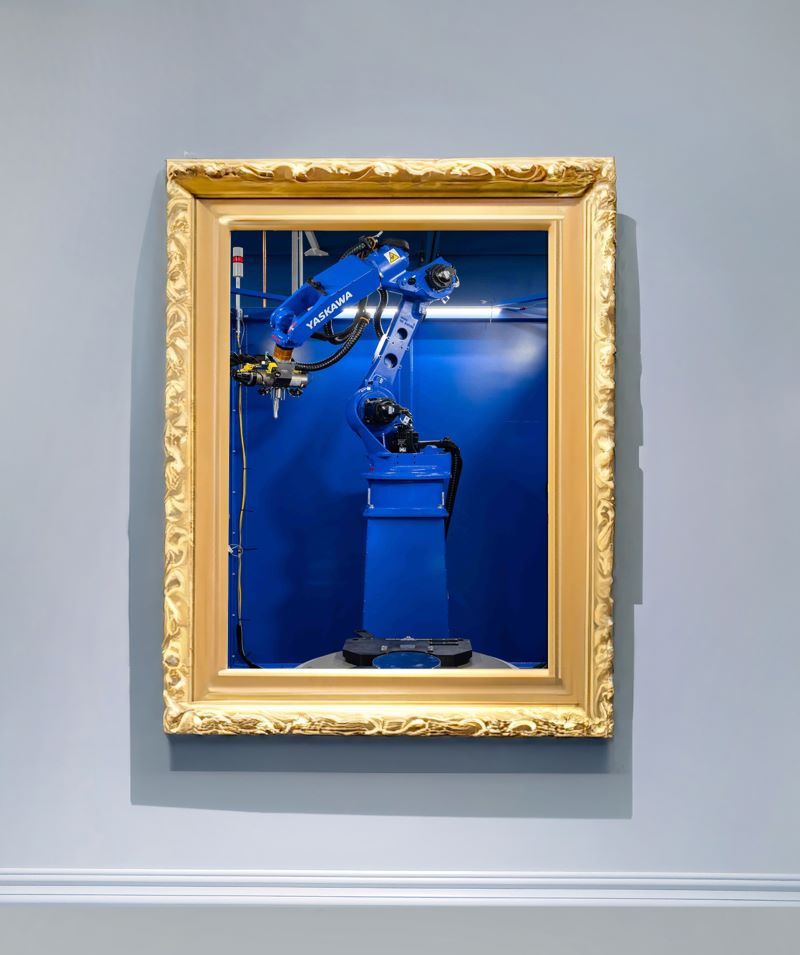
Chemical bonds in jet engines and art
In art and conservation, XRF is used to image and see aspects of an art object’s chemical composition that can tell you about the history of its origin and how to restore it or, in some cases, whether the piece is real or fake.
For metal part inspections, the XRF provides a view of the part’s chemical composition that can help a service engineer more-readily spot anomalies.
The new process using x-ray is one of a range of imaging methods and techniques engineers use for inspecting engine components. Ultrasound, computed tomography, flash thermography, eddy current testing, fluorescent penetrant inspection, and dimensional metrology are also used depending on what can best interrogate a given material or part.
The STAC was first announced in December 2022