Making room in your flight test instrumentation toolbox with a quick, light, non-intrusive and universal reaction kit is a good idea.
Many constraints apply to flight test instrumentation. It must be designed to be integrated into a complex and often tiny structure and to face extreme environments while targeting to get ever more knowledge about the test vehicle.
The IoT (Internet of Things) paves the way to a lot of new technologies, for example wireless or low power. At the same time, electronics continue to gain in performance while reducing power requirement and size. Inspired by the flight test community’s feedback, Safran Data Systems decided to investigate an alternative form factor to the parallelepiped housing. The main drivers of the exploration process, presented hereafter were, ease of installation, ease daily operations and minimize intrusiveness of data acquisition units. The product is called µMA.
Design specific mounting plates to install the devices in the test vehicle is costly, time consuming and affects the reactivity facing changing conditions. The cylindrical shape is a good fit to cylindrical connectors and allows using COTS brackets, clamps or straps already used in the vehicle itself.
One of the key drivers was to propose an architecture that would offer all the versatility expected and cope with unique needs. A building brick concept, based on cylindrical cells that host the electronic parts, enables the product to be modular and versatile. The complete assembly / disassembly of the device is simple and does not require any tool.
Keeping the device as small as possible was a heavy constrain. The sweet spot between the downscaling willingness and the kind of features needed to be embedded in the device led to an optimal diameter being about 20mm.
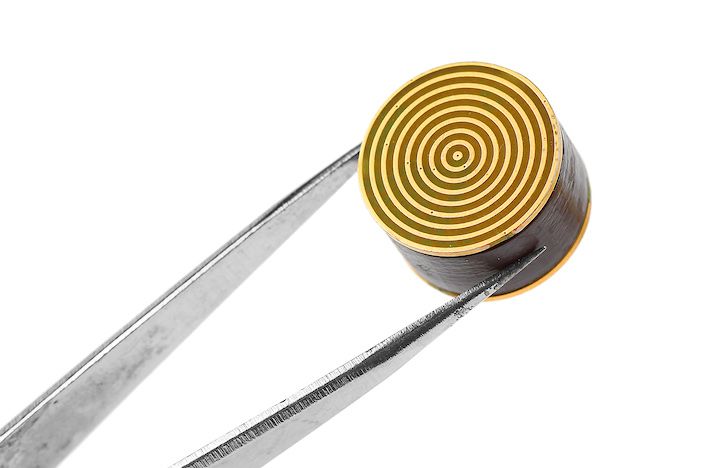
The product is composed of a few types of cells. The acquisition cells host the analog signal conditioning front-end and the analog to digital converter. A data storage optional cell can be added in the device.
The energy source can be of various kinds: internal with battery (button cell, AA cell, 18650 cell) or external through Power over Ethernet (PoE). The Processing and Datalink cell handles the communications and synchronization with the FTI network, other µMAs, a mobile device or a PC through wired or wireless communications.
The product is also capable of auto-discovery and self-configuration, following the default behavior selected by the user, for example maximum performance or best energy management.
From an architecture point of view, it is possible to use the µMA product independently but also connected to each other with or without wires, as a light FTI with a new type of distributed architecture but also as an extension of an existing FTI for last minute modifications for example.
This achievement is not trivial. It has required capitalizing on decades of experience in innovation and development of instrumentation systems, imagine new solutions and usages with instrumentation players, thinking of systems and architectures in a new way, to develop a new modular approach of 3D electronics, and to investigate low-power, wireless and energy technologies from the world of IoT and adapt them to the flight test instrumentation environment.
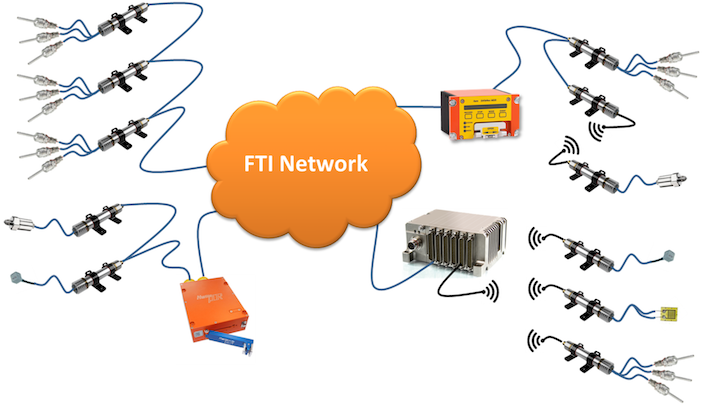
The investigations and tests in Safran Data Systems labs, Test & Training Center and in real environments, demonstrate that this new approach of the design and usage (data acquisition unit as close as possible to the sensor, no modification of the structures, immediate reaction capacity, live troubleshooting, auto-configuration, plug and play, rapid reconfiguration) generates real gains in instrumentation, testing and certification activities. The overall µMA product has been patented.
This article was provided by Safran Data Systems.