Materials scientists in China are developing a material that mimics the structure of polar bear fur for application in aircraft structures.
The insulation provided by a polar bear’s fat, skin and fur helps them survive in the frigid Arctic. Unlike the hairs of humans or other mammals, polar bear hairs are hollow. Zoomed in under a microscope, each one has a long, cylindrical core punched straight through its center.
The shapes and spacing of these cavities have long been known to be responsible for their distinctive white coats. But they also are the source of heat-holding capacity, water resistance, and stretchiness, all desirable properties to imitate in a thermal insulator.
Engineers at the University of Science and Technology of China (USTC) in Hefei, Anhui province, have therefore been trying to recreate the structure of individual polar bear hairs for industrial exploitation as part of a research project.
Their work was published in the journal Chem this month. Co-senior author of the study, Shu-Hong Yu, a professor of chemistry at USTC said, “Polar bear hair has been evolutionarily optimized to help prevent heat loss in cold and humid conditions, which makes it an excellent model for a synthetic heat insulator.
Jian-Wei Liu, an associate professor at USTC said, “By making tube aerogel out of carbon tubes, we can design an analogous elastic and lightweight material that traps heat without degrading noticeably over its lifetime. The hollow centers limit the movement of heat and also make the individual hairs lightweight, which is one of the most outstanding advantages in materials science.”
The research team manufactured millions of hollowed-out carbon tubes, each equivalent to a single strand of hair, and wound them into a spaghetti-like aerogel block for testing.
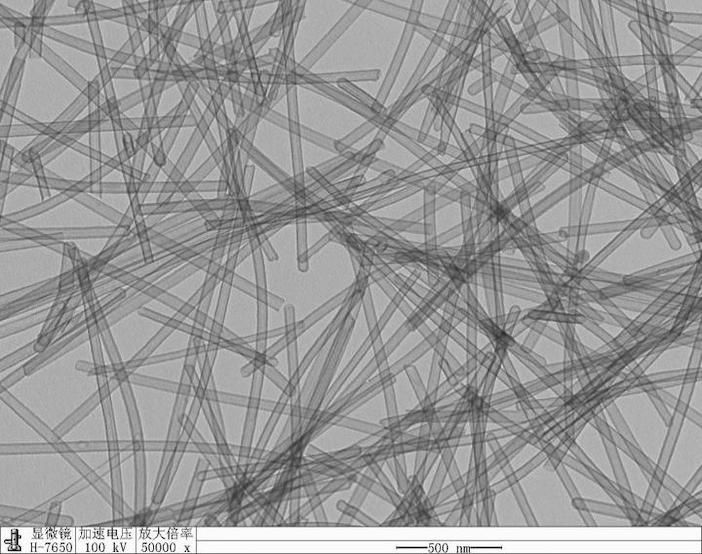
Compared to other aerogels and insulation components, they found that the polar-bear-inspired hollow-tube design was lighter in weight and more resistant to heat flow.
It was also hardly affected by water, a handy feature for maintaining insulation performance in humid conditions and was very stretchy, further boosting its engineering applicability.
The researchers are now working to scale up the manufacturing process to produce an insulator material on the meter scale rather than the centimeter one. “While our carbon-tube material cannot easily be mass produced at the moment, we expect to overcome these size limitations as we work toward extreme aerospace applications,” said Yu.