Rolls-Royce has demonstrated a suite of robotic technologies for inspecting and repairing engines while they are on an aircraft, including swarming cockroach robots, snake-arm robots and remotely-operated probes.
Part of the UK-based aero-engine manufacturer’s Intelligent Engine vision launched in February 2017, the most developed of the technologies is a “remote boreblending robot”, which is planned to be in use within two years.
The boreblending robot is fixed to the side of an engine and inserts a probe inside of it. A camera on the probe scans the compressor blades for damage and builds a 3D point cloud image. This image is compared to a 3D digital model of the engine to determine damage. An expert at a Rolls-Royce Availability Centre then remotely controls the robot and instructs it to grind away the damaged areas using a high-speed air spindle.
Dragos Axinte, director of the Rolls-Royce University Technology Centre at the University of Nottingham and the research lead, said, “It can be thought of as like a portable CNC machine tool. An unskilled operator can bolt it on the engine so the specialist from Derby can operate and repair the engine.”
The robot has taken three and a half years to develop to its current demonstrator stage. Dr James Kell, Rolls-Royce’s on-wing technology specialist, repair technology, said, “It will allow us to service our engines in hours rather than days.”
Other robots being developed by Rolls-Royce and academic partners include miniature “periscopes”, fiber-optic networked cameras embedded within engines that would provide visual data to complement the data already gathered by other vibration, acoustic and temperature sensors.
The company is also developing pairs of small ‘snake-arm’ robots able to inspect engines using a proprietary non-destructive testing technique, remove damage and carry out patch repairs on damaged thermal barriers.
In addition, a project with Harvard University is developing small robotic cockroaches – measuring 4.5 x 1cm and weighing 1.8g each – that are deployed via a long tube inside the engine to perform visual inspections of hard-to-reach parts, such as the combustion chamber.
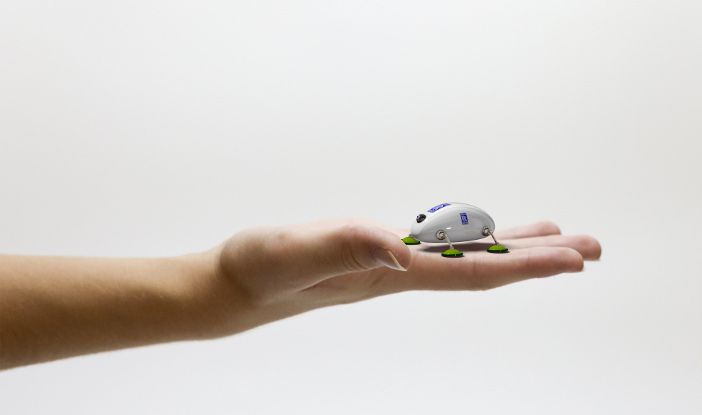
Sebastien de Rivaz, research fellow at the Wyss Institute, Harvard University, said, “We’ve been focusing on the manufacturing techniques. We want to scale it down to fit in borescopes and put cameras on it. They are autonomous and transmit their perspective to a central location. Instead of five hours we could carry out an engine inspection in five minutes.”
Kell added, “While some of these technologies, such as the Swarm robots, are a long way from everyday reality, others are being tested and will be introduced within the next few years. We have competition in this field, but all of these technologies are unique to Rolls-Royce.”