Eddyfi Technologies provides nondestructive testing (NDT) inspection technologies, with a focus on advanced phased array ultrasonic testing, eddy current array, and other ultrasonic and electromagnetic equipment including instruments, sensors, software and robotic solutions.
In this article Daniel Richard, solutions development expert at Eddyfi Technologies discusses Friction Stir Welding (FSW) and recent advances and future developments in Phased Array Ultrasonic Testing (PAUT).
Q: Can you describe friction stir welding (FSW) as a manufacturing technology, its advantages / disadvantages, its applications in aerospace ? Is it usage growing? If yes why?
Friction Stir Welding (FSW) is an advanced solid-state joining process used to weld materials without reaching their melting point. The process involves a rapidly rotating tool that is plunged into the welded area and moved along the joint, generating frictional heat that softens the material without melting it. The plasticized material is then mechanically stirred together, forming a high-integrity weld with superior mechanical properties.
FSW offers several key advantages over traditional welding techniques:
- Minimal Heat Distortion: Since the process occurs below the material’s melting point, it reduces residual stresses, shrinkage, and distortion, which is particularly critical in aerospace applications where precision is essential.
- Defect Prevention: Solid-state welding eliminates common defects associated with fusion welding such as solidification cracking, porosity, and lack of fusion.
- High Mechanical Strength: The resulting welds exhibit excellent mechanical properties, often surpassing those of the base material, ensuring structural integrity in high-performance applications.
- Automation and Efficiency: FSW is well-suited to automation, enabling high-speed, repeatable welds with minimal human intervention, making it ideal for large-scale aerospace production.
While FSW offers significant benefits, it does have some limitations:
- Initial Equipment Investment: FSW requires specialized machinery with high axial force capabilities, making the initial setup costly.
- Material Thickness Restrictions: The process is most effective for medium-thickness materials, with challenges in welding very thin or thick sections without process optimization.
- Joint Accessibility: Due to the rigid nature of the rotating tool, FSW is primarily suited for linear and circumferential welds rather than complex geometries.
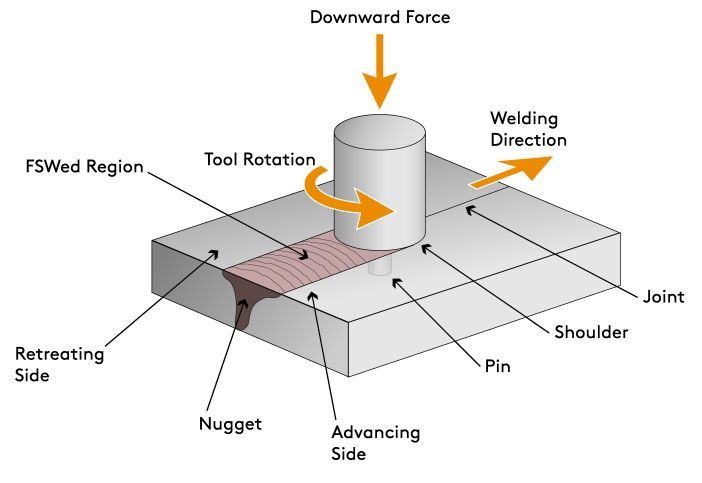
FSW has been widely adopted in the aerospace industry for the fabrication of aluminum structures, particularly in applications where high-strength, defect-free welds are essential. Common aerospace applications include:
- Aircraft Fuselage and Wings: Large aluminum panels are welded using FSW to enhance structural strength while minimizing weight.
- Fuel and Cryogenic Tanks: FSW is extensively used in rocket and spacecraft manufacturing to join fuel tanks and cryogenic storage components, ensuring leak-proof and high-strength welds.
- Launch Vehicles and Spacecraft Components: Space companies and established aerospace manufacturers increasingly rely on FSW to fabricate lightweight, high-performance structures.
The use of FSW in aerospace is growing significantly, driven by several factors:
- Expansion of Commercial Space and NewSpace Market: The rise of private space companies has accelerated demand for lightweight, high-strength welded structures in rockets and spacecraft.
- Shift Toward Aluminum-Lithium Alloys: Aerospace manufacturers are adopting advanced aluminum-lithium alloys, which benefit from FSW’s defect-free joining capabilities.
- Automation and Cost Efficiency: With the push for more automated and cost-effective manufacturing solutions, FSW is increasingly favored for its high-speed, repeatable welding process.
As the aerospace sector continues to innovate, friction stir welding will play a crucial role in enabling lightweight, high-strength structures that meet stringent performance and safety requirements.
Q: Are there any challenges associated with inspecting friction stir welded parts? Any there any challenges unique to the aerospace sector?
While FSW is known for producing high-quality, defect-resistant welds, Non-Destructive Testing (NDT) remains essential to ensure structural integrity, particularly in aerospace applications where safety and performance are paramount. Several defect types can occur, requiring advanced inspection methods to detect and evaluate them accurately.
- Voids: Small isolated voids can form in the welded material, potentially affecting strength.
- Wormholes: These elongated voids align with the welding direction and can extend several millimeters, weakening the joint.
- Lack of Penetration: Incomplete weld penetration at the root can create a weak bond, posing a high risk of failure under stress—a critical concern for aerospace applications.
- Kissing Bonds: A particularly challenging defect caused by oxide layers preventing proper material fusion at the weld root. Since it remains partially bonded, it is difficult to detect with conventional NDT methods.
Beyond internal defects, FSW also introduces surface characteristics that can complicate NDT inspection:
- Surface Patterns: The rotating tool creates arc-shaped waves on the weld surface which can introduce signal noise in ultrasonic testing.
- Flashing: Thin excess material at the weld edges can obstruct inspection and may need mechanical removal or compensation techniques to enable NDT evaluation.
In aerospace, structural integrity, weight optimization, and stringent quality control elevate the complexity of FSW inspection. The challenges include:
- Thin-Walled Structures and High-Strength Materials: Aerospace components often involve thin-walled aluminum or advanced alloys that require high-resolution NDT techniques to identify small but critical defects.
- Complex Geometries: While FSW is primarily used for linear welds, aerospace applications often involve curved or circumferential welds (e.g. fuel tanks, fuselage panels), requiring adaptable inspection solutions.
- Detection of Kissing Bonds: Since kissing bonds do not have a clear gap, traditional ultrasonic methods struggle to identify them. This has driven innovation in Phased Array Ultrasonic Testing (PAUT) and advanced signal processing techniques to improve detection capabilities.
- High Safety Standards and Certification Requirements: Aerospace welds must meet strict regulatory standards (e.g., FAA, EASA, NASA, and MIL-specs), requiring repeatable, high-precision inspection methods that can document and validate weld quality with traceability.
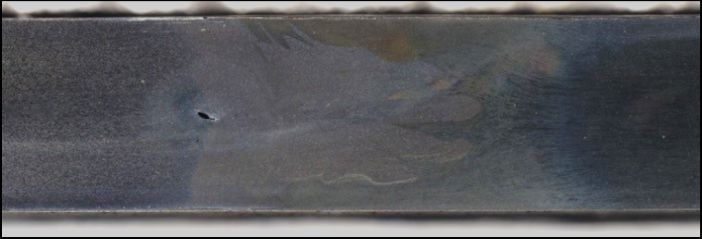
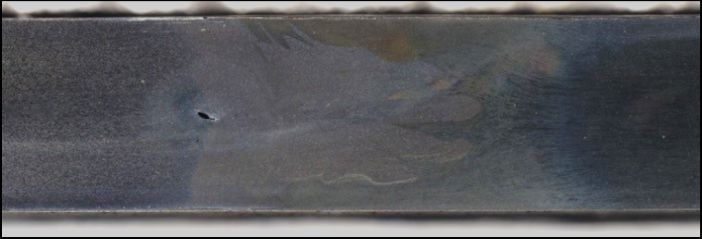
Q: In a similar way can you describe PAUT, how it works its inherent advantages and disadvantages, its usage in aerospace inspection and QC?
One of the primary advantages of PAUT over traditional X-ray inspection is the absence of ionizing radiation. Unlike radiographic testing (RT), which requires specialized shielding and designated enclosures, PAUT can be performed
in an open manufacturing environment. This eliminates the need for radiation bunkers and allows aerospace manufacturers to inspect large components without interrupting other production activities. The ability to conduct inspections on the shop floor, rather than in isolated areas, improves workflow efficiency and reduces logistical constraints.
PAUT offers significant time savings compared to traditional ultrasonic testing (UT) and radiography. With typical inspection speeds of 50mm per second or faster, depending on the scanner configuration and required resolution, PAUT ensures welds are validated in real time. This rapid inspection capability allows manufacturers to identify defects early in the process, minimizing rework and maintaining production efficiency.
Another advantage of PAUT is its compatibility with automated manufacturing systems. In many cases, PAUT probes can be mounted directly on the same mechanism as the FSW machine, enabling immediate post-weld inspection. This integration reduces the amount of hardware required at the weld site and allows for real-time quality control. By identifying potential defects as soon as they occur, manufacturers can make adjustments to welding parameters on the fly, improving overall process reliability.
In the aerospace sector, rigorous quality control and regulatory compliance are essential. PAUT provides a fully digital inspection record, ensuring complete traceability of every weld. These permanent records support defect tracking, trend analysis, and predictive maintenance, allowing manufacturers to optimize welding processes over time. Additionally, auditable PAUT data simplifies certification processes and ensures compliance with industry standards such as FAA, EASA, and MIL-specs.
Aerospace components require a high degree of precision, and PAUT delivers consistent, repeatable results. Unlike conventional UT, which depends heavily on operator technique, PAUT utilizes advanced digital signal processing and automated scanning solutions that enhance the probability of defect detection. This ensures that even challenging defect types, such as lack of penetration or voids within FSW joints, can be accurately identified and characterized.
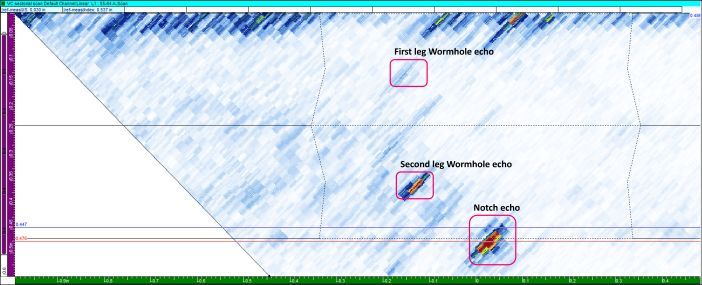
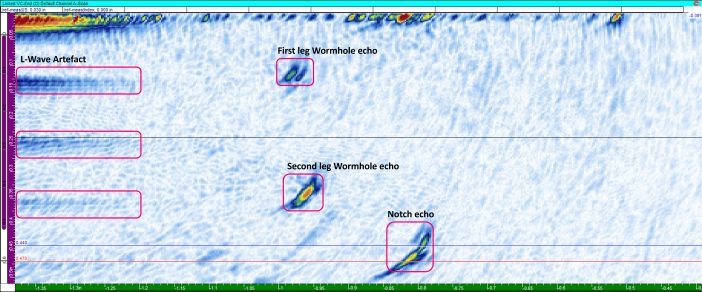
Q: How has PAUT technology been adapted or customized to meet the rigorous demands of aerospace certification?
Phased Array Ultrasonic Testing (PAUT) has evolved significantly to meet the stringent demands of aerospace certification. Early PAUT inspections were largely manual, requiring operators to move probes by hand while interpreting results in real time. While this approach was effective in some industries, it lacked the repeatability, precision, and traceability required for aerospace applications, where strict quality control and regulatory compliance are essential.
To address these challenges, modern PAUT systems incorporate automated scanning technology that ensures consistent probe movement along the weld path. These scanners eliminate variations introduced by human operation, enhancing defect detection accuracy. Additionally, fully encoded positioning allows for precise spatial mapping of inspection data, ensuring that every detected indication is accurately located and documented for certification purposes.
A key advancement in aerospace PAUT is the ability to record entire weld inspections in a single data file, even for welds exceeding 20 meters in length. This level of data capture is critical for:
- Regulatory compliance, providing verifiable proof of weld integrity
- Traceability, ensuring complete documentation for audits and quality control
- Post-inspection analysis, allowing for deeper defect evaluation and process optimization
By maintaining complete inspection records, aerospace manufacturers can meet the strict FAA, EASA, and MIL-spec requirements while improving process control and defect prevention strategies.
The adoption of robotic PAUT systems is transforming aerospace NDT by enabling inspections beyond linear and circumferential weld paths. Unlike traditional scanners, robotic systems can move probes dynamically in three-dimensional space, making them ideal for inspecting:
- Curved aerospace structures, such as fuselages and engine components
- Complex geometries, including welded joints in composite assemblies
- Hard-to-reach welds, improving accessibility without sacrificing precision
This robotic advancement enhances inspection flexibility and adaptability, ensuring consistent weld quality across a broader range of aerospace components.
Aerospace certification demands unwavering accuracy, repeatability, and data integrity. PAUT technology has been optimized to meet these requirements through:
- Automated scanning solutions that minimize human error
- Encoded data acquisition for precise defect localization
- Advanced software-driven imaging for high-resolution defect characterization
- Industry 4.0 integration to support predictive maintenance and manufacturing optimization
Q: What are the main challenges in applying PAUT to the complex geometries and material interfaces typically seen in aerospace stir welds, and how have these been addressed?
Aerospace FSW joints are often 5 mm thick or less, making it essential to use high-frequency PAUT probes capable of detecting small flaws with the necessary resolution. While lower-frequency probes are suitable for thicker welds, 10 MHz PAUT probes provide the required resolution for thin aerospace structures and are widely used due to their availability and proven effectiveness. These high-frequency probes enable accurate imaging of minute defects such as voids, lack of penetration that could compromise structural integrity.
The wave pattern created by the rotating tool head during FSW presents another inspection challenge. If the weld surface is too irregular or raised, it prevents the use of conventional solid wedges, which are typically required in PAUT to steer the ultrasonic beams effectively. While mechanically blending the weld surface is an option, this additional manufacturing step increases production time and cost, making it an inefficient solution.
To overcome this challenge, localized immersion systems have been developed to provide consistent coupling between the PAUT probe and the weld surface. In this method, each PAUT probe is encased in a sealed cavity filled with water, which serves as the coupling medium. This water-based coupling technique eliminates the need for solid wedges and allows ultrasonic waves to penetrate the weld with minimal interference, ensuring accurate defect detection despite the weld’s surface irregularities.
By utilizing high-frequency probes and localized immersion coupling, PAUT has been successfully adapted to the complex geometries and thin-walled structures of aerospace friction stir welds. These advancements enhance inspection accuracy, repeatability, and efficiency, making PAUT a reliable and effective solution for ensuring weld integrity in aerospace applications.
Q: Are there any recent advances in PAUT testing techniques and technology that are useful when inspecting stir welds?
In recent years, Phased Array Ultrasonic Testing (PAUT) has seen significant advancements that enhance its effectiveness in inspecting friction stir welds (FSW). Emerging techniques such as Full Matrix Capture (FMC) and Total Focusing Method (TFM) have brought substantial improvements in imaging resolution, making it easier to detect small, volumetric, and crack-like defects that could compromise aerospace weld integrity.
FMC and TFM significantly improve resolution and defect characterization, offering a clearer and more detailed view of the weld structure compared to conventional PAUT techniques. However, despite its advantages, adoption has been somewhat limited due to two key factors:
- Standardization of PAUT in Aerospace: Many aerospace manufacturers have well-established PAUT protocols that require formal validation before transitioning to new methods.
- Slower Scanning Speed: FMC-TFM techniques generally have a lower acquisition speed, often reducing inspection velocity to half that of conventional PAUT. This slowdown can impact overall production efficiency, particularly in high-throughput environments.
A promising variation of FMC-TFM is Plane Wave Imaging (PWI), which retains the enhanced image quality of TFM while significantly reducing inspection time. In some cases, PWI has demonstrated inspection speeds faster than traditional PAUT, making it a potential game-changer for aerospace FSW applications. As PWI technology matures, its adoption in the industry will be closely monitored to determine its long-term impact on weld inspection efficiency and accuracy.
Another breakthrough within the FMC-TFM family is Phase Coherence Imaging (PCI), which enhances the ability to detect small volumetric and crack-like defects. PCI improves flaw visibility by enhancing the coherence of reflected signals, making it particularly useful for identifying fine cracks and subtle discontinuities within FSW joints.
However, PCI does come with a trade-off:
- Reduced Sensitivity to Large Flat Defects: Unlike conventional PAUT and TFM, PCI is less effective at detecting large planar flaws, such as delamination. Additionally, its ability to perform thickness assessment is limited, making it more suitable for flaw characterization than general weld geometry evaluation.
Q: Are there any future improvements to PAUT techniques and technology that will be more useful when inspecting stir welds?
Currently, PAUT data interpretation remains heavily reliant on human inspectors, who manually screen and analyze weld images for potential defects. While dedicated software tools assist in processing data, the screening process remains time-intensive and is inherently subject to human variability in interpretation.
The next major leap in PAUT technology is expected to be the integration of artificial intelligence (AI) and machine learning algorithms into weld inspection workflows. AI-powered defect recognition models could:
- Automated defect classification, significantly reducing manual analysis time.
- Improve consistency, eliminating the variability introduced by different inspectors.
- Identify subtle defect patterns that may be overlooked in conventional analysis.
- Provide real-time feedback, enhancing in-line inspection efficiency for aerospace manufacturers.
While AI-driven PAUT analysis is still in its early stages, research and development efforts are actively working toward full qualification of AI models for aerospace applications. Over the next few years, we can expect AI-assisted PAUT interpretation to become increasingly reliable and widely adopted, complementing human inspectors and accelerating the overall quality control process.
Another key area of future improvement lies in further automation of the inspection process. While PAUT scanning has already transitioned from manual operation to automated and robotic systems, future developments will focus on:
- Fully integrated robotic PAUT solutions that automatically adjust probe positioning in real time for complex aerospace geometries.
- Faster data acquisition techniques, reducing inspection cycle times without compromising image resolution.
- More advanced imaging algorithms, enhancing real-time defect visualization and characterization.
The long-term evolution of PAUT is likely to align with Industry 4.0, where big data analytics and cloud-based processing will enhance predictive maintenance strategies. By combining historical PAUT inspection data with AI-driven predictive models, manufacturers could:
- Identify trends in defect formation, optimizing FSW process parameters for better weld quality.
- Predict potential failure points before defects become critical, reducing rework and improving production efficiency.
- Integrate real-time PAUT data with digital twin simulations, allowing engineers to assess weld performance under simulated operating conditions.